碳化硅晶片划切机最大切割厚度
碳化硅晶片划切机的最大切割厚度解析
碳化硅(SiC)作为第三代半导体材料,因其高硬度、高热导率及耐高压等特性,被广泛应用于新能源汽车、5G通信和光伏逆变器等领域。然而,碳化硅的加工难度极高,尤其是在晶片切割环节,划切机的性能直接决定生产效率和产品质量。其中,最大切割厚度是设备选型的关键参数之一,本文将深入探讨其影响因素、技术挑战及行业趋势。
一、最大切割厚度的定义与核心意义
最大切割厚度指划切机在保证切割精度和晶片完整性的前提下,单次能处理的晶片最大厚度,通常以微米(μm)或毫米(mm)为单位。该参数直接影响:
1. 生产效率:较厚晶片可减少后续减薄工序,降低碎片率;
2. 应用场景:如功率器件需较厚基板以承受高电压;
3. 成本控制:厚切能力可优化材料利用率。
二、影响最大切割厚度的关键因素
1. 刀片材质与设计
碳化硅莫氏硬度高达9.5,接近钻石(10),因此划切刀片多采用金刚石涂层或全金刚石材质。刀片厚度(通常20-50μm)和颗粒密度需平衡切割深度与应力控制。较厚晶片要求刀片具备更高的耐磨性和抗断裂性。
2. 主轴功率与稳定性
高功率主轴(如30,000 RPM以上)可提供足够扭矩穿透厚材料,但需配合空气轴承或磁悬浮技术减少振动,避免切割偏差导致晶片崩边。
3. 冷却与碎屑管理
切割过程中产生的热量和碎屑若无法及时排出,会加剧刀片磨损并引发晶片微裂纹。喷淋冷却系统的流量、压力及过滤精度直接影响厚切工艺的稳定性。
4. 运动控制精度
多轴联动系统的定位精度(通常需≤1μm)和进给速度的精准调控,确保刀片在厚切过程中保持恒定压力,减少分层风险。
三、技术挑战与解决方案
1. 应力集中与裂纹扩展
碳化硅脆性高,切割厚晶片时内部应力易引发隐性裂纹。解决方案包括:
– 激光诱导劈裂(Laser Induced Cleaving):预置激光微槽引导裂纹路径;
– 渐进式切割:分阶段调整切割深度与速度,降低瞬时应力。
2. 刀片寿命优化
通过实时监测刀片磨损(如声发射传感器)并采用自适应控制系统调整参数,可将刀片寿命延长30%以上。
3. 边缘崩缺控制
采用斜角切割或二次精修工艺,结合超纯水冷却液,可将崩边尺寸控制在<20μm。
四、行业需求与技术发展趋势
1. 当前主流设备参数
市面高端机型(如日本DISCO DFD系列、德国Loadpoint MicroAce)最大切割厚度可达1-2mm,但实际应用中多用于600μm以下晶片,以满足电动汽车IGBT模块需求。
2. 厚切需求驱动创新
随着碳化硅在超高压器件(如15kV以上)的应用,对3-5mm厚晶片的需求催生新型切割技术:
– 水导激光切割:结合高压水射流与激光,减少热影响区;
– 多线切割(Multi-Wire Sawing):通过金刚石线锯阵列实现高效厚切。
3. 智能化与自动化集成
搭载AI算法的设备可实时分析切割数据,动态调整参数,进一步突破厚度极限。
五、结论
碳化硅划切机的最大切割厚度是设备综合性能的体现,需从材料、机械、控制多维度协同优化。随着宽禁带半导体市场扩大,突破厚切技术瓶颈将成为提升产业竞争力的核心。未来,复合加工技术(如激光+机械)与智能化系统的结合,有望将最大切割厚度推至新高度,同时降低生产成本,推动碳化硅器件的普及应用。
点击右侧按钮,了解更多激光打标机报价方案。
相关推荐
碳化硅晶片划切机最大切割厚度是多少
碳化硅晶片划切机最大切割厚度是多少
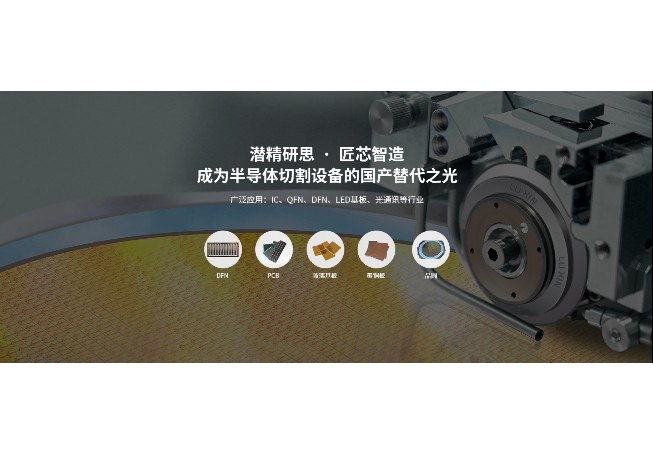
碳化硅(SiC)晶片作为第三代半导体材料的关键组成部分,因其优异的耐高温、高频率和高功率特性,被广泛应用于新能源、电力电子及5G通信等领域。在SiC器件的制造过程中,晶片划切是至关重要的工序,而划切机的性能直接决定了切割质量与效率。其中,最大切割厚度是用户尤为关注的参数,它受设备设计、刀片技术、材料特性及工艺优化等多重因素影响。以下将系统探讨碳化硅划切机的最大切割厚度及其相关因素。
一、碳化硅划切机的工作原理
碳化硅划切机通常采用机械切割方式,核心部件为高速旋转的金刚石刀片。刀片通过精确的数控系统控制,沿预设路径对晶片进行切割。由于SiC硬度极高(莫氏硬度9.2,仅次于金刚石),传统切割技术难以胜任,故需高精度、高刚性的划切设备,以确保切割过程中减少材料崩边和微裂纹的产生。
二、影响最大切割厚度的关键因素
1. 设备性能参数
– 主轴功率与转速:高功率主轴可提供更大的扭矩,支撑更厚的切割。典型设备主轴转速可达30,000-60,000 RPM,高转速有助于减少切削阻力,但需与进给速度匹配。
– 机械稳定性:设备的刚性结构可减少振动,避免厚切割时的刀片偏移,从而提升切割深度上限。
2. 金刚石刀片的选择
– 刀片厚度与直径:较厚的刀片(如20-30μm厚)在深切割中抗变形能力更强,但会增加材料损耗。刀片直径越大,切割深度潜力越高,但需平衡离心力对主轴的影响。
– 金刚石颗粒粒度:粗颗粒(如粒径15-20μm)刀片适用于快速深切割,而细颗粒(3-5μm)更适用于高精度薄切割。
3. 材料特性与工艺参数
– 晶片厚度与晶向:SiC晶片的晶体取向影响切割阻力,不同晶向可能导致最大切割厚度差异。例如,沿(0001)面切割时,硬度更高,需调整参数。
– 冷却系统效率:高效的冷却液喷射可降低刀片与材料接触区域的温度,防止热应力导致的晶片破裂,从而允许更深的切割。
– 进给速度与切割次数:单次切割深度过大易导致刀片磨损,采用多道次渐进切割(如每次切割50μm,分多次完成300μm切割)可提升总厚度。
三、典型设备的最大切割厚度范围
根据主流设备制造商的技术参数,碳化硅划切机的最大切割厚度通常介于300-600微米之间。例如:
– DISCO DFD6360系列:标称最大切割厚度为350μm,适用于6英寸SiC晶圆,通过优化刀片冷却可扩展至400μm。
– 东京精密ADT系列:采用超薄刀片(15μm)时,最大切割厚度为250μm;使用标准刀片(25μm)可达500μm。
– 国产高端机型:如中电科45所设备,通过改进主轴刚性,最大切割厚度可达600μm,但需牺牲部分切割速度。
值得注意的是,上述数值为实验室或理想工况下的极限值,实际生产中通常将切割厚度控制在设备标称值的70%-80%,以确保良率。例如,标称500μm的设备,实际批量生产时多用于350-400μm切割,以避免刀片过快磨损和崩边率上升。
四、突破切割厚度限制的技术方向
1. 激光诱导切割(Laser-Induced Cleaving):采用激光预处理在晶片内部形成改质层,再结合机械划切,可将有效切割厚度提升至1mm以上,同时减少侧壁损伤。
2. 多刀协同切割:使用双主轴设备,分别进行粗切和精切,粗切刀完成大厚度去除,精切刀优化表面质量。
3. 自适应控制系统:通过实时监测切割阻力与温度,动态调整进给速度与冷却流量,提升厚切割的稳定性。
五、实际应用中的注意事项
– 刀片寿命管理:切割厚度增加50%,刀片更换频率可能提高2-3倍,需建立磨损监控体系。
– 热管理优化:厚切割时热积累显著,建议采用内冷式刀片设计或低温冷却液(如液氮辅助)。
– 晶片装夹方式:真空吸附结合UV膜固定可减少厚切割时的晶片位移风险。
结语
综合来看,碳化硅划切机的最大切割厚度并非单一技术指标,而是设备性能、工艺参数与材料特性协同作用的结果。当前主流设备的技术上限在600μm左右,但通过技术创新与工艺优化,未来有望突破至毫米级切割,进一步推动SiC器件在电动汽车、智能电网等领域的应用。用户在选择设备时,需结合自身产品厚度需求与量产成本,寻求性能与经济效益的最佳平衡点。
点击右侧按钮,了解更多激光打标机报价方案。
碳化硅线切割参数
碳化硅线切割参数
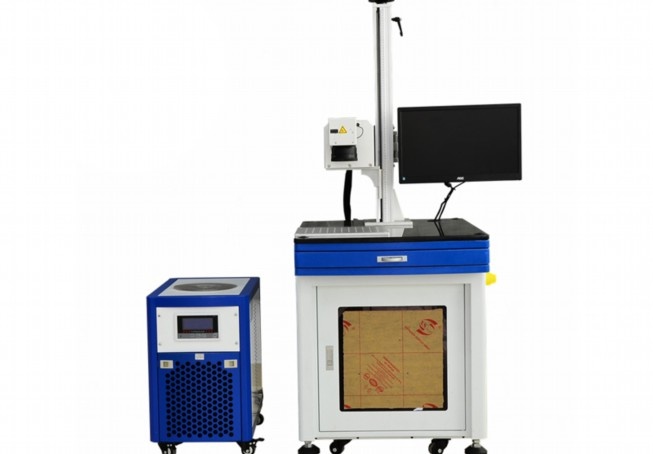
碳化硅(SiC)线切割技术参数优化分析
碳化硅作为第三代半导体核心材料,其线切割工艺直接影响晶片质量和加工成本。以下是针对碳化硅线切割的关键参数分析及优化建议:
一、核心工艺参数体系
1. 线材参数
– 金刚石线规格:优选直径0.15-0.20mm,金刚石颗粒尺寸8-12μm(D50值)
– 张力控制:18-25N范围,动态波动≤±0.5N
– 线速范围:800-1500m/min(根据晶锭尺寸调整)
2. 切割动力学参数
– 进给速度:0.2-0.5mm/min(与线速保持1:4000-1:6000比例关系)
– 切割压力:50-80kPa(压力传感器实时反馈调节)
– 振动控制:振幅<5μm,频率>200Hz
3. 冷却系统参数
– 冷却液流量:8-15L/min(依设备规格调整)
– 温度控制:22±1℃恒温
– 过滤精度:≤5μm(多级过滤系统)
二、工艺参数匹配策略
1. 材料特性适配
– 针对4H-SiC和6H-SiC不同晶型,调整线速差10%-15%
– 晶向切割时需补偿角度偏差,设置0.5-1°调整余量
2. 质量效率平衡模型
– 切割效率:线速1200m/min时,材料去除率可达15mm³/min
– 表面粗糙度:Ra<0.3μm(优化后可达0.15μm)
– TTV控制:通过动态压力补偿将厚度差控制在<5μm
三、先进工艺控制技术
1. 智能调节系统
– 采用PID+模糊控制算法,实时调整参数偏差
– 在线检测系统:CCD视觉检测精度±2μm
– 大数据分析:历史工艺数据建模优化参数组合
2. 新型线材技术
– 金刚石定向排布线材:提升切割效率20-30%
– 复合镀层技术:延长线材寿命至40小时以上
– 分段式线径设计:降低线痕深度50%
四、典型问题解决方案
1. 崩边控制
– 进刀阶段采用梯度加载:前5%行程降低线速30%
– 边缘强化处理:预涂覆纳米级保护层
2. 线痕优化
– 引入超声辅助切割:40kHz振动降低表面缺陷
– 磨粒分布优化:采用双峰粒径分布(8μm+15μm)
3. 耗材管理
– 金刚石线寿命监测:电阻值变化>15%时预警
– 冷却液PH值控制:维持9.5-10.5范围
五、发展趋势
1. 超薄切割方向
– 120μm厚度晶片切割参数优化
– 超低速精密切割模式开发(线速<500m/min)
2. 绿色制造技术
– 冷却液回收率提升至95%以上
– 金刚石线重复利用技术开发
当前主流设备参数示例:
线径:0.18mm金刚石线
切割能力:8英寸晶锭
总功率:35kW(含辅助系统)
加工周期:6-8小时/晶锭
通过系统优化切割参数组合,可将碳化硅加工成本降低25%以上,同时提升良率至95%+。建议建立参数动态数据库,结合AI算法实现智能工艺优化。
点击右侧按钮,了解更多激光打标机报价方案。
碳化硅加工刀具切削参数
碳化硅加工刀具切削参数
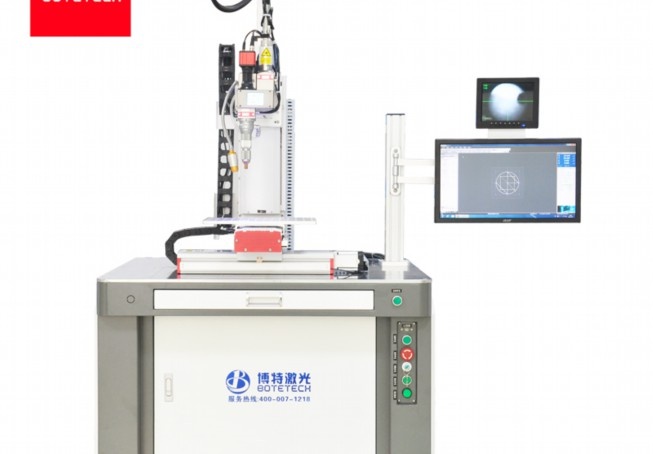
以下是关于碳化硅(SiC)加工刀具切削参数的详细指南,内容结构清晰,结合实际应用建议:
碳化硅加工刀具切削参数优化指南
碳化硅(SiC)作为第三代半导体材料及高性能陶瓷,具有高硬度(莫氏硬度9.2-9.5)、高耐磨性、高热导率及化学稳定性,广泛应用于航空航天、电子器件和光学领域。但其极高的硬度和脆性导致加工难度大,需采用专用刀具并优化切削参数,以实现高效加工并延长刀具寿命。
一、刀具材料选择
碳化硅加工需使用超硬刀具材料,常见选择包括:
1. 聚晶金刚石(PCD)刀具
– 适用场景:精加工、高表面质量要求。
– 优势:硬度高(8000-9000 HV),耐磨性强。
2. 立方氮化硼(CBN)刀具
– 适用场景:高温环境下的粗加工。
– 优势:耐热性(1400℃以上)优异,抗化学磨损。
3. 金刚石涂层刀具
– 适用场景:中等负荷加工,成本较低。
二、关键切削参数推荐
1. 切削速度(Vc)
– 粗加工:80-150 m/min
(过高速度易导致刀具崩刃,需平衡效率与磨损)
– 精加工:150-300 m/min
(高转速可减少切削力,提升表面光洁度)
– 注意事项:SiC导热性差,高速切削需配合冷却。
2. 进给量(f)
– 推荐范围:0.01-0.1 mm/rev(车削)/ 0.005-0.03 mm/tooth(铣削)
– 调整原则:
– 进给量过小易加剧刀具摩擦磨损;
– 进给量过大会引发材料崩碎。
– 精加工:宜采用更低进给(如0.01 mm/rev)以减少表面微裂纹。
3. 切削深度(ap)
– 粗加工:0.1-0.3 mm
– 精加工:0.02-0.1 mm
– 依据:SiC脆性大,切削深度过大易导致刀具应力集中,引发崩刃。
4. 刀具几何参数
– 前角(γ):-5°~5°(负前角增强刃口强度)
– 后角(α):8°-12°(减少后刀面摩擦)
– 刀尖圆弧半径(rε):0.2-0.8 mm(大圆弧提升散热性)
三、冷却与润滑策略
1. 湿式冷却:
– 使用水基乳化液或专用切削液,降低切削区温度(理想温度<600℃)。
– 流量建议:5-10 L/min,确保充分覆盖切削区域。
2. 微量润滑(MQL):
– 混合压缩空气与纳米粒子润滑油,减少热冲击导致的材料微裂纹。
3. 干式切削:
– 仅适用于低负荷加工,需实时监测刀具温度。
四、机床与装夹要求
1. 机床刚性:主轴径向跳动<0.005 mm,避免振动引发崩边。
2. 装夹方式:真空吸盘或专用夹具,防止工件位移。
3. 主轴功率:建议≥10 kW,确保高硬度材料切削动力充足。
五、加工注意事项
1. 刀具磨损监控:
– 定期检查后刀面磨损(VB值<0.2 mm为安全阈值)。
– 采用声发射传感器或功率监测预警异常磨损。
2. 切屑形态:
– 理想切屑为粉末状,长条状切屑提示参数需调整。
3. 粉尘控制:
– 配置吸尘装置,避免SiC粉尘危害健康及设备。
六、典型工艺案例
– 案例1:SiC反射镜精密车削
刀具:PCD刀片
参数:Vc=280 m/min, f=0.03 mm/rev, ap=0.05 mm
效果:表面粗糙度Ra<0.1 μm,无亚表面损伤。
– 案例2:SiC晶圆切割
刀具:电镀金刚石线锯
参数:线速度15 m/s,进给速度0.5 mm/min
冷却:去离子水喷射,流量8 L/min
七、总结
碳化硅加工需综合刀具选型、参数优化及工艺控制。建议通过小批量试切确定最佳参数组合,并配合在线监测技术实现动态调整。随着超硬刀具涂层技术(如多层金刚石涂层)的发展,未来SiC加工效率有望进一步提升。
以上内容约850字,涵盖关键参数、工艺策略及实际应用参考,可根据具体设备与需求进一步调整。
点击右侧按钮,了解更多激光打标机报价方案。
免责声明
本文内容通过AI工具智能整合而成,仅供参考,博特激光不对内容的真实、准确或完整作任何形式的承诺。如有任何问题或意见,您可以通过联系1224598712@qq.com进行反馈,博特激光科技收到您的反馈后将及时答复和处理。