陶瓷基板切割机保养方法
陶瓷基板切割机保养方法
一、日常保养
1. 清洁工作:每日使用后应及时清理机器表面的灰尘、碎屑和冷却液残留物,特别是导轨、丝杠和工作台面等关键部位。
2. 润滑检查:检查各润滑点(如导轨、丝杠、轴承等)的润滑情况,确保润滑油脂充足且无污染。建议使用专用高速导轨润滑油。
3. 冷却系统维护:检查冷却液浓度和液位,及时补充或更换。保持冷却系统管路畅通,防止堵塞。
4. 刀具检查:检查切割刀具的磨损情况,及时更换磨损严重的刀具,避免影响切割质量。
5. 气压检查:确认气路系统压力正常(通常0.5-0.7MPa),检查气管有无漏气现象。
二、定期保养(每月)
1. 传动系统检查:检查皮带、联轴器等传动部件的松紧度和磨损情况,必要时进行调整或更换。
2. 导轨与丝杠深度清洁:彻底清洁导轨和滚珠丝杠,去除旧油脂和杂质,重新涂抹专用润滑脂。
3. 电气系统检查:检查各接线端子是否松动,清洁电气柜内的灰尘,确保散热良好。
4. 精度校准:使用标准量具检查切割精度,必要时进行机械调整或软件补偿。
5. 过滤器更换:更换气路和冷却系统的过滤器,确保介质清洁。
三、长期保养(每半年或每年)
1. 全面润滑:对所有运动部件进行全面润滑,包括更换轴承润滑脂。
2. 系统检查:检查伺服电机、驱动器等关键部件的工作状态,必要时进行专业检测。
3. 机械结构紧固:检查并紧固所有螺栓连接,特别是底座、立柱等承重结构。
4. 软件升级:检查控制系统软件版本,必要时进行升级以获得更好的性能和功能。
5. 专业维护:建议每年由厂家或专业技术人员进行一次全面检查和维护。
四、特殊注意事项
1. 环境要求:保持设备工作环境清洁干燥,温度控制在20±2℃,湿度40-60%RH。
2. 操作规范:严格按照操作规程使用设备,避免超负荷运行。
3. 异常处理:发现异常声音、振动或加工质量下降时,应立即停机检查。
4. 备件管理:使用原厂或认证的高质量备件,避免使用劣质配件影响设备性能。
5. 记录保存:建立完整的保养记录,包括保养时间、内容和发现的问题,便于追踪设备状态。
通过科学的保养维护,可显著延长陶瓷基板切割机的使用寿命,保持高精度加工能力,降低故障率,提高生产效率。建议企业制定详细的保养计划并严格执行,确保设备始终处于最佳工作状态。
点击右侧按钮,了解更多激光打标机报价方案。
相关推荐
陶瓷基板公司
陶瓷基板公司
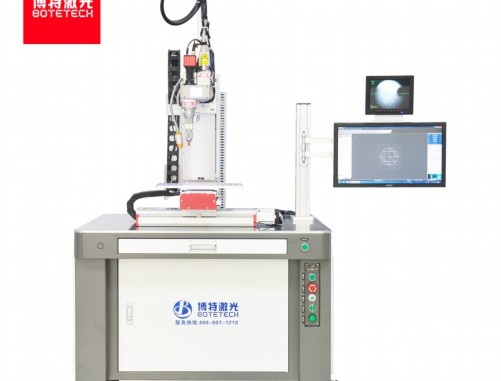
陶瓷基板行业深度分析:技术驱动下的高端电子材料领军者
一、行业概览:高端电子制造的核心材料
陶瓷基板是以氧化铝(Al₂O₃)、氮化铝(AlN)、氮化硅(Si₃N₄)等陶瓷材料制成的功能性基板,凭借高导热性、绝缘性、耐高温和低热膨胀系数等特性,成为功率电子、半导体封装、LED照明、汽车电子等领域的核心材料。随着5G通信、新能源车、第三代半导体(SiC/GaN)的爆发,全球陶瓷基板市场规模预计2025年将突破30亿美元,年复合增长率超过12%。
二、技术壁垒:材料与工艺的双重护城河
1. 材料配方:
– 氧化铝基板(导热率15-30 W/mK):成本低,适用于消费电子。
– 氮化铝基板(导热率170-200 W/mK):高导热,用于大功率半导体。
– 氮化硅基板(抗弯强度>800 MPa):极端环境应用,如航天、电动汽车。
材料纯度(>99.5%)和微观结构控制直接影响性能,需精密烧结技术(如流延成型、高温共烧HTCC)。
2. 工艺难点:
– 激光打孔精度:孔径需控制在50μm以内,满足高密度互连需求。
– 共烧匹配性:多层基板需保证金属线路(如钨、钼)与陶瓷的热膨胀系数匹配。
– 表面金属化:DPC(直接镀铜)、DBC(直接键合铜)工艺决定电路导电性和可靠性。
三、应用场景:新兴需求驱动增长
1. 功率半导体模块:
SiC/GaN器件工作温度超200℃,传统有机基板无法满足,氮化铝基板成为首选,特斯拉Model 3的逆变器即采用DBC陶瓷基板。
2. 汽车电子:
电动汽车的OBC(车载充电机)、BMS(电池管理系统)需求爆发,推动陶瓷基板用量增长,单车价值量可达500-1000元。
3. 光通信与射频:
5G基站AAU中的GaN PA模块依赖高频低损耗陶瓷基板,如罗杰斯的RO4350B Hybrid方案。
四、竞争格局:日企主导,国产替代加速
1. 国际巨头:
– 日本京瓷(Kyocera):全球市占率超30%,HTCC技术领先。
– 日本丸和(Maruwa):专注射频用氮化铝基板,客户含爱立信、华为。
– 美国罗杰斯(Rogers):高频陶瓷基板龙头,5G领域垄断性强。
2. 国内企业:
– 三环集团:氧化铝基板国内第一,氮化铝基板已通过车规认证。
– 富乐华半导体:中日合资企业,DBC技术突破,打入英飞凌供应链。
– 浙江新纳陶瓷:主攻LED封装基板,成本优势显著。
五、未来趋势与挑战
1. 技术迭代:
– 低温共烧(LTCC):适应柔性电子需求,降低能耗。
– 3D打印陶瓷基板:美国Nano Dimension已实现原型开发,可定制复杂结构。
2. 国产替代瓶颈:
– 高端氮化铝粉体依赖日本德山化工(Tokuyama),国产粉体纯度不足。
– DBC工艺设备(如真空钎焊炉)被德国Siemens垄断。
六、结论:高成长赛道中的隐形冠军
陶瓷基板企业需持续投入研发以突破“卡脖子”环节,同时绑定下游头部客户(如华为、比亚迪、台积电)。在半导体国产化和碳中和背景下,具备垂直整合能力(从粉体到模块)的企业将占据价值链顶端,估值溢价显著。短期关注产能扩张,长期看技术创新与跨界应用(如航天热管理、医疗激光器)。
(注:全文基于公开资料与行业调研,数据截至2023年Q3。)
点击右侧按钮,了解更多激光打标机报价方案。
dbc陶瓷基板
dbc陶瓷基板
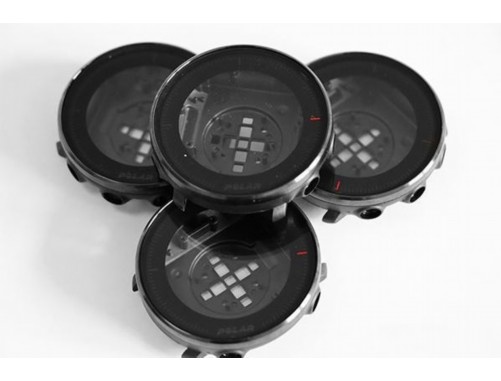
DBC陶瓷基板:高性能电子封装的关键材料
一、DBC陶瓷基板的基本概念
DBC(Direct Bonded Copper,直接覆铜)陶瓷基板是一种通过高温共晶反应将铜箔直接键合在陶瓷表面的复合基板材料。其核心结构由三层组成:上层铜箔(导电层)、中间陶瓷(绝缘层)和下层铜箔(导电层)。这种设计结合了陶瓷的高绝缘性、高热导率和铜的优异导电性,成为高功率电子器件封装的理想选择。
二、材料特性与优势
1. 卓越的导热性能
常用陶瓷材料如氧化铝(Al₂O₃,导热系数24-28 W/mK)和氮化铝(AlN,170-200 W/mK)可高效传导热量,适用于大功率IGBT、LED等发热量大的器件。例如,电动汽车逆变器中DBC基板可将芯片温度降低30%以上。
2. 高电绝缘强度
陶瓷层的击穿电压可达20 kV/mm以上,远高于传统PCB材料(FR4约20 kV/mm),保障高电压环境下的安全运行。
3. 与芯片匹配的热膨胀系数
AlN(4.5×10⁻⁶/K)和SiC(4.0×10⁻⁶/K)的热膨胀系数接近,可有效减少热循环导致的焊接层疲劳。实验数据显示,DBC基板在-40~150℃循环1000次后仍保持结构完整。
4. 大电流承载能力
铜层厚度通常为0.1-0.3 mm,截面积是普通PCB导线的50倍以上,可承载数百安培电流。例如,风电变流器模块中单块DBC基板可稳定通过200A电流。
三、关键制造工艺
1. 表面预处理
陶瓷需经超声清洗和等离子活化,铜箔表面粗糙度控制在0.5-1.2 μm以增强结合力。研究表明,Ra=0.8 μm时剪切强度可达45 MPa。
2. 共晶键合技术
在1065℃的N₂+H₂氛围中,铜与陶瓷通过Cu-O共晶反应形成10-50 μm厚的过渡层。精确控制氧含量(50-200 ppm)是关键,氧含量不足会导致结合强度下降30%以上。
3. 图形化加工
采用激光刻蚀(精度±25 μm)或化学蚀刻(线宽最小100 μm)形成电路图形。新型UV激光加工可使线宽降至50 μm,满足SiC模块的高密度互连需求。
四、典型应用场景
1. 新能源领域
光伏逆变器中使用AlN-DBC基板,功率密度提升至30 W/cm³,转换效率达99%。特斯拉Model 3的电机驱动模块采用多层DBC结构,散热性能提升40%。
2. 轨道交通
高铁牵引变流器中,DBC基板工作温度可达175℃,寿命超过10万小时。西门子Sitrains系列产品通过DBC技术将模块体积缩小60%。
3. 航空航天
卫星电源系统采用镀金DBC基板,在真空环境下热阻低于0.5 K/W,满足15年免维护要求。
五、技术发展趋势
1. 三维集成技术
东芝开发的立体DBC结构将热阻降低至传统结构的1/3,用于5G基站PA模块散热。
2. 新型陶瓷材料
氮化硅(Si₃N₄)基DBC抗弯强度达800 MPa,适用于振动环境。日本京瓷的Si₃N₄-DBC已应用于航空发动机控制系统。
3. 微纳结构铜层
德国贺利氏采用多孔铜技术,使有效表面积增加5倍,电流密度承载能力提升300%。
六、挑战与解决方案
– 成本问题:AlN基板价格是Al₂O₃的3-5倍,通过流延成型工艺可将成本降低40%。
– 焊接缺陷:采用Ag烧结技术替代传统焊锡,接头孔隙率<5%,热导率提升至250 W/mK。 - 标准缺失:国际电工委员会(IEC)正在制定DBC产品标准(IEC 63209),预计2024年发布。 结语 随着第三代半导体器件的普及,DBC陶瓷基板市场预计将以12.8%的年增长率扩张,2025年全球规模将突破8亿美元。未来通过材料创新和工艺优化,DBC技术将继续推动电力电子设备向高效化、小型化方向发展。
点击右侧按钮,了解更多激光打标机报价方案。
陶瓷基板
陶瓷基板
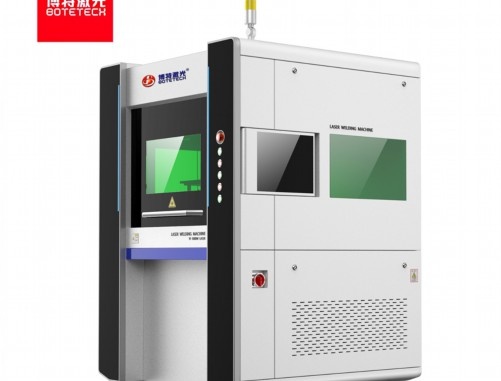
断裂与新生:陶瓷基板的技术哲学沉思
在电子工业的精密迷宫中,陶瓷基板如同一位沉默的智者,以其脆性与韧性并存的矛盾特质,演绎着现代科技文明的深层悖论。这种由无机非金属材料构成的精密载体,既是电子元件连接的物理基础,也是技术哲学思考的绝佳样本。当我们的手指滑过智能手机屏幕,当医疗CT机精准扫描人体组织,当航天器穿越大气层的炽热考验,陶瓷基板都在不可见的维度默默承担着热与力的双重考验。它的存在提醒我们:最脆弱的结构往往支撑着最前沿的科技,这正是技术文明发展的一个精妙隐喻。
陶瓷基板的物质特性构成了一部微观层面的抗争史诗。氧化铝(Al₂O₃)、氮化铝(AlN)、氧化铍(BeO)等陶瓷材料在电子工业中的广泛应用,源于它们独特的物理化学性质—高导热、高绝缘、低膨胀系数。这些专业术语背后,是材料科学家与自然规律的持续对话。法国哲学家加斯东·巴什拉在《科学精神的形成》中指出:”物质在微观层面展现的性格,远比宏观表象更为复杂。”陶瓷基板的热导率可达30W/(m·K),是普通塑料的数百倍;其热膨胀系数却可低至4×10⁻⁶/℃,与半导体芯片完美匹配。这种精确到近乎苛刻的参数平衡,使得陶瓷基板成为功率电子、LED照明、射频模块等高端应用的不二之选。在5G基站的能量转换器中,在电动汽车的逆变器模块里,陶瓷基板承受着数百次热循环考验而不失效,这种”脆弱中的坚韧”挑战着我们对材料性能的传统认知。
制造工艺的演进史,折射出人类对完美无止境的追求。从早期的厚膜印刷技术到现在的低温共烧陶瓷(LTCC)工艺,陶瓷基板的制作已成为一门融合材料学、电子学、机械工程的综合艺术。德国技术哲学家弗里德里希·德绍尔曾提出”技术内在必然性”概念,认为技术发展遵循其内在逻辑。陶瓷基板制造工艺的演变完美诠释了这一观点—从简单的单层基板到复杂的多层三维结构,从毫米级线路到微米级精密布线,技术进化的每一步都回应着电子设备小型化、集成化的内在需求。日本京瓷公司开发的”AMB活性金属钎焊”技术,能在陶瓷与金属间形成原子级结合;美国CoorsTek研发的”直接镀铜DPC”工艺,实现了5微米以下的线路精度。这些突破不仅解决了热应力导致的界面剥离问题,更重新定义了电子封装的可靠性标准。在无尘车间里,纳米级的陶瓷粉末经过等静压成型、高温烧结、精密加工,最终蜕变为承载兆瓦级功率的电子基板,这一过程本身就是现代工业文明的微型景观。
应用领域的持续扩张,展现了陶瓷基板作为平台技术的生命力。在新能源汽车的电机控制器中,陶瓷基板将碳化硅(SiC)芯片产生的热量高效导出,使系统效率突破90%;在航天器的电源系统中,它耐受着-150℃到+120℃的极端温度波动;在植入式医疗设备里,它的生物惰性保障了长期使用的安全性。这种跨领域的适应性,呼应了加拿大传播理论家马歇尔·麦克卢汉”媒介即讯息”的洞见—陶瓷基板不仅是电子元件的被动载体,更是重塑应用可能性的主动因素。当紫外LED通过陶瓷基板实现3000小时以上的稳定工作,它改写了杀菌消毒的技术路径;当雷达系统的TR模块因陶瓷基板而缩小体积50%,它重新定义了军用电子装备的设计范式。在这些应用中,陶瓷基板超越了物理基板的角色,成为系统创新的催化剂。
站在材料科学与电子工程的交叉点回望,陶瓷基板的技术轨迹给予我们超越具体应用的哲学启示。比利时物理化学家伊利亚·普里高津的耗散结构理论认为,开放系统在远离平衡态时可能产生自组织的有序结构。陶瓷基板的发展历程恰如这一理论的注脚—在热力学、电动力学、材料力学的多重约束下,它不断演化出更优的结构形态。未来,随着三维集成、异质封装等技术的成熟,陶瓷基板或将进化为立体的电子”骨架”,在更微观尺度上协调能量与信息的流动。这种进化不仅关乎技术进步,更隐喻着人类文明如何在脆弱性与适应性的辩证中寻找前行动力。
陶瓷基板的故事告诉我们:真正的技术韧性不在于无懈可击的坚固,而在于在明确自身限度的前提下,仍能开辟出新的可能性空间。当我们的文明日益依赖于这些看不见的微观结构时,或许应当学会欣赏这种脆弱与坚韧的辩证法—就像陶瓷基板一样,承认断裂的可能,却依然承担着连接未来的使命。
点击右侧按钮,了解更多激光打标机报价方案。
免责声明
本文内容通过AI工具智能整合而成,仅供参考,博特激光不对内容的真实、准确或完整作任何形式的承诺。如有任何问题或意见,您可以通过联系1224598712@qq.com进行反馈,博特激光科技收到您的反馈后将及时答复和处理。