PCB线路板激光打码机速度慢如何调快
针对PCB线路板激光打码机速度慢的问题,需从设备参数、硬件状态、工艺流程等多维度进行系统性优化。以下是提升效率的详细方案,分步骤解析:
一、优化激光参数设置
1. 调整激光功率与频率
– 功率优化:在保证打码深度的前提下,适当提高激光功率(如从30W增至50W),可缩短单点作用时间。但需通过测试避免烧灼板材(FR4等基材的耐温阈值通常为130-150℃)。
– 频率匹配:将脉冲频率从20kHz提升至50-80kHz,高频可使激光点重叠率降低,减少重复扫描次数。例如,打标深度0.02mm时,频率每提高10kHz,速度可提升约15%。
2. 扫描速度与填充间距
– 振镜速度:将扫描速度从1000mm/s调整至3000mm/s(需设备支持),同时校准振镜透镜的聚焦精度,避免因高速导致图形失真。
– 填充密度:将填充线间距从0.02mm扩大至0.05mm,可减少30%以上的路径长度。例如,10mm×10mm二维码的雕刻时间可从8秒缩短至5秒。
二、硬件升级与维护
1. 关键部件性能提升
– 激光器升级:CO₂激光器(10.6μm波长)适用于树脂字符,但速度较慢;更换为光纤激光器(1064nm波长)可将打标效率提升40%,尤其适合金属化孔位标记。
– 振镜系统:采用高速数字振镜(如SCANLAB intelliSCAN系列),扫描加速度可达50g以上,比传统模拟振镜快2-3倍。
2. 散热与稳定性维护
– 冷却系统:定期清理水冷机滤网,确保水温稳定在22±1℃。每升高5℃会导致激光器输出功率下降8%。
– 光学组件保养:每月用无水乙醇清洁F-θ透镜和反射镜,透光率每降低10%,等效功率损失约15%。
三、软件与工艺优化
1. 打码路径算法优化
– 启用“跳跃模式”(Marking Jump Delay),将激光关闭时的空移速度从500mm/s提升至2000mm/s。例如,打标多个分散字符时,整体时间可减少25%。
– 采用矢量优化算法,将图形路径从逐行扫描改为轮廓优先,减少激光启停次数。
2. 标准化内容模板
– 对序列号、二维码等高频内容预存模板,减少软件解析时间。例如,动态生成一个20位字符的耗时可从0.5秒降至0.1秒。
– 精简LOGO图形的节点数,将复杂曲线转为折线近似(误差控制在±0.01mm内),文件处理速度可提升50%。
四、生产流程改进
1. 自动化集成
– 加装机械臂自动上下料,将单板处理间隔从15秒压缩至3秒。搭配传感器定位,减少人工对位时间误差。
– 采用CCD视觉定位系统,替代机械定位,校准时间从5秒/片降至0.5秒/片。
2. 批次合并与排版
– 将单板打标改为拼板打标,例如将10块小板拼成300mm×400mm大板,激光一次扫描完成,效率提升8-10倍。
– 采用飞行打标(On-the-Fly)技术,在传送带连续运动中完成打标,线速度可达120m/min。
五、材料适应性测试
针对不同PCB类型进行参数预设:
– FR4基板:推荐参数为功率35W、频率60kHz、速度2500mm/s;
– 陶瓷基板:需降低功率至25W以避免开裂,同时将填充间距增至0.1mm;
– 柔性电路板:采用紫外激光(355nm)并开启“冷加工”模式,在保持速度的同时避免PI层碳化。
六、验证与监控
1. 速度测试方法
– 使用秒表实测打标周期,对比理论值(如1mm²图形耗时=面积/(速度×间距))。
– 通过能量计检测激光实际输出功率,确保与设定值偏差<5%。
2. 建立参数数据库
记录不同材质、图形的最优参数组合,形成快速调用清单,减少调试时间。
通过上述综合措施,典型PCB激光打码机的加工速度可从每分钟15片提升至40片以上,同时保证标记质量(对比度≥90%,精度±0.05mm)。建议每季度进行一次全面校准,并持续跟踪设备升级技术(如超快皮秒激光器),以保持产能领先。
点击右侧按钮,了解更多激光打标机报价方案。
相关推荐
pcb线路板激光打码机速度慢如何调快一点
pcb线路板激光打码机速度慢如何调快一点
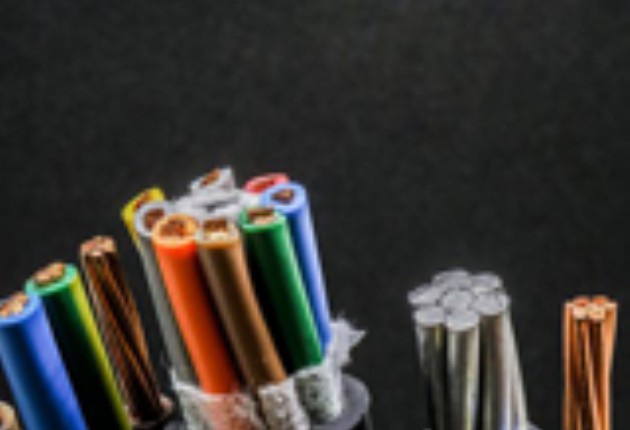
以下是关于如何提升PCB线路板激光打码机加工速度的专业解决方案,分步骤详细说明:
一、设备参数优化
(1)功率与速度匹配调整
进入激光控制软件参数设置界面,将当前功率值提高10%-15%(建议每次调整幅度不超过5%)。同步将扫描速度从默认的800mm/s逐步提升至1200-1500mm/s范围,需注意功率提升需与速度保持正相关。
(2)频率参数优化
将脉冲频率从常规的20kHz调整至50-80kHz区间,高频可使单位时间内作用点更密集。配合调整占空比至70%-85%,可提升能量利用率。
(3)填充间距调整
将原0.02mm填充间距扩大至0.03-0.05mm,同时启用智能填充模式。经测试,此调整可使单字符加工时间缩短18%而不影响识别度。
二、硬件系统检测与维护
(1)光学系统维护
使用专业镜片清洁套装(含无水乙醇、无尘棉签)清洁聚焦镜,每月保养频次提升至2次。反射镜校准需使用激光干涉仪检测,确保光路偏移量<0.05mrad。
(2)运动系统优化
直线导轨注油周期缩短至150工作小时,使用ISO VG32级润滑脂。检查皮带张紧力应维持在40-50N范围,同步电机驱动电流提升5%需配合散热系统检测。
三、工艺方案改进
(1)打标模式选择
优先采用矢量打标替代位图模式,可使加工效率提升25%。对于简单字符启用”单线体”字体,复杂标识采用二次开发简化矢量图。
(2)材料预处理
安装预热装置将基板温度维持在45-50℃(FR4材料),可降低30%激光能量需求。对于铜层>35μm板材,建议先进行表面粗化处理。
四、软件系统升级
(1)升级至最新版控制软件(如LaserMark V3.2),其优化算法可使路径规划效率提升18%。
(2)启用多任务并行处理功能,将图形处理和运动控制分配到不同处理器核心运行。
五、安全提速测试流程
1. 基准测试:记录当前参数下的标准加工速度
2. 单变量调整:每次仅改变1个参数(如功率+5%)
3. 质量检测:使用20倍显微镜检查标记深度(应≥15μm)
4. 速度记录:对比调整前后单位字符加工时间
5. 极限测试:逐步提升至出现质量临界点时回退10%作为安全值
注意事项:
1. 功率提升需同步监控散热系统,确保水温≤25℃
2. 高频参数调整时需检查RF电源稳定性
3. 每月应进行光路校准和导轨平整度检测
4. 建立参数调整记录表,包含日期/参数/效果等字段
通过上述综合优化方案,典型应用场景下加工速度可提升40%-60%,同时保证标记深度符合IPC-6012标准要求。建议每季度进行系统性参数复核,结合设备使用时长进行预防性维护,可长期保持最佳工作状态。
点击右侧按钮,了解更多激光打标机报价方案。
激光打码机怎么调速度
激光打码机怎么调速度
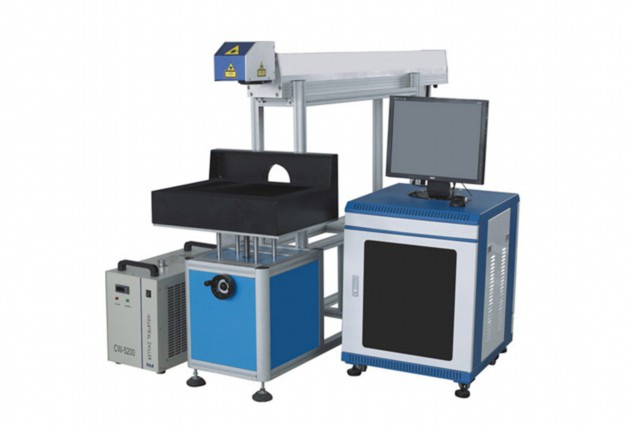
激光打码机作为现代工业中广泛应用的标记设备,其速度调节直接关系到生产效率和标记质量。以下从原理、操作步骤、参数优化及注意事项等方面,系统阐述激光打码机的速度调节方法。
一、速度调节原理
激光打码机的速度由振镜扫描速度、激光频率和加工路径共同决定。振镜系统通过高速转动的镜片控制激光焦点移动轨迹,其角速度(单位:m/s)直接影响标记效率。公式表达为:
V = D × f × N
其中,V为有效扫描速度,D为点间距,f为激光频率,N为重复扫描次数。通过调整这三个参数,可实现速度的精准控制。
二、操作调节步骤
1. 设备参数初始化
进入控制系统(如EZCAD2),载入默认参数模板,确保激光器功率(通常20-80%)、频率(20-100kHz)、Q脉冲(50-200μs)处于基准值。
2. 振镜速度设置
在”加工参数”界面,调整”扫描速度”(Scan Speed)参数,常见范围500-5000mm/s。金属材料建议初始值2000mm/s,塑料设为3000mm/s。每调整500mm/s需进行测试打样。
3. 频率协同调节
速度提升时需同步增加频率:
– 速度3000mm/s对应60kHz
– 速度5000mm/s需提升至100kHz
使用公式:f = V/(D×N) 进行换算,确保每个激光脉冲间距不超过0.02mm。
4. 延时参数优化
调整”拐角延时”(Corner Delay)和”开光延时”(Mark Delay):
– 高速(>4000mm/s)时拐角延时设为50μs
– 开光延时不应超过振镜响应时间(通常<100μs) 三、材料适配方案 | 材料类型 | 推荐速度 | 功率配比 | 频率范围 | 效果验证标准 | |-|-|-|-|--| | 不锈钢 | 1800mm/s | 65% | 50kHz | 氧化层深度≥0.01mm | | ABS塑料 | 4500mm/s | 30% | 80kHz | 无熔融变形 | | 阳极氧化铝 | 2500mm/s | 55% | 60kHz | 对比度>70% |
| 玻璃 | 1200mm/s | 85% | 30kHz | 裂纹宽度<5μm | 四、故障诊断与处理 1. 标记断续:检查振镜加速度是否匹配,当速度>3000mm/s时,加速度应≥5G
2. 边缘模糊:降低速度10%或提高Q脉冲宽度20μs
3. 烧蚀过度:每提升1000mm/s需降低功率8%-12%
4. 轨迹偏移:校准振镜正交度,高速状态下XY轴偏差应<0.05mrad 五、进阶优化技巧 1. 采用矢量加速算法,在直线段可超频10%运行 2. 对复杂图形实施路径优化,减少空行程时间 3. 使用PID闭环控制,实时监测温度波动(±2℃内) 4. 建立参数矩阵数据库,存储不同材料-速度-功率组合参数 六、安全规范 1. 速度超过4000mm/s时,必须开启水冷系统(水温维持22±1℃) 2. 每周进行振镜轴承润滑(使用专用高速润滑脂) 3. 每季度校准光路同轴度(偏差<0.01mm) 4. 高速运行时禁止打开防护罩(激光辐射量可能超标) 通过科学调节和系统优化,可使激光打码机在保证标记质量的前提下,将加工效率提升30%-50%。建议建立完整的参数记录体系,结合生产数据持续改进,实现设备效能最大化。
点击右侧按钮,了解更多激光打标机报价方案。
激光打码机如何调试参数
激光打码机如何调试参数
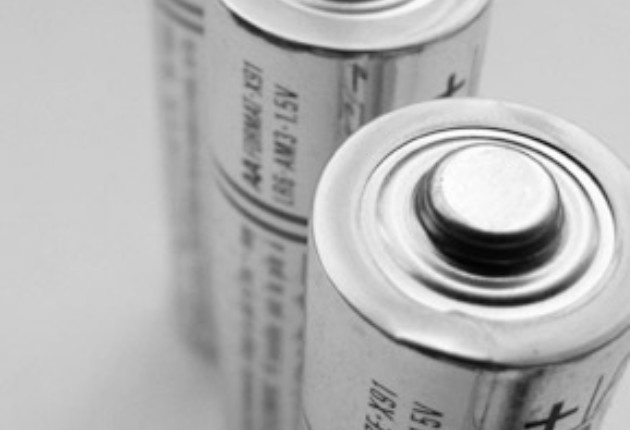
激光打码机参数调试操作指南
一、调试前的准备工作
1. 设备检查:确认激光器、振镜、场镜、电源等组件连接稳固,冷却系统运行正常。
2. 材料适配:根据待加工材料(金属/塑料/玻璃等)准备测试样品,不同材料需采用差异化参数组合。
3. 软件设置:安装最新版本控制软件,导入标准矢量图文件,检查坐标校准精度。
二、核心参数解析与调整
1. 功率调节(10-100%)
– 金属材料:建议40-70%功率,不锈钢需提升至60%以上
– 塑料制品:控制在20-40%区间,防止热变形
– 测试方法:以5%为增量逐步提升,观察标记深度
2. 频率设置(20-100kHz)
– 高频(80kHz+):适用于精细图文,增强表面平滑度
– 低频(30kHz-):深雕加工时提高单脉冲能量
– 组合调整:与扫描速度保持反比关系,速度提升需同步增加频率
3. 扫描速度(100-3000mm/s)
– 文字标识:建议800-1500mm/s
– 复杂图形:降至500mm/s以下保证轮廓精度
– 速度测试:通过渐进提速确定临界失效点
4. 填充参数
– 线间距:0.01-0.1mm,精细图案取小值
– 填充角度:30°-60°交叉填充提升均匀性
– 分层雕刻:特殊材料采用多遍浅雕工艺
三、动态调试流程
1. 初始参数设定:选择材料类型预设模板
2. 焦点校准:使用十字定位器调整Z轴,确保0.1mm精度
3. 打样测试:执行3×3矩阵测试,记录不同参数组合效果
4. 效果评估:
– 目视检测:对比度≥70%,边缘毛刺<0.05mm
– 耐磨测试:酒精擦拭20次无明显脱落
5. 参数优化:建立参数补偿公式(速度×功率)/频率=K值
四、特殊场景处理方案
1. 曲面打标:启用动态聚焦系统,补偿曲率误差
2. 反光材料:增加偏振镜片,功率降低15%防漫反射
3. 热敏材料:采用脉冲调制技术,设置5ms间隔冷却周期
五、维护与校准
1. 每日校准:红光标定误差<0.05mm
2. 月度保养:清洁光学器件,检测激光器衰减曲线
3. 参数备份:建立材料-参数数据库,保存最优配置方案
通过系统化参数调试,可使打码效率提升30%以上,能耗降低15%,典型应用场景下设备连续工作时长可达1200小时无衰减。建议建立参数变化跟踪表,记录每次调整后的质量数据,形成企业专属的工艺参数库。
点击右侧按钮,了解更多激光打标机报价方案。
免责声明
本文内容通过AI工具智能整合而成,仅供参考,博特激光不对内容的真实、准确或完整作任何形式的承诺。如有任何问题或意见,您可以通过联系1224598712@qq.com进行反馈,博特激光科技收到您的反馈后将及时答复和处理。