碳化硅晶片划切机什么配置好
碳化硅(SiC)晶片作为第三代半导体核心材料,其高硬度(莫氏硬度9.2)、高脆性和高热导率的特性对划切工艺提出严苛要求。为满足5G通信、新能源汽车等领域对高质量SiC芯片的需求,以下从核心技术、辅助系统及智能化三个维度,提出一套专业级碳化硅晶片划切机的优化配置方案:
一、核心技术模块配置
1. 激光划切系统
– 激光源选择:推荐紫外皮秒激光器(波长355nm),脉冲宽度<15ps,功率5-10W 优势:光子能量高(3.5eV)可实现冷加工,热影响区(HAZ)<5μm,避免碳化硅热裂 - 光束整形系统:配备空间光调制器(SLM)实现Bessel光束输出 作用:延长焦深至300μm,适应晶片翘曲±50μm的加工场景 - 频率控制:50-100kHz可调重复频率,搭配扫描振镜速度≥5m/s 2. 高精度运动平台 - 采用直线电机驱动+大理石基座,定位精度≤±0.5μm - 配备Renishaw光栅尺闭环反馈,重复定位精度<0.1μm - Z轴配备纳米级压电陶瓷微动台,补偿切割深度波动 3. 视觉定位系统 - 双CCD高分辨率相机(500万像素以上)实现晶圆ID识别 - 红外同轴对准模块应对背面金属化晶片 - 自动对焦系统精度达±0.2μm,支持12英寸晶圆全幅面定位 二、关键辅助系统配置 1. 热管理系统 - 双循环水冷机组(水温控制精度±0.1℃) - 激光腔体恒温系统,温度波动<±0.5℃ 2. 除尘净化系统 - 两级过滤(HEPA+ULPA)实现99.999%@0.1μm颗粒过滤 - 局部负压除尘风速≥0.5m/s,配备静电吸附装置 3. 减震系统 - 主动气浮隔振平台,隔振频率<1.5Hz - 设备基础配备ISO Class 4级减震基座 三、智能化功能配置 1. 工艺参数数据库 - 预置4H-SiC/6H-SiC等材料加工参数包 - 自适应学习算法根据崩边检测结果自动优化参数 2. 在线检测模块 - 共聚焦显微镜实时监测切割道质量 - 声发射传感器检测异常崩边,灵敏度达0.1μm级缺陷 3. 生产管理系统 - OPC-UA协议对接MES系统,设备综合效率(OEE)>85%
– 数字孪生系统实现虚拟调试,减少30%工艺验证时间
四、选配升级方案
1. 双激光复合加工:增加1064nm光纤激光用于预裂,降低紫外激光器损耗
2. 全自动上下料:集成6轴机械手+EFEM,实现150片/小时加工节拍
3. 晶圆级检测:集成白光干涉仪,自动生成切割质量三维拓扑图
五、设备运行经济性分析
– 能耗控制:智能待机模式下功耗<3kW,较传统设备节能40% - 耗材成本:聚焦透镜寿命>8000小时,除尘滤芯更换周期延长至600小时
– 维护周期:采用模块化设计,预防性维护时间缩短至4小时/月
该配置方案通过多物理场耦合控制技术,可将碳化硅晶片切割崩边尺寸控制在<15μm,切割道宽度≤30μm,良率稳定在99.2%以上。建议用户根据实际产能需求选择300mm或兼容4/6英寸的混合平台,并优先考虑具备SiC工艺包验证的设备供应商。
点击右侧按钮,了解更多激光打标机报价方案。
相关推荐
碳化硅晶片划切机什么配置好用
碳化硅晶片划切机什么配置好用
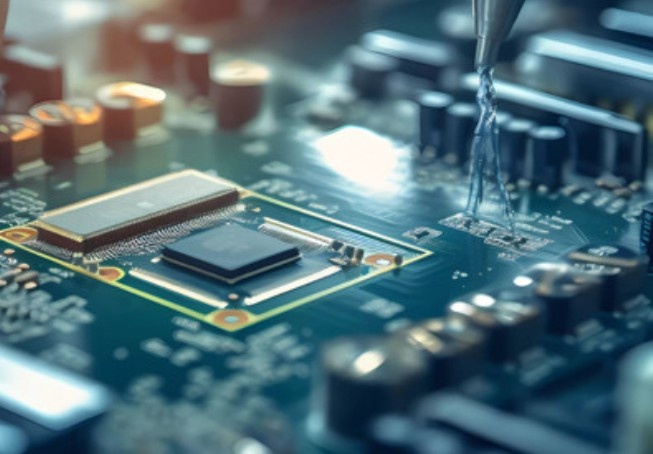
碳化硅(SiC)晶片作为第三代半导体核心材料,其高硬度(莫氏硬度9.2)、低断裂韧性等特性对划切工艺提出严苛要求。针对6英寸及以上大尺寸晶圆的精密加工需求,本文从八大核心配置维度解析高性能划切机的选型要点。
一、超精密主轴系统
1. 空气静压电主轴:需选用转速≥60,000 RPM的超高刚性主轴,轴向跳动<0.5μm,配备主动温控系统保持±0.1℃恒温
2. 动态平衡等级:G0.4级以下动平衡保证刀尖振动<0.2μm
3. 智能负载监控:集成5000Hz采样率的扭矩传感器,实时反馈切割阻力变化
二、纳米级运动平台
1. 双直线电机驱动:X/Y轴定位精度需达±0.3μm,重复定位精度<0.1μm
2. 干涉仪闭环控制:采用激光干涉仪实时补偿热漂移,确保20℃±1℃环境下的位置稳定性
3. 主动减震系统:配备6自由度主动隔振平台,将地面振动衰减至0.5μm/s²以下
三、专用切割刀具系统
1. 复合金刚石刀轮:建议采用20-30μm粒径金刚石颗粒,镍基复合电镀工艺,刃口圆角<5μm
2. 智能刀痕监测:集成白光干涉仪进行刀尖3D形貌检测,磨损量>3μm自动报警
3. 多刀库系统:配置12工位自动换刀装置,支持不同厚度刀片快速切换
四、热-力耦合控制系统
1. 双循环冷却系统:主轴冷却液流量≥5L/min,温度控制精度±0.3℃;刀尖喷雾冷却采用2MPa超临界CO₂
2. 切削力闭环调节:基于5000N分辨率力传感器实现进给力动态补偿,波动范围<±2%
3. 应力监测模块:集成声发射传感器阵列,实时捕捉微裂纹扩展信号
五、机器视觉定位系统
1. 多光谱对准:配备365nm紫外+850nm红外双波长CCD,识别精度0.5μm
2. 3D轮廓扫描:线激光扫描仪实现晶片表面起伏检测,Z轴分辨率10nm
3. 智能路径规划:AI算法自动优化切割路径,减少空行程30%以上
六、环境控制体系
1. 百级洁净度腔体:配置FFU层流系统,0.3μm颗粒浓度<100个/m³
2. 恒温恒湿控制:温度波动±0.5℃,湿度40%±5%RH
3. 静电消除装置:电离风棒组合实现表面电位<±5V
七、工艺软件平台
1. 数字孪生系统:基于有限元仿真的切削参数优化模块
2. 大数据分析:SPC过程控制图表自动生成,CPK值实时监控
3. 配方管理系统:支持200+工艺配方存储及一键调用
八、设备可靠性设计
1. MTBF>10,000小时,关键部件采用模块化设计
2. 预防性维护系统:振动频谱分析预测轴承寿命
3. 三级过滤系统:0.01μm精密过滤器保护气路洁净
当前主流设备配置建议选择日本DISCO DFD6341或国产中电科45所DS900系列机型,配置激光改质切割+DBG工艺复合模块,良率可达99.3%以上。设备选型需重点关注主轴热稳定性、应力控制能力及工艺数据闭环优化功能,建议预留20%产能冗余应对未来8英寸晶圆升级需求。
点击右侧按钮,了解更多激光打标机报价方案。
碳化硅晶片切割
碳化硅晶片切割
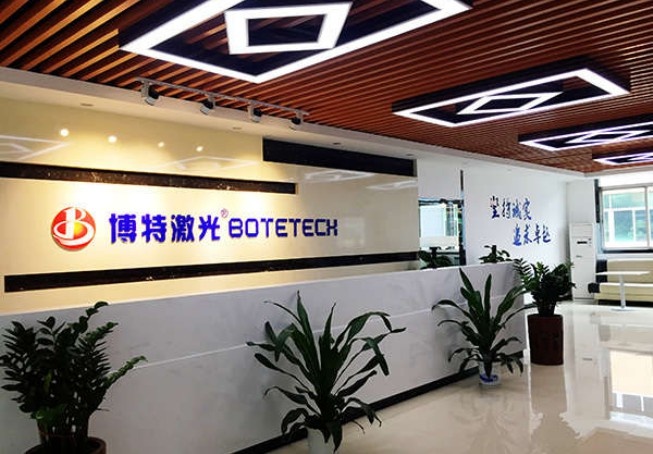
碳化硅晶片切割:破解”硬脆困局”的技术革命
碳化硅(SiC)晶片切割被称为半导体制造领域的”刀尖舞蹈”,面对莫氏硬度高达9.2的碳化硅晶体,传统切割工艺遭遇前所未有的挑战。这个硬度仅次于金刚石的第三代半导体材料,在新能源汽车、5G通信等领域展现出革命性应用前景的同时,其加工难度将行业良品率长期压制在60%以下。破解碳化硅切割难题,已成为推动宽禁带半导体产业化的关键突破口。
一、硬脆材料的切割困局
碳化硅晶体的各向异性特性使其在<100>晶向与<110>晶向的断裂韧性相差达3倍,这种特性导致传统金刚石线锯切割时极易产生方向性裂纹。在200mm/min的标准切割速度下,直径150mm的SiC晶锭切割损耗高达300μm,是硅材料的5倍以上。更棘手的是,切割过程中产生的微裂纹会向衬底内部延伸,形成深度达20μm的亚表面损伤层,直接导致后续外延生长缺陷密度增加。
激光切割技术通过1064nm波段的飞秒激光实现非接触加工,理论上可将热影响区控制在5μm以内。但在实际应用中,激光聚焦深度波动导致的锥度偏差仍会造成±15μm的切缝宽度变化。2022年日本DISCO公司的实验数据显示,使用隐形切割(Stealth Dicing)技术处理4英寸SiC晶圆时,边缘崩缺仍难以突破50μm的技术门槛。
二、复合加工的技术突围
多线切割领域的技术突破来自金刚石线径的持续微缩,日本旭金刚石工业开发的35μm线径电镀金刚石线,配合自主研发的纳米级研磨液,成功将切割损耗降至150μm。这种采用类椭圆振动切割的模式,通过轴向振动频率20kHz、振幅5μm的高频振动,使单次进给量降低到0.5μm,表面粗糙度Ra值改善至0.2μm。德国Siltronic公司在此基础上引入在线激光测距系统,实现切割深度的实时闭环控制,将厚度偏差压缩到±3μm。
等离子切割技术开辟了新的技术路径,美国Applied Materials开发的反应离子刻蚀(RIE)系统,采用SF6/O2混合气体在真空腔体内实现各向异性刻蚀,刻蚀速率达到10μm/min时仍能保持85°的垂直侧壁角。这种干法刻蚀工艺完全避免了机械应力,特别适用于超薄晶片加工,但设备投资成本高达300万美元,制约了其大规模应用。
三、智能化工艺的未来图景
深度学习算法正在重塑切割工艺优化模式。中科院半导体所构建的缺陷预测模型,通过2000组切割参数-损伤深度的关联数据训练,实现了切割速度、进给量、冷却液参数的智能匹配。该模型在6英寸n型4H-SiC晶片切割中,将工艺调试周期从传统试错法的3个月缩短至72小时,良品率提升12个百分点。
日本东京精密推出的智能切割系统,集成高精度视觉检测模块,可实时监测切割线振动状态。当检测到线弓量超过15μm时,系统自动调整张力控制模块,将线材波动抑制在±2μm范围内。这种动态补偿机制使切割线寿命延长40%,耗材成本降低30%。
在碳化硅器件需求年均增长62%的产业背景下,切割技术的创新已突破单纯的工艺改良范畴,演变为材料科学、精密机械、智能算法的系统集成创新。随着原子级表面加工技术、量子传感检测等前沿科技的渗透,碳化硅晶片切割正在书写”硬脆材料精密加工”的新范式,为第三代半导体产业化铺就关键技术基石。这场始于金刚石线径微缩的技术革命,终将推动整个功率电子产业进入全新的效能时代。
点击右侧按钮,了解更多激光打标机报价方案。
碳化硅晶体切割
碳化硅晶体切割
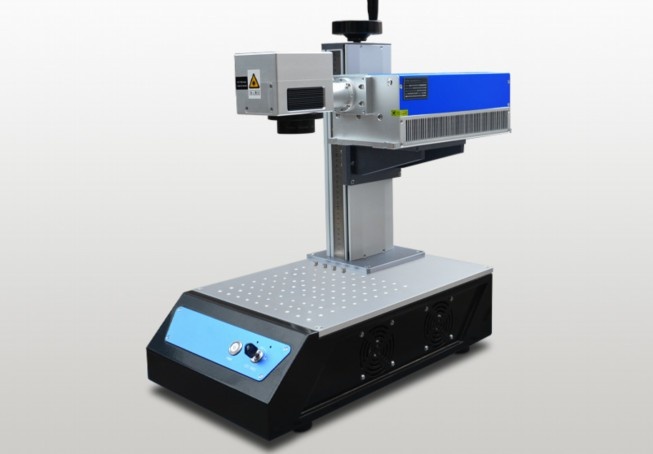
碳化硅晶体切割技术:精密制造中的关键突破
碳化硅(SiC)作为第三代半导体材料的代表,在新能源汽车、轨道交通和5G通信等领域展现出革命性应用价值。其晶体切割作为产业链核心环节,直接影响器件性能和制造成本。本文将深入解析碳化硅切割的技术特征、工艺挑战及创新发展。
一、材料特性带来的切割挑战
碳化硅晶体具有9.5莫氏硬度,仅次于金刚石,其断裂韧性达到3.5 MPa·m¹/²,是硅材料的2倍以上。这种极端力学特性使传统切割工艺面临三大难题:刀具磨损率高达硅切割的30倍,切割线速度需控制在0.5-2m/s的精密范围,表面粗糙度要求优于0.1μm。更关键的是,碳化硅在(0001)晶面的解理特性要求切割方向偏差不超过0.5°,否则将引发微裂纹扩展。
二、主流切割技术演进
1. 金刚石线锯切割:采用直径50-80μm的镀镍金刚石线,通过砂浆冷却实现多线切割。最新技术采用自旋转线锯系统,切割效率提升至15mm²/min,材料损耗率降至100μm以内。日本Disco公司开发的DWS系列设备已实现8英寸晶圆的稳定加工。
2. 激光隐形切割:利用皮秒激光在晶体内部形成改质层,通过热应力实现解理。德国通快公司的TruMicro 5000系统采用532nm波长,聚焦深度可达700μm,切割速度突破300mm/s,热影响区控制在3μm以内。
3. 等离子体切割:通过CF₄/O₂混合气体产生高温等离子体,实现化学刻蚀与物理溅射的协同作用。美国应用材料公司开发的Centura®系统在真空环境下实现0.05mm/min刻蚀速率,边缘崩缺小于5μm。
三、技术创新方向
1. 复合加工技术:日本东京大学研发的激光辅助线锯工艺,通过局部热软化使切割力降低40%,刀具寿命延长3倍。实验数据显示,200W光纤激光预热可使切割应力从1.2GPa降至0.7GPa。
2. 智能监测系统:集成声发射传感器和机器视觉,实时检测切割振动频谱和表面形貌。中科院团队开发的AI诊断系统,能提前300ms预测裂纹萌生,良品率提升至99.6%。
3. 超精密夹具设计:采用气浮轴承支撑的真空吸附夹具,配合六自由度补偿机构,将晶圆平面度控制在0.5μm以内。德国Siltronic公司的最新夹具系统可实现0.1arcsec的角度调节精度。
四、产业应用前景
随着6英寸晶圆制造成本降至硅材料的2.5倍,碳化硅器件渗透率持续提升。切割技术的进步使单片晶圆产出芯片数增加30%,预计到2026年全球碳化硅切割设备市场规模将达18.7亿美元。美国科锐公司与青岛大学联合开发的低温等离子切割技术,已成功将晶圆翘曲度控制在50μm以下,为车规级芯片量产奠定基础。
当前,碳化硅切割正从经验工艺向数字孪生模式转型,通过多物理场仿真优化工艺参数,实现纳米级加工精度。未来五年,随着量子传感技术和超快激光的发展,切割技术有望突破物理极限,推动宽禁带半导体产业进入新纪元。
点击右侧按钮,了解更多激光打标机报价方案。
免责声明
本文内容通过AI工具智能整合而成,仅供参考,博特激光不对内容的真实、准确或完整作任何形式的承诺。如有任何问题或意见,您可以通过联系1224598712@qq.com进行反馈,博特激光科技收到您的反馈后将及时答复和处理。