铜箔外形激光切割机切不透
好的,这是一份关于铜箔外形激光切割机“切不透”问题的分析报告及解决方案建议,约800字:
铜箔外形激光切割机“切不透”问题深度分析与解决路径
铜箔作为电子电路、锂电池等领域的核心基础材料,其精密加工需求日益增长。激光切割因其非接触、高精度、高柔性的特点,已成为铜箔外形加工的主流工艺之一。然而,在实际生产中,“切不透”是困扰操作人员的常见且棘手的问题,直接影响产品良率、生产效率和成本。以下针对此问题进行系统分析并提出解决思路:
一、问题核心:能量传递与吸收失效
激光切割铜箔的本质是利用高能量密度的激光束局部熔化或气化材料,配合辅助气体吹除熔融物形成切缝。出现“切不透”,核心在于到达铜箔表面的有效激光能量不足以克服材料移除阈值,或能量传递/吸收过程受阻。具体可分解为以下关键环节:
二、根本原因分析(鱼骨图思维:人、机、料、法、环、测)
1.激光源与光路系统(机):
激光功率不足/衰减:激光器老化、泵浦源效率下降、谐振腔污染或冷却系统异常导致输出功率低于设定值,无法达到铜箔(尤其是较厚或高纯度铜箔)的切割阈值。
光束质量劣化:激光模式不稳定(如TEM00模劣化)、光束发散角过大或存在像散,导致焦点处能量密度不足。常见原因有光学镜片(透镜、反射镜)污染、损伤、热透镜效应,或光路准直偏移。
焦点位置偏移:焦点未准确落在铜箔表面或最佳切割焦深区间内(通常略低于表面)。Z轴高度设定错误、热变形、自动调焦系统故障、振动干扰均可导致。
光学元件污染/损伤:切割产生的烟尘、溅射物附着在保护镜、聚焦镜表面,严重降低透光率。镜片划伤或镀膜烧蚀也会导致能量损失。
2.加工参数设置(法):
切割速度过快:单位长度材料吸收的激光能量不足。
激光功率设置过低:未根据材料厚度、类型、切割速度合理设定。
脉冲参数不当(针对脉冲激光):峰值功率、脉冲频率、脉宽不匹配,无法有效熔化/气化铜箔。
辅助气体问题:
类型错误:铜箔切割通常需高纯氮气(N2)以防止氧化,有时也用压缩空气(效率较低)。使用氧气(O2)会形成高熔点氧化铜,更难切透。
压力/流量不足:无法有效吹走熔融铜液,导致热量堆积在切口前端形成“热障”,阻碍后续激光能量进入,甚至造成重凝堵塞切口。
喷嘴问题:喷嘴堵塞、磨损(孔径变大或变形)、安装不正(与光束不同轴),导致气流紊乱、保护气幕失效、吹除能力下降。
3.材料因素(料):
铜箔厚度超标:实际厚度大于设备/工艺设定的能力范围。
材料成分/状态变化:不同批次铜箔的纯度、硬度、表面处理(如抗氧化涂层)有差异,影响吸收率和热传导。
表面污染/氧化:油污、灰尘、严重氧化层增加激光反射和散射,降低吸收率。
张紧力不足/不平整:铜箔在切割区域有褶皱或下垂,导致离焦,能量密度骤降。
4.设备状态与环境(环、机):
平台/运动系统精度问题:导轨磨损、丝杠间隙、伺服响应滞后导致实际运动轨迹与设定路径偏差,部分区域未有效切割。
冷却系统异常:激光器或光学头冷却不足,引发功率保护降额或光学元件热变形。
环境干扰:强振动(如附近大型设备运行)、温度剧烈波动影响光路稳定性和设备精度。
气压/气源不稳定:供气压力波动导致辅助气体效果时好时坏。
5.操作与维护(人):
参数设置错误:操作员误输入参数。
设备维护不到位:未定期清洁光路、更换消耗品(保护镜、喷嘴)、保养运动部件。
装夹/对位失误:材料未正确固定或定位,导致切割位置偏移或离焦。
三、系统性排查与解决方案
解决“切不透”需遵循“从易到难、由表及里”的原则进行排查:
1.快速检查与基础调整:
确认参数:仔细核对当前切割程序参数(功率、速度、频率、气压、焦点)是否符合该材料的工艺规范。尝试小幅降低切割速度或提高激光功率(注意防烧损)。
检查气体:确认气体类型(应为N2)、气压/流量是否达标,检查气管有无折弯泄漏、过滤器/减压阀是否正常,清洁或更换堵塞/磨损的喷嘴。
清洁光学窗口:立即检查并清洁切割头下方的保护镜片(遵循严格的无尘操作规范)。
检查材料:确认铜箔厚度、表面是否清洁无氧化、平整无褶皱。清洁表面污渍。
验证焦点:进行焦点标定测试(如斜坡测试),调整Z轴高度至最佳焦点位置。
2.深入诊断与维护:
检查光束/光路:使用激光功率计检测实际输出功率是否达标。通过专用设备(如光束质量分析仪)或观察打标/烧蚀效果评估光束模式。系统性地检查并清洁所有光路中的反射镜、聚焦镜(需专业拆卸)。检查光路准直。
设备状态检查:检查运动系统(导轨、丝杠)润滑、磨损和间隙。确认冷却水流量、温度正常。检查设备水平及固定是否牢靠,排除环境振动源。
查阅日志/联系厂商:查看设备运行日志和报警信息。联系设备制造商技术支持,获取针对该型号设备的专业诊断建议和可能的参数优化方案。
3.工艺优化与预防:
建立标准工艺库:对不同厚度、类型的铜箔建立并严格验证最优切割参数组合。
实施预防性维护计划:定期(按小时或批次)清洁保护镜片、更换喷嘴;定期(按周/月)检查清洁内部光路、保养运动部件、校准焦点和光路;定期(按年)检测激光功率和光束质量。
控制环境与物料:确保工作环境清洁、温湿度适宜、无强振动。严格管控来料铜箔的规格和存储条件。
操作员培训:强化操作员对设备原理、参数意义、日常点检、基础故障识别的培训。
四、结论
铜箔激光切割机“切不透”是一个多因素综合作用的结果。解决该问题不能仅靠单一调整,而需进行系统性排查,从参数设置、辅助气体、光学系统清洁、焦点校准等基础环节入手,逐步深入到设备状态、光路质量和工艺优化层面。建立并严格执行标准化的操作流程、工艺参数库和预防性维护计划是防止问题复发的关键。对于复杂或持续存在的问题,务必寻求设备制造商专业技术支持,利用其专业工具和经验进行深度诊断修复。通过科学分析和严谨执行,可有效解决“切不透”难题,保障生产的连续性和产品的高质量。
(字数统计:约850字)
补充说明:
本报告基于通用原理分析,具体到某一台设备(如您提到的“250604212”可能是设备编号或订单号),还需结合该设备的具体型号、配置、使用历史、当前报警信息等进行针对性诊断。
实际操作中务必遵守激光安全规范,清洁光学元件和调整光路时需特别小心,避免损伤或造成人身伤害。
如果经过基础排查仍无法解决,强烈建议联系设备供应商的售后服务工程师进行现场诊断和维修。
点击右侧按钮,了解更多激光打标机报价方案。
相关推荐
激光切割机切铜板
激光切割机切铜板
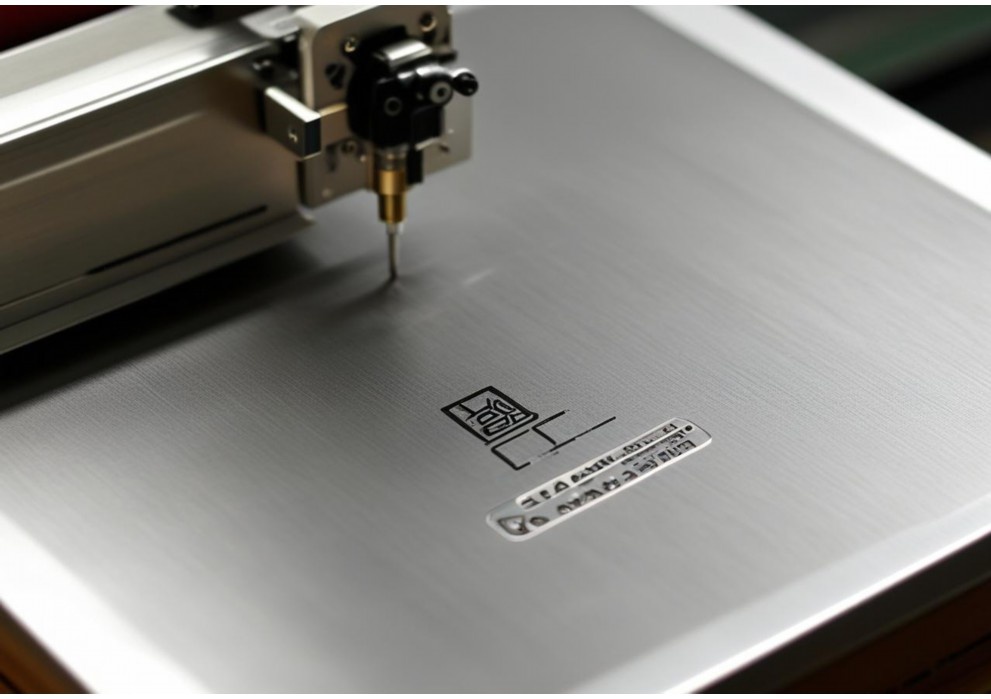
激光切割机高效切割铜板:工艺要点与应用解析
铜板因其优异的导电性、导热性和延展性,广泛应用于电力电子、散热器、装饰等领域。激光切割作为精密加工手段,在铜板加工中展现出独特优势,但也面临特殊挑战。
一、铜板激光切割的独特挑战与应对
高反射率陷阱:铜对常用红外激光(如1μm光纤激光)反射率极高(>90%),导致大量能量损失,切割困难。
导热性难题:铜散热极快,热量难以在切口处有效聚集,影响切割效率和断面质量。
粘渣与毛刺:熔融铜粘性大,易附着在切口下方形成难以清除的熔渣和毛刺。
针对性解决方案:
高功率激光破局:采用≥3kW高功率光纤激光器(推荐6kW以上),以强度克服反射。
抗反射技术加持:使用绿光(532nm)或紫外(355nm)激光器,铜对其吸收率显著提升(绿光吸收率约40%)。
工艺参数精调:优化焦点位置(常置于板面以下)、峰值功率与占空比(如使用脉冲模式)、气压控制(高纯氮气辅助吹渣)。
二、核心工艺参数与设备要求
(典型参数参考表)
|铜板厚度|激光功率|切割速度|辅助气体|喷嘴类型|焦点位置|
|-||||||
|0.5mm|1-2kW|8-15m/min|高纯氮气(≥15bar)|小口径(1-1.5mm)|板面下0.2mm|
|1mm|2-3kW|5-10m/min|高纯氮气(≥18bar)|小口径(1-1.5mm)|板面下0.3mm|
|2mm|≥4kW|2-5m/min|高纯氮气(≥20bar)|特殊防溅射喷嘴|板面下0.5mm|
|3mm+|≥6kW|<2m/min|高纯氮气(≥25bar)|专用抗反光喷嘴|板面下1mm| 设备关键要求: 1.高功率高亮度激光源:光纤激光器(IPG、nLIGHT等)为主流。 2.动态调焦系统:实时补偿热透镜效应,保持焦点稳定。 3.防反射保护装置:防止反射光损坏激光器光学元件。 4.高稳定性气路系统:确保气压恒定,有效吹除熔融物。 三、优势应用场景 精密电子元件:FPC柔性电路板补强钢片、引线框架(切缝<0.1mm)。 高效散热系统:服务器/IGBT水冷板流道(复杂异形孔无毛刺)。 新能源电池制造:锂电池极耳(铜箔)无接触切割(热影响区<50μm)。 建筑装饰艺术:紫铜屏风、浮雕(精细图案无变形)。 四、质量控制与安全要点 断面质量控制:监测毛刺高度(应<板厚5%)、检查背面无熔渣粘连(通过调整气压和速度优化)。 防氧化处理:切割后及时清洁表面氮化物残留,必要时做钝化保护。 严格防护措施:安装防反射罩、佩戴专用防护眼镜(防铜蒸气及强反射光)。 实时监控系统:配备CCD视觉或红外热像仪,监测切割过程稳定性。 总结: 激光切割铜板是技术密集型工艺,成功的关键在于高功率激光源选择、抗反射技术应用、氮气辅助工艺优化及精密参数控制。随着高亮度绿光激光器等技术进步,铜及高反材料的切割效率与质量将持续提升。企业在引入该工艺时,需结合自身产品厚度和精度需求,选择适配设备并建立严格工艺规范,方能充分发挥激光切割在铜加工领域的精密、高效与柔性优势。 >实践建议:对于厚度>3mm的纯铜板,可考虑”激光-水刀复合切割”或”铣削后激光精修”工艺以平衡效率与质量。持续监控镜片污染状况(铜蒸气沉积)是保障长期稳定生产的关键细节。
点击右侧按钮,了解更多激光打标机报价方案。
如何用激光切割机切割铜板
如何用激光切割机切割铜板
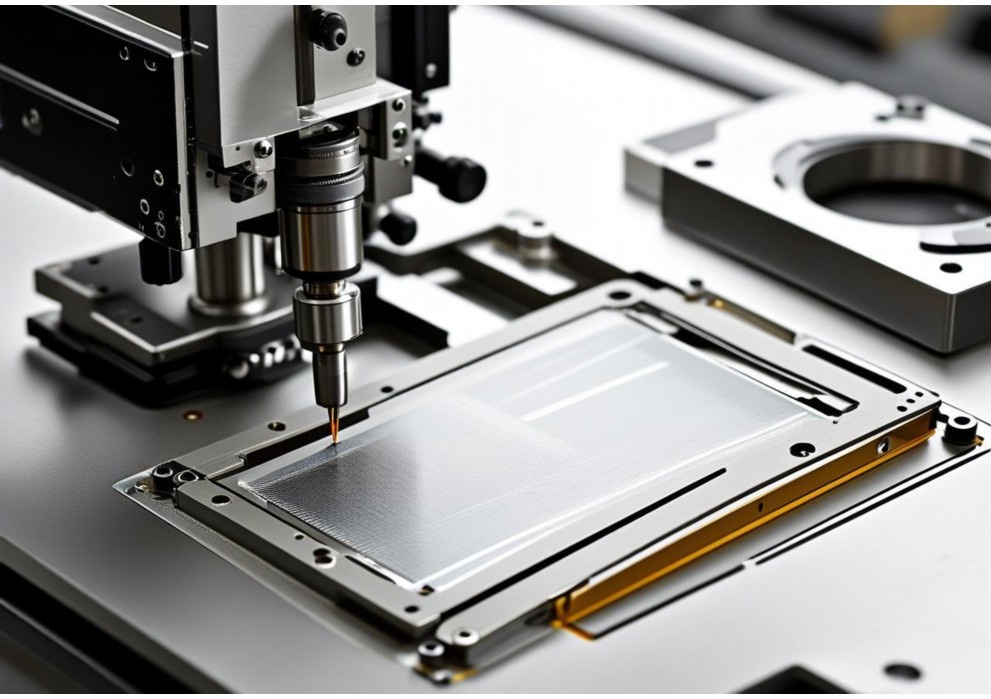
激光切割机切割铜板:专业指南与技巧
铜板凭借其优异的导电性和导热性,广泛应用于电子、散热器、装饰及工业领域。激光切割因其高精度和无接触特性成为铜板加工的理想选择,但铜的高反射率和高导热性也带来独特挑战。以下为使用激光切割机切割铜板的详细步骤与关键要点:
一、核心设备要求与安全准备
1.激光器类型:光纤激光器
必须选择光纤激光器(波长1070nm左右)。CO2激光器(波长10.6μm)绝大部分能量会被铜表面反射,效率极低且极易损坏激光器。
功率选择:薄板(<1mm)可用500W-1000W;中厚板(1-3mm)推荐1500W-3000W;厚板(>3mm)需3000W以上高功率激光器。
2.安全防护:重中之重
反射防护:铜的强反射性是最主要风险。确保切割头配备高质量、针对铜反射优化的防护镜片(通常为铜金膜镜片),并定期检查更换。
操作员防护:佩戴专用激光防护眼镜(针对光纤激光波长)。
设备防护:激光器腔体和切割头内部需有完善的反射光监测与防护机制。
环境安全:清理易燃物,保证良好通风(铜切割产生金属粉尘和少量烟雾)。
二、切割前准备
1.材料处理:
清洁表面:去除油污、氧化物、保护膜,确保表面洁净干燥。污渍会导致切割不均匀和反射异常。
提高吸收率(可选但推荐):
涂层法:在切割区域均匀喷涂薄层激光增透材料(如专用黑色标记漆)。
氧化法:对表面进行轻微氧化处理(需控制程度)。
覆膜法:粘贴专用激光吸收膜(效率高,成本稍高)。
平整度:确保铜板平整,避免因翘曲导致焦点偏移或碰撞喷嘴。
2.设备检查与设置:
聚焦镜片清洁:无尘环境操作,用专用工具清洁镜片。
喷嘴选择与校准:
根据板材厚度选择喷嘴孔径(通常薄板用较小孔径如Φ1.0-1.5mm,厚板用较大孔径如Φ2.0-3.0mm)。
精确校准喷嘴高度(至关重要!):使用调高器或塞尺设定喷嘴到板材表面的距离(通常在0.5-1.5mm范围),确保同心度和气流稳定。
气体选择与连接:
必须使用高纯度氮气(N2)作为切割辅助气体(纯度≥99.999%)。氧气(O2)会导致铜剧烈氧化,切口发黑、粗糙、产生大量熔渣。
检查气路密封性,连接稳定。
焦点位置设定:
焦点位置对切割质量(尤其是垂直度和粗糙度)影响显著。通常焦点位于板材表面或略微进入板材内部(负离焦)效果更好(例如-1mm到-2mm)。
需通过试切确定最佳焦点位置。
三、关键切割参数设置与优化
参数需根据激光器功率、铜板厚度、切割速度、喷嘴、气体压力综合调整。以下为参考范围(务必以实际设备试切为准):
|参数|薄铜板(<1mm)|中厚铜板(1-3mm)|厚铜板(>3mm)|备注|
|:–|:–|:|:–|:|
|激光功率|500W-1000W|1500W-3000W|3000W+|功率不足无法有效熔融,过高易过烧|
|切割速度|较高(5-15m/min)|中等(2-8m/min)|较低(0.5-3m/min)|速度过快切不透,过慢导致热影响区大、挂渣|
|氮气压力|较高(10-20bar)|高(15-25bar)|非常高(20-30+bar)|压力不足无法有效吹走熔融物,保证切口清洁|
|焦点位置|表面或略下(-0.5mm)|板材内(-1mm~-2mm)|板材内(-2mm~-3mm)|负离焦增加能量密度,改善厚板切割能力|
|喷嘴高度|0.8-1.2mm|1.0-1.5mm|1.2-2.0mm|确保气流顺畅,避免碰撞|
|穿孔参数|低功率/短时间脉冲|脉冲穿孔或渐进穿孔|必须使用渐进穿孔|尤其重要!防止高反射熔融物飞溅损坏喷嘴/镜片|
穿孔技巧(关键难点):
避免直接高功率连续穿孔:极易引起高反射熔融物剧烈飞溅。
推荐方法:
脉冲穿孔:使用较低功率的脉冲激光逐步“啄”穿材料。
渐进穿孔:激光功率由低到高缓慢增加,同时辅助气体压力也逐步提升,直至穿透。这是最安全有效的方法。
穿孔位置尽量远离轮廓起点一小段距离。
四、操作流程
1.软件准备:导入或绘制切割图形,合理排样,设置切割路径(引入引出线)。
2.装夹固定:使用夹具(磁性、机械式)或专用切割平台(如蜂窝板)牢固固定铜板,防止移动或振动。
3.设定起点与高度:将切割头移动到板材起始位置,启动调高器自动探测并设定初始高度。
4.启动切割:确认所有参数和安全措施无误后,启动切割程序。密切监控初始穿孔过程。
5.过程监控:观察切割火花状态(应稳定向下喷射)、听气体声音是否稳定、注意是否有异常反射光或报警。
6.完成与取件:切割完成后,待平台冷却(尤其是薄板易烫手),小心取下工件,注意锋利边缘。检查切割质量。
五、常见问题与解决方案
1.切不透/速度慢:
功率不足→提高功率(需在设备能力范围内)。
速度过快→降低切割速度。
焦点位置错误→调整焦点(通常向负离焦方向试)。
气体压力不足/纯度不够→检查气源、管路,提高压力,确保氮气纯度。
喷嘴堵塞/损坏→清洁或更换喷嘴。
2.切口粗糙/挂渣多:
气体压力不足或纯度低→提高压力,确保高纯氮气。
速度过快或过慢→优化切割速度。
焦点位置不佳→调整焦点位置。
功率不合适→微调功率(过高可能使熔池紊乱)。
3.切缝过宽/垂直度差:
焦点位置不准→精确调整焦点。
喷嘴孔径过大→尝试更小孔径喷嘴。
气压过高→适当降低气压。
4.反射损坏喷嘴/镜片(最严重):
穿孔参数/方法错误→必须使用脉冲或渐进穿孔!
喷嘴高度设置错误(过低)→重新校准喷嘴高度。
镜片污染或损坏→立即停机检查更换镜片。
材料表面极度不平或有突起→确保板材平整。
设备防反射机制失效→联系设备厂商检修。
六、提升切割质量与效率的附加建议
表面预处理:使用涂层、氧化或覆膜法显著提高激光吸收率,可有效降低所需功率或提高速度,改善切割质量。
高质量耗材:使用原厂或高规格的保护镜片、喷嘴、聚焦镜。
优化切割路径:减少空程移动,合理规划切割顺序减少热变形。
定期维护:严格按手册清洁光路(镜片、光纤接头)、检查冷却系统、校准设备。
小批量试切:对于新材料或高要求工件,务必先用边角料进行参数测试和优化。
总结
成功使用激光切割铜板的核心在于:选用光纤激光器、严防反射风险、必须使用高纯氮气、精确设置焦点与喷嘴高度、掌握安全的渐进穿孔技术、根据板材厚度精细调参(功率、速度、气压)。通过严格的设备维护、规范的操作流程和不断的参数优化,激光切割能够为铜板加工提供高效、精密、高质量的解决方案。安全始终是第一要务,尤其在处理高反射材料时。
点击右侧按钮,了解更多激光打标机报价方案。
激光切割机为什么不能切铜
激光切割机为什么不能切铜
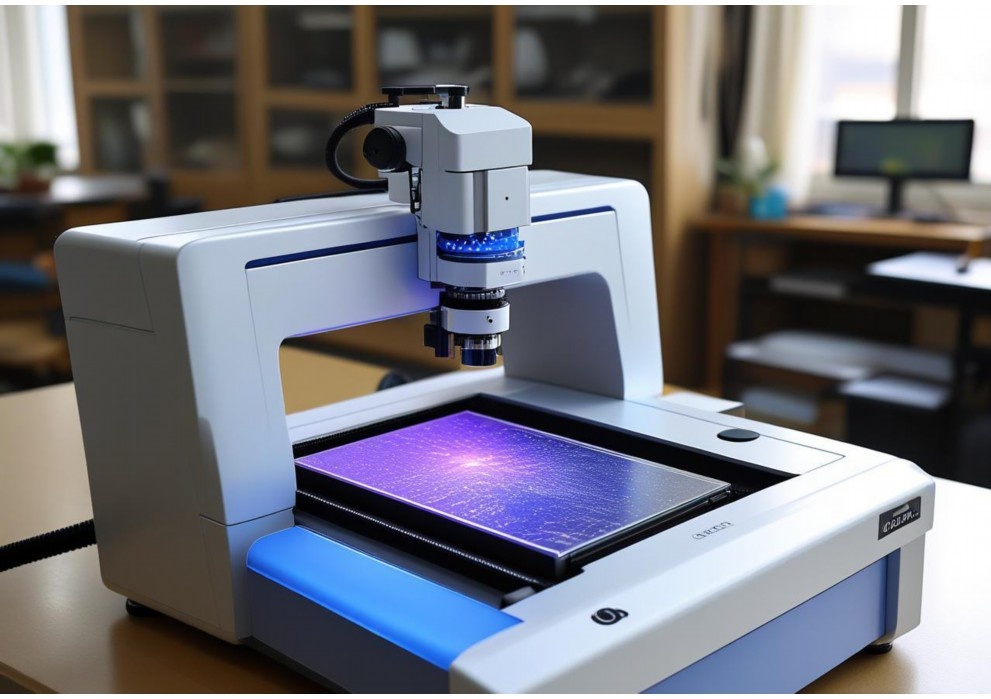
激光切割机“难啃的硬骨头”:为什么切割铜如此棘手?
在金属加工领域,激光切割机以其高精度、高效率和高灵活性成为行业利器。然而,当面对铜这种常见金属时,激光切割机却常常显得“力不从心”,甚至完全无法胜任。这背后并非设备能力不足,而是铜材料特殊的物理性质与激光作用机制之间产生了难以调和的矛盾。深入探究这些矛盾,能帮助我们理解技术局限,并找到更合适的加工方案。
一、核心挑战:铜对激光的“顽固抵抗”
铜对激光的“不合作”态度,源于其一系列独特的物理特性:
1.超高的反射率:
铜,尤其是纯铜和黄铜(铜锌合金),拥有极高的可见光与红外光反射率。对于工业激光切割主力军——波长为10.6微米的CO2激光和1微米左右的光纤/碟片激光——铜在室温下的反射率普遍超过90%,甚至高达95%以上。
后果:绝大部分入射激光能量被直接反射出去,无法有效进入材料内部转化为切割所需的热能。这就像试图用强光照射一面镜子,光会被反射走而无法加热镜子本身。
2.卓越的导热性:
铜是地球上导热性能最好的金属之一,其热传导速度远超钢铁等常用激光切割材料。
后果:即便有少量激光能量被吸收转化为热量,这些热量也会以惊人的速度从激光作用点向四周和材料内部快速扩散。这使得局部区域难以积累起达到铜熔点(约1083°C)所需的、足够集中的高温。热量“瞬间”被传导走,无法有效熔化材料。
3.较高的熔点与特定的熔化特性:
铜的熔点虽然低于钢铁,但结合其高反射率和高导热性,要达到并维持熔化状态仍然困难。
后果:熔融铜的粘度较低,流动性好。在切割过程中,辅助气体(如氧气、氮气)难以有效地将熔融铜从切缝中稳定、连续地吹走。熔融物可能飞溅、粘连或重新凝固在切缝壁或切割头下方,导致切割面质量差(粗糙、挂渣多)、切缝不规则甚至切割中断。
二、安全风险:致命的反射光
铜对激光的强反射特性不仅导致切割困难,更带来了极其严重的安全隐患:
随机反射路径:被铜表面反射的高能激光束方向完全不可预测。
设备损坏:反射光可能直接击中并烧毁激光切割头内部精密的聚焦镜片、传感器或其它光学元件,造成昂贵的设备损坏。
火灾风险:反射的激光束可能击中切割机工作舱内的易燃材料(如电缆、油污、纸张、护罩),引发火灾。
人身伤害:如果防护装置失效或操作不当,反射的激光束甚至可能穿透工作舱逸出,对操作人员或其他在场人员造成严重的眼睛或皮肤灼伤,这种伤害往往是永久性的。这是限制激光切割机加工铜的最重要安全考量之一。
三、技术折中与局限应对
面对铜的挑战,工程师们也发展出一些应对策略,但都存在显著局限:
1.使用高功率光纤/碟片激光器:
原理:1微米波长的近红外激光被铜的吸收率(尤其在熔融状态下)略高于10.6微米的CO2激光(可能从5%提升到30-40%,但仍远低于钢铁)。超高功率(如6kW,8kW甚至更高)可以在一定程度上克服反射和导热损失。
局限:
反射风险依然严重存在,仍需极其严格的防护措施。
主要用于薄铜板(通常≤3mm),切割较厚铜板(>5mm)时,效率急剧下降,质量难以保证,切缝宽且粗糙。
设备成本高昂(高功率激光器价格昂贵)。
切割速度远低于切割同等厚度钢材。
切割质量(特别是断面垂直度、粗糙度)通常不如切割钢材或采用其他方法切割铜。
2.使用绿光或紫外激光器:
原理:更短波长(如绿光532nm、紫外355nm)的激光被铜的吸收率显著提高(可超过50%)。
局限:
设备成本极其昂贵。
功率水平通常较低(远低于光纤/红外激光)。
主要用于精密微加工(钻孔、划线、雕刻薄箔),几乎无法用于工业级厚度的切割。
加工速度慢。
3.特殊工艺与辅助手段:
表面处理:在铜表面涂层(如黑漆、专用吸光材料)或做氧化处理(发黑),暂时提高其对激光的吸收率。
局限:增加工序和成本;涂层可能污染材料或需要后续清理;效果不稳定;不适用于大批量或高精度要求。
改变辅助气体:尝试使用氧气等活性气体,利用氧化反应放热来辅助切割。
局限:效果有限,对高反射高导热问题改善不大,且会在切割面形成较厚的氧化层,通常不适用于需要洁净切割面的场合。
四、更优选择:替代加工技术
鉴于激光切割铜的重重困难与风险,其他加工方法通常是更可靠、更经济、更安全的选择:
1.等离子切割:
利用高温高速等离子弧熔化金属,并用高速气流吹走熔融物。
优点:切割铜(尤其是中厚板)速度较快,成本相对较低,设备普及度高,不受材料反射率影响。
缺点:切割精度和切口质量通常不如激光切割钢材(切缝较宽,斜角较大,热影响区大),毛刺较多,噪音大,烟尘多。
2.水刀切割:
利用超高压水射流(或混合磨料)进行切割。
优点:冷切割,无热影响区、无变形、无材料性质改变;可切割任意厚度的铜;无反射风险;切割精度高。
缺点:切割速度相对较慢;设备投资和运行成本(能耗、磨料)较高;切割厚硬材料时可能产生轻微锥度。
3.冲压/剪切:
适用于大批量、形状相对简单的薄铜板零件。
优点:效率极高,成本低。
缺点:模具成本高,柔性差,不适合复杂轮廓或小批量。
4.线切割:
利用电火花腐蚀原理进行切割。
优点:可切割高硬度导电材料,精度极高,表面质量好。
缺点:切割速度很慢,主要用于精密模具加工,不适合大批量生产。
结论:理解限制,明智选择
激光切割机难以切割铜的核心症结在于铜的超高反射率、卓越导热性以及由此引发的加工效能低下和严重安全风险。虽然超高功率光纤激光器提供了一种有限的解决方案(主要用于薄铜板),但其成本高昂、反射风险仍需严防、切割质量和厚度能力受限。安全因素(反射激光的破坏性)始终是激光切割铜的首要制约。
因此,在需要加工铜材时,务必优先考虑等离子切割、水刀切割、冲压或线切割等替代工艺。这些技术在效率、成本、安全性或加工能力方面,往往比强行使用激光切割更具综合优势。理解材料特性与加工技术的匹配关系,是做出最优决策、保障安全和效率的关键。铜的“高反”特性,让它成为了激光切割王国中一块名副其实的“硬骨头”,也促使制造者不断探索更适配的加工之道——这既是挑战,也是驱动技术革新的动力。
点击右侧按钮,了解更多激光打标机报价方案。
免责声明
本文内容通过AI工具智能整合而成,仅供参考,博特激光不对内容的真实、准确或完整作任何形式的承诺。如有任何问题或意见,您可以通过联系1224598712@qq.com进行反馈,博特激光科技收到您的反馈后将及时答复和处理。