陶瓷基板切割机速度慢如何调快
陶瓷基板切割机速度优化方案
问题分析
陶瓷基板切割机速度慢可能由多种因素造成,需要系统性排查和优化。以下是可能导致速度下降的主要原因:
1. 机械部件磨损:导轨、丝杠等传动部件磨损会增加摩擦阻力
2. 刀具状态不佳:金刚石刀具磨损或安装不当
3. 参数设置不合理:进给速度、主轴转速等参数未优化
4. 冷却系统问题:冷却不足导致设备自动降速保护
5. 控制系统滞后:软件或硬件响应速度慢
6. 材料特性变化:陶瓷基板材质或厚度改变
优化措施
一、机械系统优化
1. 传动系统维护
– 检查并清洁直线导轨和滚珠丝杠,使用专用润滑脂润滑
– 检查皮带或联轴器是否松动,必要时更换
– 调整各轴预紧力至合适水平,过大增加阻力,过小降低精度
2. 刀具管理
– 检查金刚石刀具磨损情况,磨损超过0.02mm应更换
– 确保刀具安装同心度误差<0.01mm - 根据材料选择合适粒度的刀具(建议200-400目) 二、工艺参数优化 1. 速度参数调整 - 逐步提高进给速度(建议从当前值每次增加10%测试) - 优化加速度参数,减少启停时间 - 主轴转速与进给速度匹配(陶瓷切割建议转速3000-6000rpm) 2. 切割路径优化 - 采用高效路径规划,减少空行程 - 对小尺寸切割采用多片同时加工模式 - 优化切入切出方式,减少加减速次数 三、冷却系统改进 1. 冷却液管理 - 确保冷却液流量≥5L/min(具体参考设备规格) - 使用专用陶瓷切割冷却液,定期更换(建议每200小时) - 检查喷嘴位置,确保对准切割区域 2. 温度控制 - 监控主轴温度,异常升温时应检查轴承状态 - 环境温度控制在20±2℃为佳 四、电气系统检查 1. 伺服系统优化 - 检查伺服电机电流是否正常 - 优化伺服增益参数,提高响应速度 - 检查编码器信号是否稳定 2. 控制系统升级 - 更新控制软件至最新版本 - 检查PLC程序是否有优化空间 - 必要时增加运动控制卡提升计算速度 实施步骤 1. 初步检查:记录当前所有参数,进行设备全面点检 2. 参数调整:每次只调整一个参数,观察效果 3. 性能测试:使用标准测试件验证切割质量和速度 4. 稳定运行:找到最佳参数后持续监控至少24小时 5. 标准化:将优化参数记录存档,制定定期维护计划 注意事项 1. 提速过程中必须密切监控切割质量,确保无崩边、裂纹等缺陷 2. 提速应逐步进行,避免急剧变化导致设备损坏 3. 定期进行设备精度校验,速度提升不应牺牲加工精度 4. 记录每次参数调整的效果,建立设备性能数据库 5. 操作人员应接受针对性培训,熟悉优化后的设备特性 通过以上系统性优化,陶瓷基板切割机的加工速度通常可提升20%-40%,同时保持或提高加工质量。建议每季度进行一次全面性能评估和优化调整。
点击右侧按钮,了解更多激光打标机报价方案。
相关推荐
陶瓷基板公司
陶瓷基板公司

陶瓷基板行业深度分析:技术驱动下的高端电子材料领军者
一、行业定义与核心价值
陶瓷基板是以氧化铝(Al₂O₃)、氮化铝(AlN)、氮化硅(Si₃N₄)等陶瓷材料为核心,通过流延成型、高温共烧(HTCC/LTCC)或直接镀铜(DPC)等工艺制成的特种电子基板。其核心价值体现在三大特性:
1. 热管理性能:热导率可达170-230W/(m·K)(如AlN基板),是传统FR-4材料的百倍以上
2. 高频适应性:介电常数可低至6-8(LTCC材料),满足5G毫米波传输需求
3. 结构稳定性:热膨胀系数(CTE)可精准匹配半导体芯片(如AlN与Si的CTE差<0.5×10⁻⁶/℃) 二、市场格局与竞争态势 全球市场呈现"金字塔"结构: - 顶层:日本京瓷(Kyocera)、日本丸和(Maruwa)占据高端市场,掌握军用级AlN基板90%产能 - 中层:台湾同欣电子、中国大陆三环集团主攻车规级市场 - 新兴力量:深圳珈伟新能、合肥圣达实业在Mini LED用微孔陶瓷基板领域实现突破 2023年全球市场规模达28.7亿美元,其中: - 功率模块基板占比42%(IGBT/SiC模块驱动) - 射频器件基板占比31%(5G基站建设需求) - 光学封装基板增长最快(CAGR 19.3%) 三、技术演进路线 第三代技术革命正在进行: 1. 立体化结构:日本TDK开发的3D-MCM技术实现多层陶瓷互连,布线密度提升至500线/mm² 2. 纳米改性:中科院上海硅酸盐所研发的ZrO₂纳米掺杂AlN基板,断裂韧性提高40% 3. 低温共烧突破:华为2012实验室开发的LTCC+方案将烧结温度降至650℃,兼容铜导体 四、核心应用场景 1. 新能源汽车: - SiC功率模块基板需求爆发(单车用量达0.8㎡/辆) - 比亚迪汉EV采用三环集团AlN基板,模块散热效率提升70% 2. 5G通信: - 毫米波AAU需要介电损耗<0.001的LTCC基板 - 华为64TRx天线模组采用京瓷多层陶瓷方案 3. 高端光电: - Mini LED芯片载板要求CTE匹配度<0.3×10⁻⁶/℃ - 苹果Pro Display XDR使用陶瓷基板实现10000nit亮度 五、行业关键壁垒 1. 材料纯度控制:AlN粉体氧含量需<0.02%(相当于99.999%纯度) 2. 共烧技术:金属-陶瓷热膨胀差需控制在Δα<1×10⁻⁶/℃ 3. 精密加工:激光打孔精度要求±5μm(相当于头发丝的1/15) 六、未来发展趋势 1. 复合化:陶瓷-金属复合基板(如AlSiC)在航天领域渗透率提升 2. 智能化:嵌入传感器的自诊断基板(如村田的SmartSubstrate™) 3. 绿色制造:低温烧结技术可降低能耗40%(欧盟2025年强制标准) 七、投资关注点 高价值赛道: - 车规级AlN基板(毛利率>45%)
– 医疗电子用生物相容性基板(如ZrO₂牙科种植体)
– 超高频氮化硅基板(太赫兹应用前瞻布局)
风险提示:
– 原材料波动(钨电极价格2023年上涨37%)
– 技术替代风险(如GaN-on-Si对传统射频基板的冲击)
当前行业正处于”黄金交叉点”:一方面新能源汽车和5G基建推动需求年增25%以上,另一方面国内企业在关键设备(如气氛烧结炉)领域仍存在”卡脖子”环节。具备垂直整合能力(从粉体制备到模块封装)的企业将掌握定价权,预计2025年头部厂商市占率CR3将超过60%。
点击右侧按钮,了解更多激光打标机报价方案。
dbc陶瓷基板
dbc陶瓷基板
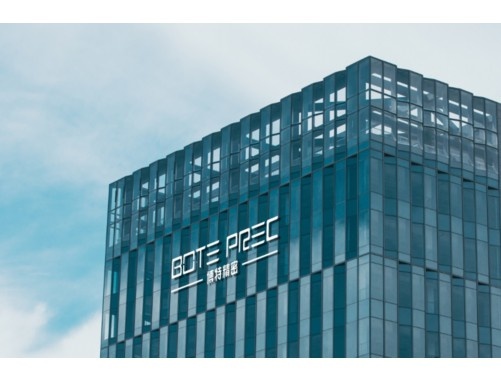
DBC陶瓷基板:高性能电子封装的关键材料
一、DBC陶瓷基板的基本概念
DBC(Direct Bonded Copper,直接覆铜陶瓷基板)是一种通过高温共晶反应将铜箔直接键合在陶瓷表面的复合基板技术。其核心结构由三层组成:上下两层高纯度铜箔(厚度通常为0.1-0.3mm)中间夹着陶瓷绝缘层(常用Al₂O₃或AlN,厚度0.25-1.0mm)。这种独特结构结合了陶瓷的高导热性(AlN可达170-230W/mK)、低热膨胀系数(6-8ppm/℃)以及铜的优异导电性(电阻率≤0.015Ω·mm²/m),成为大功率电子器件封装的理想选择。
二、关键制造工艺与技术特性
1. 表面处理技术:陶瓷表面需经过激光微蚀刻或化学处理形成5-10μm的粗糙度,铜箔则需达到Ra≤0.5μm的镜面级平整度。
2. 共晶键合工艺:在1065-1083℃的H₂/N₂保护气氛中,通过Cu-O共晶反应实现原子级结合,剪切强度可达60MPa以上。
3. 图形化加工:采用紫外激光(波长355nm)或化学蚀刻(FeCl₃溶液)形成50μm精度的电路图形,线宽/线距可达100μm/100μm。
典型性能参数:
– 热导率:Al₂O₃版24-28W/mK,AlN版170-230W/mK
– 击穿电压:≥2.5kV(0.3mm厚度)
– 热循环寿命:-55℃~250℃循环1000次无分层
三、行业应用现状
1. 新能源领域:IGBT模块中DBC基板占比达60%以上,如特斯拉Model 3的逆变器采用0.3mm AlN DBC,热阻低至0.5K/W。
2. 航空航天:星载相控阵雷达T/R组件使用AlN DBC,功率密度提升至30W/cm²。
3. 医疗设备:CT机X射线管模块采用BeO DBC,散热能力较传统方案提升400%。
2023年全球市场规模达18.7亿美元,其中中国占比35%,年增长率12.4%。主要供应商包括罗杰斯(美国)、贺利氏(德国)、同欣电子(中国台湾)等。
四、技术发展趋势
1. 三维集成技术:通过TSV(硅通孔)实现多层DBC堆叠,东芝已开发出10层垂直互连模块。
2. 新型陶瓷材料:Si₃N₄基DBC热导率可达90W/mK,抗弯强度800MPa,丰田中央研究所已试用于混合动力汽车。
3. 微通道冷却:DARPA开发的嵌入式微通道DBC,散热能力达1000W/cm²,为传统方案的5倍。
五、挑战与解决方案
1. 成本问题:AlN基板价格是Al₂O₃的3-5倍,采用流延成型替代干压成型可降低30%原料成本。
2. 焊接可靠性:开发Ag-Cu-Ti活性钎料(熔化温度780℃),使焊接接头强度提升至120MPa。
3. 标准体系缺失:中国电子技术标准化研究院正在制定《电子陶瓷基板热循环试验方法》等6项行业标准。
随着5G基站GaN器件(功耗≥100W/mm)和电动汽车SiC模块(结温≥200℃)的普及,DBC基板正在向超薄化(≤0.1mm)、高精度(线宽≤30μm)方向发展。未来五年,全球市场预计将以15.6%的复合增长率持续扩张,中国本土企业通过突破高纯AlN粉体(纯度≥99.95%)制备技术,有望实现进口替代率40%以上的目标。
点击右侧按钮,了解更多激光打标机报价方案。
陶瓷基板
陶瓷基板
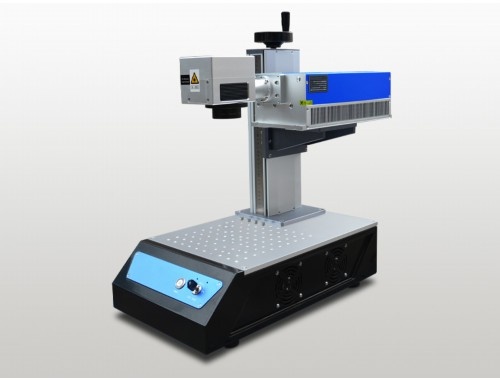
断裂与新生:陶瓷基板在技术文明中的双重角色
在电子设备微型化与高性能化的浪潮中,一种看似脆弱却异常坚韧的材料正悄然支撑着现代科技的脊梁。陶瓷基板——这种由古老陶艺演化而来的高科技产物,以其独特的物理化学特性,在半导体封装、LED照明、电力电子等领域扮演着不可或缺的角色。它的存在,恰如文明进程中的一个隐喻:最脆弱的物质经过火的淬炼,往往能转化为最持久的载体。陶瓷基板不仅承载着电子元件的物理重量,更承载着人类对技术极限的不断挑战。
陶瓷基板的历史可追溯至二十世纪中期,当时电子工业迫切需要一种能够耐受高温且绝缘性能优异的基板材料。传统有机基板在高温环境下易变形老化,金属基板则面临绝缘难题。陶瓷材料——尤其是氧化铝(Al₂O₃)的引入,完美解决了这一困境。随着技术进步,氮化铝(AlN)、氧化铍(BeO)等高性能陶瓷相继登场,热导率从氧化铝的20W/(m·K)跃升至氮化铝的170-230W/(m·K),满足了功率电子器件日益增长的散热需求。在LED领域,陶瓷基板使芯片结温降低30-40℃,显著延长了器件寿命;在汽车电子中,它确保控制单元在发动机舱高温环境下稳定工作。这些数字背后,是材料科学家对陶瓷烧结工艺、显微结构控制的百年探索。
陶瓷基板的卓越性能源自其独特的微观宇宙。电子显微镜下可见,高品质陶瓷基板由尺寸均匀的晶粒紧密堆积而成,晶界清晰洁净。这种结构使其具备三大优势:热导率高——声子(热振动的量子)在规则晶格中传播阻力小;热膨胀系数可调——通过复合不同材料,可匹配硅芯片的4.2ppm/℃;机械强度大——氧化锆增韧陶瓷的断裂韧性可达10MPa·m¹/²。然而,陶瓷的”阿喀琉斯之踵”在于脆性。德国马普研究所通过纳米压痕实验发现,陶瓷裂纹扩展速度可达声速的1/3,这意味着一旦产生微裂纹,结构完整性会瞬间丧失。为克服这一缺陷,现代工艺采用多层复合设计:如活性金属钎焊(AMB)技术在陶瓷与铜层间形成微米级过渡区,剪切强度提升至80MPa以上;激光打孔技术实现垂直互连,导通电阻低于0.1Ω。这些创新使陶瓷基板成为电力电子模块的”骨骼系统”,在高铁变流器中承受300A电流而不失效。
在碳中和背景下,陶瓷基板正推动能源技术革命。光伏逆变器采用陶瓷覆铜板(DBC)后,功率密度提升50%,系统效率突破99%;电动汽车的SiC功率模块依托氮化硅基板,使续航里程增加8-10%。日本京瓷公司开发的低温共烧陶瓷(LTCC)技术,将传感器、无源元件集成于同一基板,减小模块体积70%。更令人振奋的是量子计算领域:超导量子比特需要工作在毫开尔文温度的陶瓷基板,其表面粗糙度需控制在纳米级以避免能量损耗。中国电科38所研制的微波陶瓷基板,介电损耗角正切值低至0.0001,为”九章”量子计算机提供了关键支撑。这些应用揭示了一个深层规律:每当技术遭遇物理极限,陶瓷基板总能通过材料创新开辟新路径。
站在材料科学的视角回望,陶瓷基板的发展轨迹与人类文明进程惊人地相似。如同远古先民将松软黏土烧制成不朽的陶器,现代工程师通过控制原子排列,使脆性陶瓷变得强韧。在5G基站、太空探测器、深海电缆等极端环境中,陶瓷基板默默承担着能量与信息的转换传输,其性能边界不断被重新定义。未来,随着自修复陶瓷、透明导电陶瓷等新材料的出现,这一古老又年轻的平台将继续突破物理限制。或许技术的本质就是如此:在看似不可调和的矛盾——如陶瓷的脆性与韧性、绝缘与导热之间,创造性地找到平衡点。陶瓷基板的故事提醒我们,文明进步的密码往往隐藏在材料微观结构的晶界之中,等待人类去解读与超越。
点击右侧按钮,了解更多激光打标机报价方案。
免责声明
本文内容通过AI工具智能整合而成,仅供参考,博特激光不对内容的真实、准确或完整作任何形式的承诺。如有任何问题或意见,您可以通过联系1224598712@qq.com进行反馈,博特激光科技收到您的反馈后将及时答复和处理。