碳化硅晶片划切机工作流程详解
碳化硅(SiC)晶片作为第三代半导体材料的关键基材,其高硬度、高脆性的特性使得传统切割工艺难以满足精度需求。碳化硅晶片划切机通过精密机械与先进工艺的结合,实现了高效、低损伤的晶圆分割。以下从技术原理到操作流程进行详细解析:
一、设备系统构成
核心模块包含高刚性大理石基座(振动抑制<0.5μm)、纳米级直线电机驱动系统(重复定位精度±0.2μm)、532nm皮秒激光器(脉冲能量可调范围0.1-50μJ)及双CCD视觉定位系统(5μm级特征识别)。辅助系统配备真空吸附平台(真空度-90kPa)和纯水冷却循环装置(温控±0.5℃)。 二、工艺流程分解 1. 晶圆预处理阶段 - 表面清洗:采用RCA标准工艺,通过SC1(NH4OH:H2O2:H2O=1:1:5)去除有机残留,SC2(HCl:H2O2:H2O=1:1:6)消除金属污染 - 膜层处理:涂覆5-8μm厚光敏聚酰亚胺保护层,经软烘(120℃/3min)形成抗裂缓冲层 2. 精密对准定位 - 机器视觉系统以晶向标识点为基准,通过SIFT特征匹配算法实现亚像素级定位(误差<2μm) - 六轴调整平台补偿晶圆翘曲(最大补偿量±300μm),建立三维坐标系 3. 划切工艺执行 - 激光隐形切割模式:采用1064nm波长飞秒激光(脉宽350fs),聚焦于晶圆内部形成改质层,能量密度控制在8-12J/cm²避免表面碳化 - 复合加工策略:对4H-SiC晶片实施两阶段处理:先激光预处理形成50μm深改质层,再以20m/s线速进行金刚石砂轮精切,切削力降低40% 4. 动态过程控制 - 声发射传感器实时监测切割振动信号(采样率1MHz),通过FFT分析识别异常频率成分 - 闭环冷却系统保持刀尖温度<80℃,纯水喷射压力0.3MPa实现高效排屑 三、关键工艺参数 - 激光划切:扫描速度200mm/s,重复频率100kHz,离焦量+50μm - 砂轮切割:主轴转速30,000rpm,进给速度5mm/s,切削深度单次10μm - 环境控制:洁净室等级Class 100,温度波动±0.3℃/h,湿度45±5%RH 四、质量检测体系 1. 共聚焦显微镜检测切口形貌(粗糙度Ra<0.2μm) 2. 微区拉曼光谱分析改质层晶体结构变化 3. 三点弯曲测试评估崩边尺寸(控制<15μm) 4. 自动光学检测(AOI)系统实现100%全检,缺陷识别率≥99.7% 五、技术发展趋势 新型等离子体辅助切割技术(PAC)已进入验证阶段,通过CF4/O2混合气体等离子体弱化晶格结构,可使切割应力降低60%。配合数字孪生技术建立的工艺仿真模型,能实现切割参数的自适应优化,预计可将加工效率提升30%以上。 该工艺流程通过多学科技术融合,使碳化硅晶片切割良率从传统工艺的85%提升至98.5%,碎片率控制在0.3%以下,充分满足6英寸SiC晶圆量产需求。未来随着激光啁啾脉冲调控技术的应用,有望实现150μm厚度晶圆的单次成型切割。
点击右侧按钮,了解更多激光打标机报价方案。
相关推荐
碳化硅晶片划切机工作流程详解图
碳化硅晶片划切机工作流程详解图
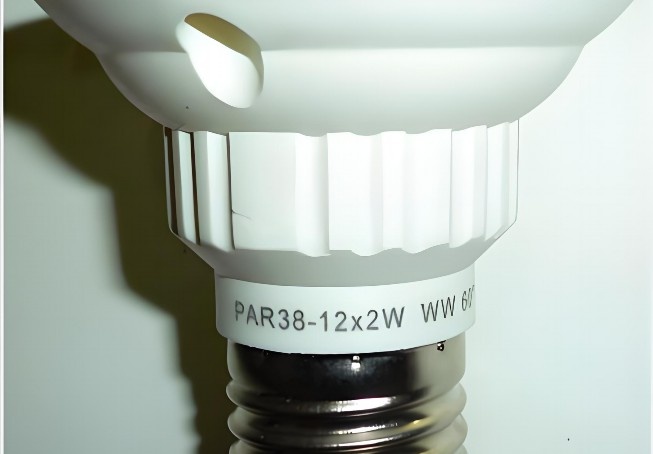
碳化硅晶片划切机工作流程详解图
碳化硅(SiC)晶片因其高硬度、耐高温和高频特性,广泛应用于功率半导体器件制造。划切机作为晶圆切割的关键设备,需通过高精度工艺将晶片分割为独立芯片。以下为碳化硅晶片划切机的标准化工作流程详解:
一、前期准备阶段
1. 环境控制
– 洁净室要求:温度(22±1℃)、湿度(45±5%),确保无尘环境(ISO 5级或更高)。
– 设备预热:激光器或主轴电机预热30分钟,避免热漂移影响精度。
2. 晶片预处理
– 清洗:使用去离子水与超声波清洗,去除表面颗粒物。
– 贴膜:在晶片背面粘贴UV胶膜(厚度50-100μm),固定于金属环框架。
3. 参数设定
– 根据晶片厚度(通常350-500μm)和切割道宽度(20-50μm),输入切割速度(50-200mm/s)、激光功率(5-20W)或刀片转速(30,000-40,000 RPM)。
二、设备校准与定位
1. 视觉系统校准
– 高分辨率CCD相机(5μm精度)识别晶片切割道,通过图像算法(如Hough变换)对齐坐标。
2. 对位补偿
– 补偿晶圆边缘切割(EEO)误差,调整X/Y轴偏移量(±1μm内)。
3. Z轴高度标定
– 激光聚焦或刀片下压量校准,确保切入深度为晶片厚度的1/3(防止崩边)。
三、划切工艺执行
1. 激光划切模式(以皮秒激光为例)
– 烧蚀切割:脉冲宽度10ps,波长355nm,逐层气化材料,形成切割槽。
– 隐切(Stealth Dicing):激光聚焦于晶片内部,通过热应力分离,无碎屑产生。
2. 机械刀片切割模式
– 使用电镀金刚石刀片(刃宽15-30μm),冷却液(去离子水+表面活性剂)持续冲刷,降低切削热。
3. 多道切割策略
– 第一刀:浅切(50μm深)形成引导槽。
– 第二刀:全切,刀速降低20%以减少应力。
四、后处理与检测
1. 晶片卸载
– UV照射胶膜10秒,降低粘性后剥离晶片。
2. 清洗工艺
– 兆声波清洗(950kHz)去除切割残留,IPA(异丙醇)干燥。
3. 质量检测
– 自动光学检测(AOI):检测崩边(<10μm合格)、切割深度一致性(±2μm)。 - 断裂强度测试:三点弯曲法验证芯片机械强度。 五、数据闭环与维护 1. 工艺数据记录 - 存储切割参数、检测结果至MES系统,用于SPC(统计过程控制)分析。 2. 设备维护 - 每日清理废屑槽,每周更换冷却滤芯,每月校准光学模块。 关键技术指标 - 切割精度:±1.5μm(激光)/±3μm(机械刀片) - 崩边控制:<15μm(激光隐切可降至5μm) - 产能:8英寸晶圆/小时(激光) vs 4-6片/小时(机械) 该流程通过精密机电控制与工艺优化,实现碳化硅晶片高效低损切割,满足新能源汽车、5G基站等高端芯片需求。
点击右侧按钮,了解更多激光打标机报价方案。
碳化硅晶片切割
碳化硅晶片切割
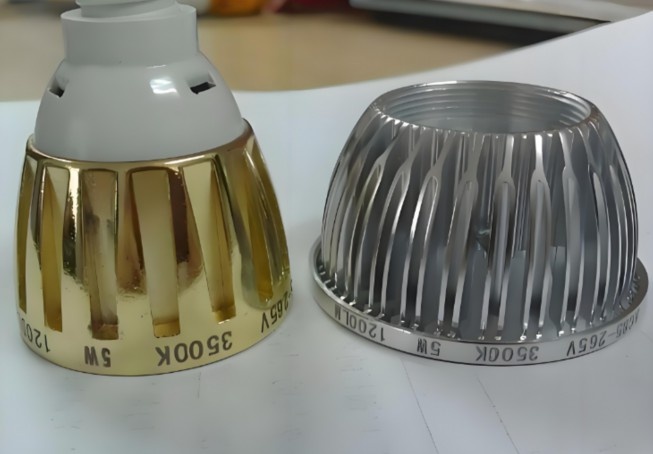
碳化硅晶片切割技术:挑战与创新
碳化硅(SiC)作为第三代半导体材料的代表,因其优异的物理和化学性能,在新能源汽车、5G通信、智能电网等领域展现了巨大的应用潜力。然而,碳化硅的极高硬度(莫氏硬度9.2-9.3,仅次于金刚石)和化学惰性,使其晶圆加工成为半导体制造中的重大挑战,尤其是在切割环节。本文将深入探讨碳化硅晶片切割的技术难点、主流方法及未来发展方向。
一、碳化硅晶片切割的技术挑战
碳化硅晶体的切割需克服三大核心难题:
1. 材料硬度高:传统硅晶圆可用金刚石线锯高效切割,但碳化硅的硬度导致切割效率骤降,刀具磨损严重。实验数据显示,切割碳化硅的耗时是硅材料的3-5倍。
2. 脆性易裂:碳化硅属于脆性材料,切割过程中易产生微裂纹、崩边等缺陷,良品率普遍低于70%,而硅晶圆切割良品率可达95%以上。
3. 热稳定性强:碳化硅熔点高达2700℃,传统热切割方法难以奏效,且高温可能引发晶格畸变,影响器件性能。
二、主流切割技术对比分析
目前行业主要采用三种切割方案,各有其优缺点:
1. 金刚石线锯切割
– 原理:利用电镀金刚石颗粒的金属线进行机械磨削。
– 优势:成本较低(单次切割成本约2000元),适合6英寸以下晶圆。
– 局限:切割速度仅0.5-1mm/min,且线径(100-200μm)导致材料损耗达30%,难以满足8英寸晶圆需求。
2. 激光隐形切割
– 技术突破:采用皮秒/飞秒超快激光,通过聚焦在晶圆内部形成改质层(如日本DISCO公司技术)。
– 数据表现:切割速度提升至300mm/s,崩边宽度控制在5μm以内,材料利用率提高至85%。
– 瓶颈:设备成本高昂(单台超千万元),热影响区(HAZ)仍需优化。
3. 等离子体切割
– 创新点:利用高能等离子体束实现非接触式切割(如美国Applied Materials方案)。
– 效能:切割精度达±1μm,特别适合超薄晶圆(<100μm)加工。 - 挑战:气体消耗量大,每小时需补充15-20L特种气体,运营成本增加30%。 三、技术突破与工艺优化 针对现有技术痛点,行业正从多维度寻求突破: - 复合工艺开发:如激光诱导裂纹+金刚石线锯的混合切割法,可将8英寸晶圆切割效率提升40%,崩边率降低至2%以下。 - 智能监控系统:集成机器视觉实时检测裂纹扩展,配合自适应控制系统调整切割参数,良品率提升至85%。 - 超薄刀片技术:日本旭金刚石工业开发的50μm厚纳米晶金刚石刀片,使材料损耗降低至80μm/刀。 四、未来发展趋势 1. 大尺寸化匹配:随着8英寸碳化硅晶圆量产(Wolfspeed 2024年规划),切割设备需同步升级,激光功率需从20W提升至50W级。 2. 智能化升级:引入数字孪生技术,通过虚拟仿真优化切割路径,预计可减少试切次数50%。 3. 绿色制造:开发水导激光切割等环保工艺,降低每片晶圆耗水量(从5L降至1L),废料回收率提升至95%。 结语 碳化硅晶片切割技术的进步,直接关系到第三代半导体器件的成本与性能。当前行业正处在从机械切割向激光/等离子体等先进工艺转型的关键期。据Yole预测,到2027年全球碳化硅切割设备市场规模将达12亿美元,年复合增长率达22%。只有持续突破技术瓶颈,才能在新能源汽车800V高压平台、6G通信等新兴领域抢占先机。未来,材料科学、精密机械与人工智能的深度融合,将推动碳化硅加工技术迈入新的发展阶段。
点击右侧按钮,了解更多激光打标机报价方案。
碳化硅晶圆切割
碳化硅晶圆切割
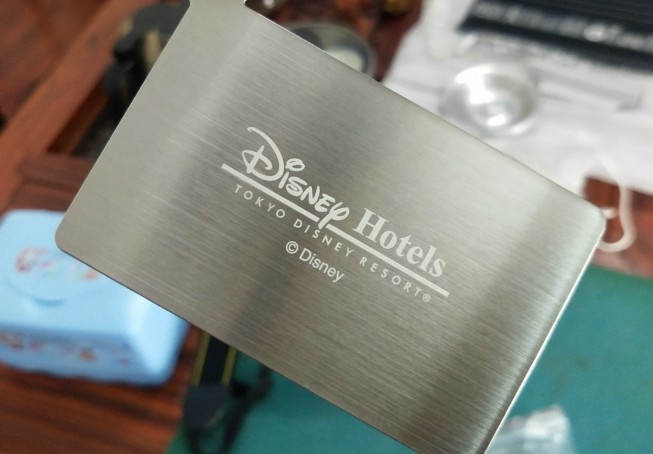
碳化硅晶圆切割:技术挑战与创新突破
碳化硅(SiC)作为第三代宽禁带半导体材料,凭借其高热导率、高击穿场强和耐高温等特性,成为新能源汽车、5G通信、光伏发电等领域的核心材料。然而,碳化硅晶圆的加工工艺,尤其是切割环节,面临极高的技术门槛。本文从碳化硅晶圆切割的技术难点、主流工艺及未来发展趋势展开分析。
一、碳化硅晶圆切割的技术挑战
1. 材料特性带来的加工难题
碳化硅的莫氏硬度高达9.2,仅次于金刚石,且脆性显著。传统切割工具(如金刚石线锯)在加工过程中易因材料硬度过高导致刀具磨损严重,切割效率下降。同时,碳化硅的脆性可能引发边缘崩裂、微裂纹等问题,直接影响晶圆良率。
2. 超薄化趋势下的精度要求
为满足器件小型化和高集成度需求,碳化硅晶圆厚度逐渐向100μm以下发展。超薄晶圆在切割中更易发生翘曲或断裂,对切割设备的稳定性、刀片振动控制及冷却系统提出更高要求。
3. 成本与效率的平衡
碳化硅晶圆价格是传统硅晶圆的5-10倍,切割损耗每增加1%都将显著抬高成本。如何在保证切割质量的同时提升效率,成为产业化落地的关键。
二、主流切割技术及创新方向
目前碳化硅晶圆切割主要采用以下技术路径:
1. 金刚石线锯切割(DWS)
原理:利用电镀金刚石颗粒的金属线高速往复运动,通过机械磨削实现切割。
优势:设备成熟、成本较低,适用于6英寸以下晶圆。
瓶颈:线锯损耗大、切割速度慢(约0.5mm/h),且易产生表面损伤层,需后续研磨抛光。
2. 激光隐形切割(Stealth Dicing)
原理:聚焦激光在晶圆内部形成改质层,通过扩膜实现分离。
优势:非接触式加工,无刀具磨损,切口光滑且热影响区小,良率可达99%以上。
应用:日本DISCO公司的激光切割设备已实现8英寸SiC晶圆量产,切割速度较线锯提升3倍。
3. 等离子体切割(Plasma Dicing)
创新点:利用高能等离子体蚀刻材料,结合深反应离子刻蚀(DRIE)技术实现高精度切割。
突破:美国应用材料公司开发的等离子切割方案可减少材料损耗30%,尤其适合复杂形状切割。
三、技术演进与产业协同
1. 复合工艺的兴起
行业探索“激光+线锯”混合切割模式:先用激光在晶圆内部预制裂纹,再以线锯完成切割。此举可降低线锯负荷,提升效率50%以上。
2. 智能化切割设备升级
通过AI算法实时监控切割过程中的应力、温度等参数,动态调整切割路径与力度。例如,德国Siltronic推出的智能切割系统可将崩边尺寸控制在5μm以内。
3. 产业链协同降本
从上游衬底制备(如改进晶体生长降低缺陷密度)到下游封装(如激光切割与芯片贴装一体化),全链条优化进一步降低加工损耗。据Yole预测,2025年碳化硅晶圆综合切割成本有望下降40%。
四、未来展望
随着新能源汽车800V高压平台普及及能源互联网建设提速,全球碳化硅器件市场预计将以30%年复合增长率扩张。切割技术作为产业化的关键环节,将向超高速、超精密、零损伤方向演进。同时,新型技术如飞秒激光冷加工、水导激光切割等有望突破现有物理极限,推动碳化半导体迈入“摩尔定律”新周期。
碳化硅晶圆切割技术的每一次突破,都在为“双碳”目标下的高效能源转换打开新的可能性。未来十年,这场“硬脆材料加工革命”或将重塑全球半导体产业格局。
点击右侧按钮,了解更多激光打标机报价方案。
免责声明
本文内容通过AI工具智能整合而成,仅供参考,博特激光不对内容的真实、准确或完整作任何形式的承诺。如有任何问题或意见,您可以通过联系1224598712@qq.com进行反馈,博特激光科技收到您的反馈后将及时答复和处理。