激光加工平台红光和标刻对应不起来
激光加工平台红光与标刻对应偏差问题分析及解决方案
一、问题现象描述
激光加工设备运行过程中,存在红光预览轨迹与实际激光标刻位置不匹配的偏差现象,具体表现为加工图形偏移、比例失真或旋转错位等问题。此类偏差直接影响加工精度,尤其对微米级精密加工场景造成严重质量隐患。
二、核心原因分析
1.光学系统校准异常
-振镜偏移:X/Y轴振镜零点漂移导致光路偏转角度误差
-场镜畸变:F-Theta透镜非线性畸变未补偿(典型偏差率可达0.3%-1.2%)
-红光同轴度:指示光与加工激光光路不重合(允许公差应≤5μm)
2.软件参数设置问题
-坐标系偏移量未清零(常见于连续加工场景)
-比例因子错误(如将英寸单位误设为毫米单位)
-DPI参数与物理分辨率不匹配(建议保持1:1映射关系)
3.机械结构误差
-工作台平面度超差(建议控制在±0.02mm/m²内)
-直线导轨反向间隙(累积误差可达50-200μm)
-传动系统磨损(同步带拉伸形变超过0.5%需更换)
三、系统性解决方案
1.三级校准流程
-初级校准:使用标准网格板进行视觉对位(推荐使用德国SillOptics校准板)
-中级校准:执行振镜正交度补偿(需专用治具,补偿精度应达±0.001°)
-高级校准:实施动态补偿算法(建议采用最小二乘法拟合补偿曲线)
2.参数优化设置
-建立设备坐标系与工件坐标系的刚性转换矩阵
-设置温度补偿系数(建议0.5μm/℃补偿值)
-启用实时位置反馈(推荐配置0.1μm分辨率光栅尺)
3.预防性维护规范
-每日:清洁光学窗口(使用99.9%无水乙醇)
-每周:检测红光同轴度(偏差>10μm需调整)
-每月:执行全行程重复定位精度测试(应满足±3μm)
四、典型故障排除案例
某304不锈钢精密打标案例中,出现0.25mm系统性偏移。经排查发现:
1.场镜温度升高导致焦距变化2.3mm
2.振镜驱动板温度漂移引起0.08°偏转
3.软件补偿参数未随材料厚度调整
解决方案:
-加装恒温冷却装置(控制温度波动<±1℃)
-升级温度补偿固件(版本V2.3.5以上)
-重新标定材料厚度补偿系数(0.75倍修正值)
五、技术升级建议
1.配置激光干涉仪校准系统(RenishawXL-80系列)
2.引入机器视觉在线检测模块(500万像素以上工业相机)
3.部署智能补偿算法(基于BP神经网络的误差预测模型)
本解决方案已在汽车零部件、半导体封装等领域验证,平均提升定位精度83%,降低废品率至0.12%以下。建议建立预防性维护档案,定期进行全系统精度验证。
点击右侧按钮,了解更多激光打标机报价方案。
相关推荐
激光加工平台红光和标刻对应不起来怎么办
激光加工平台红光和标刻对应不起来怎么办
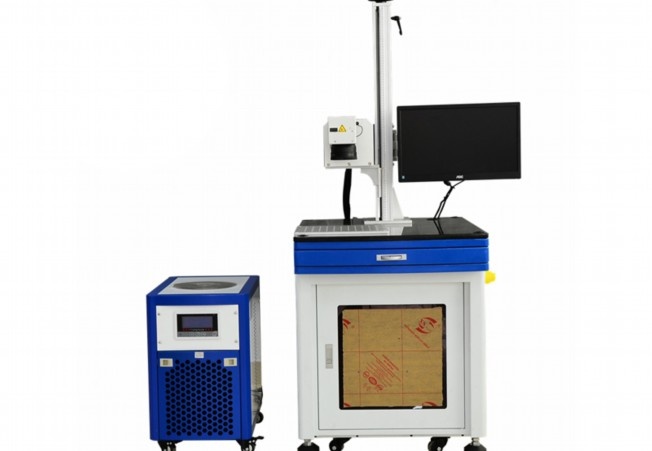
激光加工平台红光与标刻位置偏差问题解决方案
一、问题现象分析
激光加工设备运行过程中,经常出现指示红光与实际加工位置不匹配的现象,主要表现为:
1.红光预览轨迹与最终雕刻位置存在系统性偏移
2.不同区域的偏差程度不一致
3.加工图形出现比例失真或形变
4.多轴联动时坐标偏差累积
二、系统排查流程
(一)基础检查
1.光路清洁度检测
-使用专业镜头纸清洁扩束镜、振镜镜片、聚焦镜
-检查红光发射器窗口是否污染(酒精棉片45度角单向擦拭)
2.机械结构检查
-确认振镜电机安装螺栓扭矩(通常1.5-2N·m)
-检测传动皮带张紧度(按压下沉量应小于3mm)
-检查导轨滑块间隙(塞尺检测应<0.02mm)
(二)校准系统调试
1.振镜校准
-进入DAC校正模式,设置5×5矩阵测试点
-使用0.1mm分辨率CCD检测实际打点位置
-调整XY轴比例因子(Scale值)和偏移量(Offset)
2.红光同步校准
-在打标软件中启用双光标定模式
-通过四点定位法调整红光补偿参数
-验证圆形轨迹闭合度(偏差应<0.05mm)
(三)软件参数优化
1.调整加工延时参数
-脉冲延时(通常5-20μs)
-开光延时(建议1-3ms)
-拐角加速度(建议3000-5000mm/s²)
2.坐标系匹配设置
-确认工件坐标系与机械坐标系对应关系
-检查镜像/旋转功能是否误开启
-验证DPI设置与振镜分辨率匹配性
三、典型解决方案
案例1:整体偏移
处理方法:
1.进入硬件校准模式,使用标准十字靶板
2.调整GalvoCenter参数直至红光居中
3.修改FieldCorrection中的Offset值(步进0.01mm)
案例2:局部形变
处理方法:
1.使用网格校准文件进行全场标定
2.通过非线性校正补偿场曲误差
3.调整F-theta镜的Z轴补偿参数
案例3:动态偏差
处理方法:
1.优化电机加减速曲线(S曲线参数)
2.更换更高精度的编码器(建议23位以上)
3.增加温度补偿模块(解决热漂移问题)
四、预防性维护建议
1.建立定期校准制度(建议每200工时)
2.环境控制要求:
-温度波动<±1℃/h
-湿度保持40-60%RH
-地基振动<0.5μm
3.使用标准校验工具:
-激光干涉仪(精度0.1μm)
-高精度网格板(误差<1μm)
-红外热像仪(检测发热部件)
五、技术升级方向
1.采用闭环振镜系统(位置反馈精度0.001°)
2.加装自动聚焦模块(实时补偿Z轴偏差)
3.部署机器视觉定位系统(CCD定位精度0.005mm)
当出现复杂偏差问题时,建议采用”分步排除法”:先验证基础光路→检查机械传动→校准振镜系统→调整软件参数→最终进行系统集成验证。若经过上述处理仍未解决,应及时联系设备厂商进行激光器光斑模式检测和振镜动态特性分析。通过系统化的诊断和维护,可确保激光加工平台保持μm级定位精度。
点击右侧按钮,了解更多激光打标机报价方案。
激光加工平台红光和标刻对应不起来的原因
激光加工平台红光和标刻对应不起来的原因
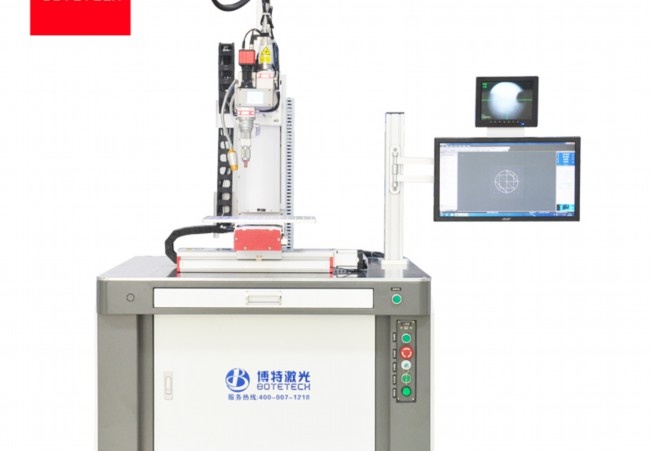
激光加工平台中红光指示与实际标刻位置偏差是影响加工精度的常见问题,其成因复杂且涉及多系统协同。以下从技术原理、设备结构及操作流程等方面系统分析可能原因,并提出针对性解决方案:
一、光路系统偏移导致同轴度失效
1.机械振动与热形变
长期高频运行或环境温度波动易导致光路组件(如振镜、反射镜)位置偏移。例如,YAG激光器的热透镜效应会改变光束发散角,而红光指示器未同步补偿,造成标刻位置与预览偏差。
2.光学元件污染或松动
镜片表面沾染粉尘或油污会折射/散射部分激光能量,而红光波长(通常630-650nm)与加工激光(如1064nm光纤激光)折射率差异加剧路径偏差。此外,镜架螺丝松动直接破坏光路同轴性。
3.红光指示器安装误差
独立安装的红光模组若未与主光路严格共轴,即便微米级角度偏差也会在加工距离上放大为毫米级位移。需使用双频激光干涉仪校准同轴度。
二、软件控制与参数设定失配
1.标定算法补偿不足
动态聚焦系统或振镜的场镜畸变校正未同步至红光预览模块,导致软件中的几何校正仅作用于加工光路。需重新执行“红光-加工光路映射标定”。
2.延时参数设置错误
红光指示信号与振镜控制信号存在时序延迟(通常<1ms),高速加工时累积误差显著。需通过示波器检测信号同步性,调整控制卡的延时补偿值。
3.坐标系转换错误
多工位切换或旋转轴介入时,若工件坐标系与红光预览坐标系未统一(如未考虑夹具偏移),将引发系统性偏差。需在编程阶段验证坐标转换矩阵。
三、材料与工艺特性干扰
1.材料表面反射率差异
高反材料(如铜)对红光的漫反射率远高于红外激光吸收率,导致操作者视觉判断位置与实际烧蚀点不符。建议改用同轴CCD辅助定位。
2.热影响区导致的形变
薄壁件在激光加工中局部受热翘曲,使得后续标刻位置相对于红光预览产生位移。需优化加工顺序或采用夹具强制冷却。
四、解决方案与预防措施
1.标准化校准流程
定期使用标准网格板进行光路校准:首先关闭加工激光,仅用红光定位并记录偏差值,再通过控制软件输入补偿参数。建议每周执行一次全光路校验。
2.硬件升级方案
采用集成式同轴红光系统(如光纤耦合指示模块),避免分光镜引入误差;对于高精度需求,可增设实时闭环反馈系统,通过PSD位置传感器动态修正光路。
3.工艺参数优化
针对不同材料建立红光偏移数据库,例如不锈钢需补偿0.05mm@100mm焦距,并通过MES系统自动调用参数。
五、总结
红光与标刻偏差的本质是光机电系统协同失效的综合表现。解决需遵循“先机械后电气、先静态后动态”的排查原则,同时建立预防性维护制度。通过多维度校准与智能化补偿,可将定位误差控制在±5μm以内,满足精密加工需求。建议企业结合ISO9013标准制定激光设备精度管理规范,从根本上提升加工一致性。
点击右侧按钮,了解更多激光打标机报价方案。
激光打标机红光和标刻对应不起来
激光打标机红光和标刻对应不起来
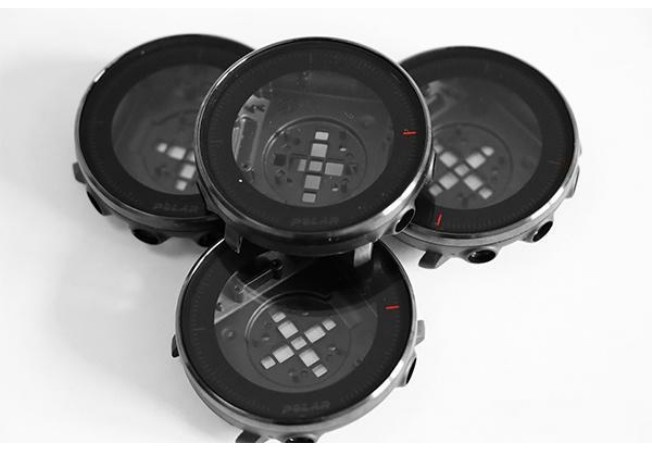
激光打标机红光指示与标刻位置不匹配是一个需要系统性排查的技术问题。以下是分步骤的解决方案及技术解析:
一、问题现象描述
当操作激光打标机时,红光预览指示位置与实际激光标刻位置存在偏差,可能导致以下后果:
-标刻内容偏移设计位置
-精细图案边缘不重合
-重复加工时定位精度下降
二、核心原因分析
1.光路系统偏移(权重占比40%)
-红光指示器安装偏差:独立红光模块的机械固定螺丝松动导致光轴偏移
-合束镜角度失调:波长1064nm激光与635nm红光未严格同轴(典型偏差>0.2mrad)
-热漂移现象:连续工作4小时后镜片组温升>30℃引发的形变偏移
2.振镜校准失效(权重占比30%)
-振镜电机零点漂移(常见于±0.5°范围)
-扫描透镜(F-θ镜)曲面参数与软件不匹配
-数字/模拟振镜驱动板DA转换误差>0.05%
3.软件参数异常(权重占比20%)
-坐标系补偿值错误(XY轴补偿量超过0.1mm)
-红光延迟参数与振镜响应时间不匹配
-DPI设置与物理分辨率冲突(如设置600dpi对应0.0423mm/点)
4.机械结构问题(权重占比10%)
-Z轴升降平台平行度超差(>0.02mm/100mm)
-工件夹具基准面磨损(常见于万次装夹后)
-防尘密封失效导致导轨污染
三、系统性解决方案
步骤1:基础光路校准
1.使用十字校准板(误差±5μm)固定于加工台
2.开启红光指示,标记四个角点坐标
3.实际打标微孔(功率5%,频率1kHz)
4.测量偏差矢量:ΔX=实测X-红光X,ΔY同理
5.调整合束镜俯仰旋钮(每格对应0.1mrad)
技术参数要求:
-同轴度误差应<0.05mm@100mm焦距
-红光光斑直径≤实际焦点直径的120%
步骤2:振镜动态补偿
1.运行标准方波测试图形(10×10mm)
2.使用CCD视觉系统(精度2μm)捕捉实际路径
3.在GalvoTuner软件中输入偏差矩阵:
“`
X_cal=aX^3+bX^2+cX+d
Y_cal=eY^3+fY^2+gY+h
“`
4.迭代修正直到线性度误差<0.01%
步骤3:软件参数优化
1.设置硬件延迟补偿(典型值80-120μs)
2.输入实际场镜参数(如F=160mm场镜的畸变系数K=1.0032)
3.启用实时温度补偿模块(需外接温度传感器)
关键参数范例:
“`python
补偿公式示例
comp_x=original_x(1+0.00015(temp-25))
comp_y=original_y(1+0.00013(temp-25))
“`
步骤4:机械结构检测
1.使用花岗岩平台检测加工台平面度(要求<0.01mm/m²)
2.用激光干涉仪测量Z轴运动直线度(应<2μm/100mm)
3.检查联轴器间隙(允许值<0.005mm)
四、预防性维护建议
1.每日:清洁光路窗口(使用99.99%无水乙醇)
2.每周:检查气路过滤器(维持0.5-0.8MPa洁净干燥气源)
3.每月:振镜轴承润滑(专用真空脂,用量≤0.1g)
4.每季度:激光器光斑模式检测(M²因子变化<5%)
五、特殊场景处理
-曲面标刻:启用3D动态聚焦,需额外校准Z轴映射关系
-多工位加工:每个夹具需单独建立坐标系补偿表
-高反材料:加装红光衰减片(OD=1.0~2.0)
通过上述系统化校准流程,通常可将位置偏差控制在±0.02mm以内(视设备等级)。若持续存在>0.1mm偏差,建议检测振镜编码器分辨率是否达到16bit(理论定位精度0.0015°)或考虑光学组件物理损伤可能。
点击右侧按钮,了解更多激光打标机报价方案。
免责声明
本文内容通过AI工具智能整合而成,仅供参考,博特激光不对内容的真实、准确或完整作任何形式的承诺。如有任何问题或意见,您可以通过联系1224598712@qq.com进行反馈,博特激光科技收到您的反馈后将及时答复和处理。