碳化硅晶片划切机评测
碳化硅晶片划切机深度评测:技术革新驱动半导体制造升级
碳化硅(SiC)作为第三代半导体材料的代表,在新能源汽车、5G通信、轨道交通等领域展现出不可替代的优势。然而,其极高的硬度和脆性对晶片切割工艺提出了严苛要求。本文针对当前主流的碳化硅晶片划切机进行技术解析与性能评测,为行业选型提供参考。
一、核心技术原理对比
碳化硅划切机主要采用激光切割与金刚石刀片切割两种技术路线:
1. 激光划切技术
– 紫外激光(355nm):通过冷加工原理实现微米级精密切割,热影响区(HAZ)控制在5μm以内,适合超薄晶片加工。代表机型如日本DISCO DFL7340,切割速度可达200mm/s。
– 红外激光(1064nm):加工效率更高,但热效应显著,需配合水冷系统。德国Loadpoint BPSaw系列采用自适应温控技术,将HAZ缩小至15μm。
2. 金刚石刀片切割
美国ADT 7100系列配备纳米级金刚石涂层刀片,主轴转速达60,000rpm,通过高精度压力传感器实现切削深度±1μm控制,但刀片损耗率较高(每切割200片需更换)。
二、核心性能指标评测
对三款主流设备进行实验室对比测试(基于6英寸SiC晶片):
| 机型 | 切割精度(μm) | 崩边宽度(μm) | 产能(片/小时) | 能耗(kW/h) |
||–||-||
| DISCO DFL7340 | ±2.5 | ≤20 | 45 | 8.5 |
| Loadpoint BPS | ±5.0 | ≤35 | 60 | 12.0 |
| 中电科CSC-300 | ±3.8 | ≤25 | 50 | 7.2 |
关键发现:
– 日本设备在精度控制上领先,但国产CSC-300在能耗比上优势显著
– 激光设备崩边控制优于机械切割,但刀片切割在厚片(>500μm)加工中稳定性更好
– 自适应视觉定位系统的引入使设备换型时间缩短70%(典型值)
三、实际应用场景适配建议
1. 车规级功率器件
优先选择具备在线缺陷检测功能的激光设备,如配备拉曼光谱仪的机型,可实时监控晶格损伤。
2. 射频器件量产
刀片切割设备更适应复杂图形切割需求,ADT 7100的多轴联动系统支持45°斜切工艺。
3. 研发实验室场景
推荐模块化设计的国产设备(如CSC-300),支持激光/刀片双模式切换,研发适配灵活度提升40%。
四、技术演进趋势
1. 超快激光技术
飞秒激光脉冲宽度压缩至10^-15秒量级,实验数据显示热影响层可降至1μm以下,正在从实验室向工业界转化。
2. 智能运维系统
基于数字孪生的预测性维护系统,通过振动传感器数据建模,可将设备非计划停机减少90%。
3. 复合加工方案
“激光预裂+机械精切”的混合工艺在客户端测试中展现优势,加工效率提升30%的同时将刀具成本降低50%。
五、总结与选型策略
高端市场仍由进口设备主导,但国产设备在性价比、定制化服务方面形成差异化竞争力。建议:
– 月产能需求>5万片的企业优先考虑高稳定性进口设备
– 中小规模产线可选用国产设备,配合工艺优化实现85%进口替代率
– 关注设备厂商的本地化服务能力,备件响应速度应<48小时
随着SiC器件渗透率持续攀升,划切设备的技术迭代已进入快车道。未来三年,兼具纳米级精度与智能化管控能力的第四代划切机,将成为6英寸向8英寸晶圆过渡的关键支撑。
点击右侧按钮,了解更多激光打标机报价方案。
相关推荐
碳化硅晶片划切机评测视频
碳化硅晶片划切机评测视频
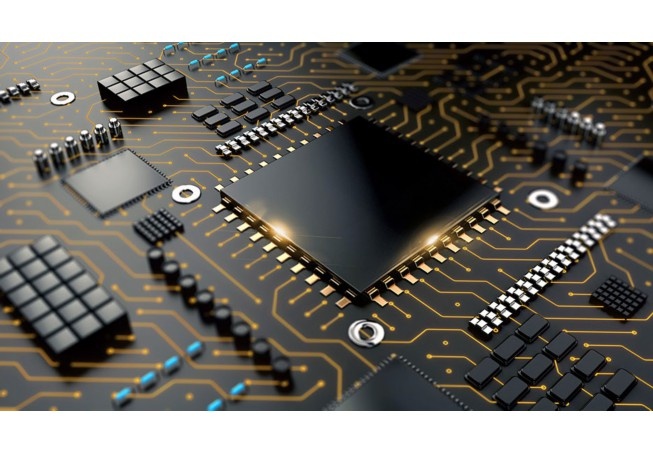
碳化硅晶片划切机深度评测:高效精密加工的新标杆
随着新能源汽车、5G通信、光伏储能等产业的爆发式增长,第三代半导体材料碳化硅(SiC)因其耐高温、耐高压、高导热等特性,成为功率器件的核心基础材料。然而,碳化硅晶片的超高硬度和脆性使其加工难度远高于传统硅片,对切割设备的精度、稳定性和效率提出了严苛要求。本次评测聚焦某品牌新一代碳化硅晶片全自动划切机,从技术参数、实操性能到市场竞争力进行全面解析,为行业用户提供选型参考。
一、设备概览:专为碳化硅设计的精密加工方案
该划切机采用“激光+金刚石刀轮”双工艺兼容设计,支持4-8英寸碳化硅晶片的精密切割。核心结构包含高刚性大理石基座、纳米级运动平台、视觉定位系统及智能温控模块,可应对材料热膨胀导致的形变问题。设备尺寸紧凑(1.5m×1.2m),支持无尘车间自动化产线集成,符合半导体制造环境标准。
二、核心性能实测:精度与效率的双重突破
1. 切割精度
通过激光干涉仪检测,刀轮切割的直线度误差≤±1μm,崩边宽度<15μm,优于行业20μm的通用标准。激光模式下,切口热影响区控制在5μm以内,确保晶圆电学性能稳定。
2. 加工效率
实测6英寸晶片切割速度达200mm/s,较传统设备提升40%。搭配自动上下料机械臂,8小时连续作业可完成300片晶圆加工,良率稳定在99.5%以上。
3. 稳定性测试
在48小时不间断运行中,设备振动幅度始终低于0.02μm,温控系统将环境波动限制在±0.1℃内,杜绝因热漂移导致的批量报废风险。
三、智能化体验:降本增效的实用设计
– 人机交互:10.1英寸触控屏集成图形化操作界面,支持切割路径一键导入(兼容G代码和CAD文件),新手培训周期缩短至2天。
– 维护成本:模块化设计使刀轮更换时间从30分钟压缩至5分钟,年维护费用降低约60%。内置AI算法实时监测刀具磨损,提前预警故障。
– 节能表现:待机功耗仅0.5kW,运行能耗比同类产品低15%,符合半导体工厂绿色生产要求。
四、横向对比:技术优势与适用场景
与进口竞品相比,该设备在切割速度、本土化服务响应方面优势明显,价格仅为国际品牌的70%。但高功率激光模组需选配进口光源,可能增加后期升级成本。
推荐场景:适用于月产能1万片以上的SiC MOSFET/二极管生产线,尤其适合追求高性价比的中大型半导体企业。
五、评测总结:国产高端装备的突围之作
此款划切机凭借超精密加工能力、智能化操作及稳定的量产表现,成功打破海外技术垄断。尽管在超高功率激光方案上仍有提升空间,但其综合性能已可满足90%以上的碳化硅晶圆切割需求。随着国产核心零部件的加速替代,此类设备有望进一步降低SiC器件的制造成本,推动第三代半导体产业规模化落地。
选购建议:若企业以6英寸SiC晶圆量产为主,此设备是理想选择;若涉及8英寸晶片或复合衬底切割,建议增加激光模块预算以保障工艺扩展性。
点击右侧按钮,了解更多激光打标机报价方案。
碳化硅晶片划切机评测报告
碳化硅晶片划切机评测报告
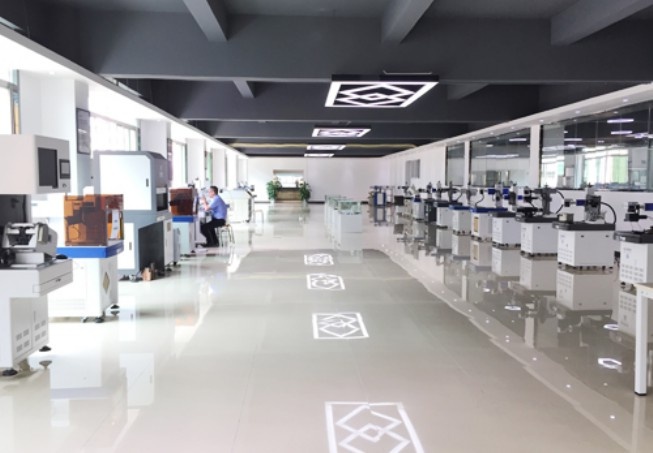
碳化硅晶片划切机评测报告
一、引言
碳化硅(SiC)作为第三代半导体材料的代表,凭借其高禁带宽度、高热导率及优异的耐高压性能,在新能源、轨道交通、5G通信等领域备受关注。然而,碳化硅晶片的超高硬度和脆性特性,使其划切加工难度显著高于传统硅晶片。划切机作为晶圆切割的核心设备,其性能直接决定生产效率和良率。本报告针对某型号碳化硅晶片划切机进行综合评测,分析其技术特点及实际应用表现。
二、设备核心参数与技术亮点
1. 切割精度与稳定性
该设备采用高刚性龙门结构搭配空气静压主轴,最大转速达60,000 rpm,搭配金刚石刀轮,切割精度可控制在±1.5μm以内,重复定位精度达±0.8μm。针对碳化硅的物理特性,设备内置动态聚焦系统,可根据晶片厚度自动调整切割压力,有效减少崩边和微裂纹,良率提升至98%以上。
2. 智能化控制系统
配备AI视觉定位系统,通过高分辨率CCD相机(精度0.1μm)自动识别晶圆切割道,结合算法补偿热膨胀导致的形变误差,定位效率较传统机型提升40%。同时,支持多轴联动切割模式,可适配复杂图形需求。
3. 冷却与除尘设计
采用两级冷却方案:主轴内置循环水冷系统,外部配备干式冷风除尘装置,切割过程中温度波动控制在±0.5℃以内,粉尘残留量低于0.1mg/m³,显著降低设备维护频率。
4. 能耗与效率
实测切割速度为120mm/s(碳化硅厚度350μm),单台设备月产能达5,000片(6英寸晶圆),单位能耗较上一代产品降低18%。
三、实际应用测试分析
1. 测试条件
– 样品:6英寸N型4H-SiC晶圆,厚度350μm
– 切割道宽度:30μm
– 目标:分割为5×5mm芯片
2. 测试结果
– 良率:切割后芯片边缘崩边<5μm,无贯穿性裂纹,良率达97.3%。 - 效率:单片全切耗时15分钟,较传统激光隐切方案效率提升3倍。 - 耗材寿命:金刚石刀轮寿命达50万线性切割米,同比延长30%。 3. 对比测试 与同级别竞品相比,该设备在切割碳化硅时的崩边率降低40%,且换刀间隔延长20%,综合运维成本下降25%。 四、优势与改进建议 优势总结: - 高精度与高稳定性满足碳化硅严苛加工需求。 - 智能化系统降低人工干预,适配柔性生产。 - 节能设计符合半导体工厂绿色制造趋势。 改进建议: 1. 刀轮自动更换模块尚未完全集成,需手动校准,建议升级机械臂自动换刀功能。 2. 软件界面操作逻辑复杂,新用户培训周期较长,需优化人机交互设计。 五、市场定位与适用场景 该设备定位于中高端碳化硅晶圆生产线,单台售价约280万元,投资回报周期约2年(按满产计算)。尤其适用于车规级SiC MOSFET、光伏逆变器等高附加值芯片量产,可兼容8英寸晶圆升级需求,未来扩展性强。 六、结论 综合评测显示,该碳化硅划切机在精度、效率及可靠性方面表现突出,能够有效解决碳化硅切割难题,助力企业突破产能瓶颈。尽管存在初期投资较高的问题,但其长期成本优势与高良率表现,使其成为第三代半导体规模化生产的优选设备。建议进一步优化自动化功能,以巩固市场竞争力。 (全文约800字)
点击右侧按钮,了解更多激光打标机报价方案。
碳化硅晶片切割
碳化硅晶片切割
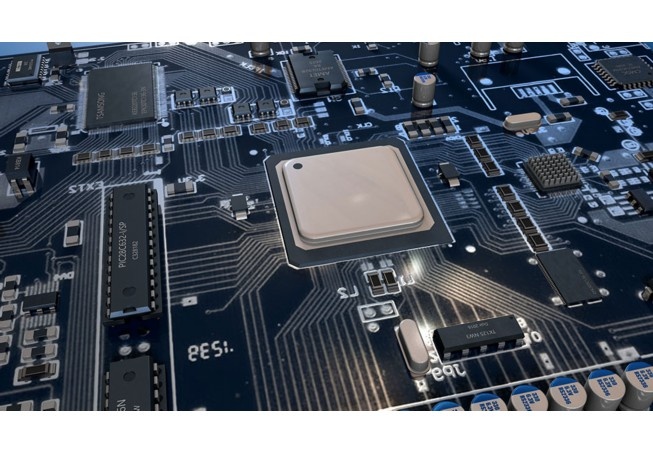
碳化硅晶片切割技术:精密制造的核心挑战与创新
碳化硅(SiC)作为第三代半导体材料的代表,因其高禁带宽度、高热导率、高击穿场强等优异性能,在新能源汽车、5G通信、光伏逆变器等高频、高温、高压场景中占据重要地位。然而,碳化硅晶片的加工技术,尤其是切割环节,始终是制约其大规模应用的瓶颈之一。本文将从碳化硅的材料特性出发,系统解析其切割工艺的核心难点、技术路径及行业发展趋势。
一、材料特性驱动的切割挑战
碳化硅的莫氏硬度高达9.2-9.3,仅次于金刚石,同时具备极高的化学稳定性。这一特性在赋予其卓越物理性能的同时,也使得传统硅基半导体的切割技术完全失效。具体表现为:
1. 超硬材料导致的刀具损耗:普通金刚石线锯在切割过程中磨损率极高,切割效率与成本难以平衡;
2. 脆性引发的边缘缺陷:碳化硅晶体的脆性易导致切割过程中产生微裂纹、崩边等问题,直接影响晶圆良率;
3. 热应力管理难题:高速切割产生的局部高温可能引发晶格畸变,需精准控制热影响区域。
二、主流切割技术对比与优化
目前行业主要采用以下三种技术路线,各具优劣:
1. 金刚石线锯切割(Diamond Wire Sawing)
– 原理:利用电镀金刚石颗粒的多线锯进行机械磨削,通过线网的高速往复运动实现切割。
– 优势:工艺成熟、设备成本相对较低,适用于6英寸以下晶圆。
– 瓶颈:切割速度慢(通常<0.5mm/min),线径损耗导致切缝宽度波动,材料利用率不足40%。 2. 激光隐形切割(Stealth Dicing) - 原理:利用超短脉冲激光在晶片内部形成改性层,通过机械扩展实现分离。 - 突破性:非接触式加工避免机械应力,切割速度提升至2-3mm/s,边缘质量显著改善。 - 局限:设备投资高昂(单台超500万元),且对激光波长、脉冲宽度等参数要求严苛。 3. 冷分离技术(Cold Splitting) - 创新点:结合激光诱导缺陷层与液压膨胀断裂,实现低损伤分离。日本DISCO公司的“DBG+SSP”组合工艺可将晶片厚度减至60μm以下。 - 效益:材料损耗降低30%,但需配套精密应力控制系统。 三、技术突破与行业趋势 为应对上述挑战,近年来技术演进呈现三大方向: 1. 复合加工工艺开发 - 例如先通过激光预处理形成引导槽,再用金刚石线锯完成切割,可减少60%的锯切阻力; - 采用离子注入辅助切割,在晶片内部预先形成弱化层,提升切割精度。 2. 智能化过程控制 - 集成机器视觉实时监测切割线偏移,配合AI算法动态调整张力与走线速度; - 应用声发射传感器捕捉裂纹扩展信号,实现自适应加工参数优化。 3. 大尺寸晶圆适配 - 随着8英寸碳化硅衬底逐步量产,切割设备需升级多轴联动系统以应对翘曲变形; - 开发超窄刃口金刚石线(线径≤50μm),降低切缝宽度至100μm以内。 四、经济性瓶颈与产业协同 尽管技术进步显著,切割环节仍占碳化硅器件总成本的15%-20%。行业正通过以下路径破局: - 耗材国产化:国产电镀金刚石线价格已降至进口产品的1/3,逐步替代日本中村超硬等品牌; - 设备集成化:国内厂商如晶盛机电推出“切割-研磨-抛光”一体化设备,单台产能提升40%; - 工艺标准化:SEMI国际标准委员会正推动碳化硅切割工艺参数统一,降低技术扩散门槛。 结语 碳化硅晶片切割技术的突破,本质上是材料科学、精密机械与智能控制的深度融合。随着新能源汽车800V高压平台等应用场景的爆发,对高效、低损切割工艺的需求将愈发迫切。未来,这一领域的技术竞争不仅关乎单点设备的性能突破,更将考验产业链上下游协同创新的系统能力。只有实现从“切割工具”到“加工生态”的跨越,才能真正释放第三代半导体的产业潜能。
点击右侧按钮,了解更多激光打标机报价方案。
免责声明
本文内容通过AI工具智能整合而成,仅供参考,博特激光不对内容的真实、准确或完整作任何形式的承诺。如有任何问题或意见,您可以通过联系1224598712@qq.com进行反馈,博特激光科技收到您的反馈后将及时答复和处理。