激光加工平台精度等级
激光加工平台精度等级解析及应用指南
(一)精度等级的核心要素
激光加工平台的精度等级由定位精度、重复定位精度和加工综合精度三大指标构成:
1.定位精度:±0.01mm(高端设备)至±0.1mm(工业级设备)
2.重复精度:通常为定位精度的1/3-1/2
3.综合精度:受机械、光学、控制系统的协同影响
(二)影响精度的关键子系统
1.机械传动系统
-直线电机精度:±0.5μm/m(高端型号)
-滚珠丝杠等级:C0-C5级(ISO标准)
-导轨直线度:0.003mm/1000mm(精密级)
2.光学聚焦系统
-光束质量M²值:1.1(单模光纤激光器)
-聚焦光斑直径:15-50μm(波长相关)
-振镜扫描精度:≤5μrad(高端扫描头)
3.智能控制系统
-闭环控制分辨率:0.1μm(纳米级平台)
-温度补偿精度:±0.5℃/m(主动补偿系统)
-振动抑制能力:>90%(主动减震平台)
(三)行业精度需求矩阵
1.微电子制造:≤±3μm(晶圆切割/打标)
2.医疗器械加工:±5-10μm(心脏支架雕刻)
3.汽车白车身焊接:±0.1mm(连续焊缝)
4.航空航天构件:±0.05mm(钛合金切割)
5.模具表面处理:±20μm(激光淬火)
(四)精度提升技术方案
1.动态补偿技术
-实时位置反馈(编码器分辨率达27bit)
-前瞻算法预测(50ms轨迹预判)
-热变形补偿(多点温控+AI建模)
2.先进校准方法
-激光干涉仪校准(精度0.5ppm)
-球杆仪圆度检测(0.1μm级)
-机器视觉在线测量(5μm级)
3.环境控制标准
-恒温车间:20±0.5℃
-地基振动:<2μm/s(RMS)
-空气洁净度:ISOClass6(百级)
(五)设备选型决策模型
建议采用多维度评估体系:
1.材料特性:铜铝等高反材料需特殊处理
2.加工厚度:每增加1mm碳钢,焦点深度变化0.2mm
3.生产节拍:精度每提升1级,产能可能下降15-30%
4.ROI分析:高精度设备投资回收期通常2-3年
(六)行业发展趋势
1.复合精度控制:融合5G+边缘计算实现μ级响应
2.智能误差补偿:基于数字孪生的预测性校准
3.新型传动方案:磁悬浮直驱技术突破纳米级瓶颈
4.多波长协同:紫外+红外复合加工精度提升方案
随着工业4.0的深入,现代激光加工平台正从单一精度指标竞争转向全流程精度管控体系构建。建议用户在设备选型时,建立包含短期加工需求、中期技术升级、长期工艺发展的三维评估模型,在精度投入与经济效益间取得最佳平衡。
点击右侧按钮,了解更多激光打标机报价方案。
相关推荐
激光加工平台精度等级标准
激光加工平台精度等级标准
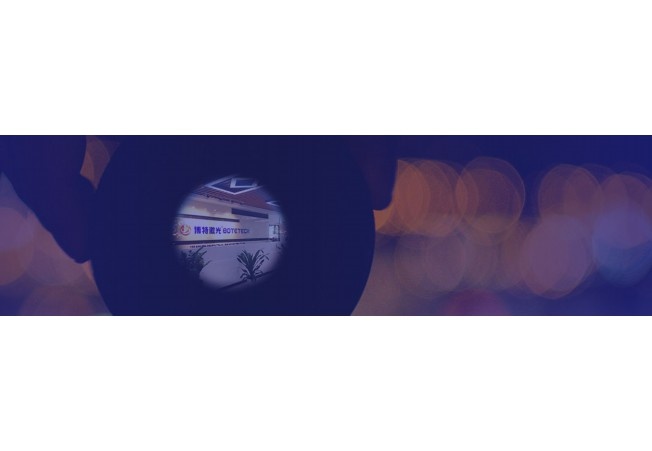
以下为关于激光加工平台精度等级标准的详细阐述:
激光加工平台精度等级标准与技术解析
激光加工技术因其非接触、高能量密度和高灵活性等优势,在精密制造领域占据重要地位。其加工精度直接决定产品质量,因此建立科学严谨的精度等级标准体系至关重要。本文将从核心参数、检测方法、行业应用差异及优化策略等方面系统解析激光加工平台的精度标准。
一、精度等级的核心评价指标
1.定位精度(PositioningAccuracy)
指激光头实际移动位置与理论坐标的偏差,通常以μm级衡量。高端设备可达±2μm,普通工业级为±5-10μm。直接影响切割/刻蚀的轮廓准确性。
2.重复定位精度(Repeatability)
同一位置多次定位的离散程度,反映设备稳定性。半导体设备要求≤±1μm,金属加工设备多在±3μm内。
3.加工精度(MachiningAccuracy)
综合光束质量、运动控制等因素的最终加工效果。例如精密钻孔的圆度误差需<5μm,微结构刻线宽度波动需<±1μm。
4.光束质量(BeamQualityFactor,M²)
M²值越接近1,光束聚焦能力越强。精密加工要求M²<1.2,确保光斑直径稳定(如紫外激光可达10μm以下)。
二、精度检测方法与工具
1.激光干涉仪检测
采用He-Ne激光干涉系统,动态测量运动轴线性定位误差,分辨率可达0.1μm。
2.标准试件加工验证
通过加工标准网格图案(如ISO9013试件),使用光学显微镜或三坐标测量仪(CMM)量化尺寸偏差。
3.实时闭环反馈系统
集成光栅尺、编码器等传感器,实时修正位置误差。如FARO激光跟踪仪可实现动态精度监控。
三、行业应用精度差异化标准
|行业领域|典型精度要求|关键影响因素|
||–|-|
|半导体封装|±0.5μm(切割道对准)|温度波动、振动隔离|
|医疗器械精密打标|线宽≤20μm,深度误差<5%|光束模式稳定性、材料热效应|
|航空航天结构件|轮廓公差±0.05mm|多轴协同精度、材料变形补偿|
四、提升加工精度的关键技术
1.机械结构优化
-采用大理石基座降低热变形
-直线电机驱动替代滚珠丝杠,消除反向间隙
-空气轴承导轨减少摩擦振动
2.智能控制算法
-前馈补偿(Feedforward)技术预判惯性误差
-自适应PID参数调节应对负载变化
-基于AI的工艺参数自优化系统
3.环境控制体系
-恒温车间(±0.1℃)降低热漂移
-主动隔振平台隔离6Hz以上振动
-正压洁净环境减少粉尘干扰
五、行业标准与认证体系
-国际标准:ISO13694(激光功率密度分布)、VDI3258(激光切割质量)
-国内规范:GB/T26135-2010(激光加工机械安全标准)
-行业认证:UL认证(电气安全)、CE认证(电磁兼容)
结语
激光加工平台的精度标准需结合具体工艺需求动态调整。随着超快激光、多轴联动等技术的发展,微纳级加工精度(<100nm)已成为前沿方向。企业应建立全生命周期的精度管理体系,从设备选型、工艺开发到日常维护实现闭环控制,以持续提升制造竞争力。
(全文约850字)
点击右侧按钮,了解更多激光打标机报价方案。
激光加工平台精度等级是多少
激光加工平台精度等级是多少
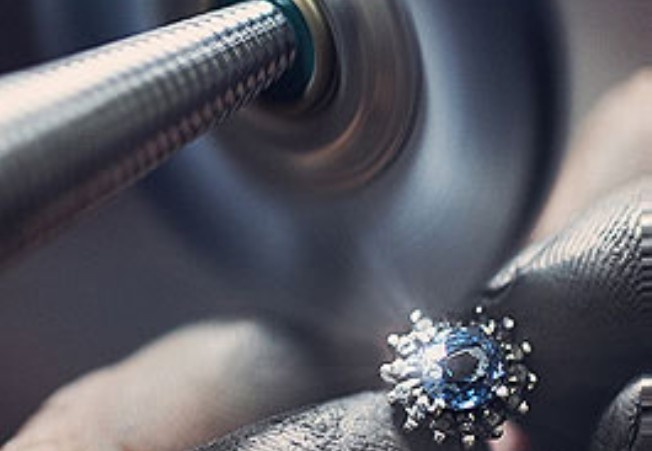
激光加工平台的精度等级是衡量其加工质量和技术水平的重要指标,直接影响加工件的尺寸精度、表面质量及生产效率。根据应用领域、设备类型和技术配置的不同,激光加工平台的精度通常可分为微米级(μm)、亚微米级(0.1μm以下)甚至纳米级(nm),具体表现因设备性能和加工需求而异。以下从多个维度详细解析其精度等级及影响因素。
一、激光加工精度的定义与分类
激光加工精度主要包括定位精度(设备移动轴的实际位置与理论位置的偏差)和重复定位精度(多次定位同一位置的一致性),通常以±Xμm或±Xmm表示。例如:
-通用型激光切割机:定位精度±0.05mm,重复精度±0.03mm;
-高精度微加工设备:定位精度±1μm,重复精度±0.5μm;
-超精密激光系统(如半导体加工):精度可达纳米级。
不同工艺的精度要求差异显著:
-激光切割:金属板材加工精度通常为±0.1mm,精密薄材可达±0.01mm;
-激光焊接:焊缝对位精度需控制在±0.02mm以内;
-激光打标/雕刻:分辨率可至10μm以下,适用于精细图文。
二、影响精度的核心因素
1.机械结构设计
-导轨与传动系统:高刚性直线导轨(如THK、HIWIN品牌)和滚珠丝杠可减少摩擦和背隙,确保运动平稳。采用直线电机技术可进一步提升定位精度至±0.5μm。
-结构稳定性:铸铁或花岗岩基座能有效抑制振动和热变形。
2.控制系统与算法
-伺服电机与编码器:高分辨率编码器(如23位绝对值编码器)配合闭环控制,实时反馈修正误差。
-运动控制算法:前瞻控制(Look-ahead)和加速度优化算法可减少拐角过冲,提升复杂路径的跟踪精度。
3.光学系统性能
-激光束质量:单模光纤激光器的M²值接近1,光束聚焦直径更小(如10μm级),适用于高精度切割。
-振镜扫描系统:高速振镜的重复定位精度达±5μrad,配合F-theta透镜可在大幅面内保持微米级精度。
4.环境与工艺控制
-温湿度调控:恒温车间(±1°C)可降低材料热膨胀误差,如钢材温度每变化1°C,100mm长度变化约1.2μm。
-辅助气体与焦点控制:实时Z轴调焦系统(如电容式传感器)可将焦点漂移控制在±0.01mm内。
三、典型应用场景的精度需求
1.工业制造领域
-汽车零部件切割:精度±0.1mm,确保装配兼容性;
-PCB微孔加工:孔径精度±5μm,满足高密度电路需求。
2.精密电子与半导体
-晶圆切割:刀痕宽度≤10μm,崩边<2μm; -FPC柔性电路加工:激光剥线精度±3μm。 3.医疗与微机械 -心脏支架切割:切缝宽度0.02mm,边缘粗糙度Ra<0.8μm; -微流控芯片加工:通道尺寸误差±1μm。 四、提升精度的关键技术 1.闭环反馈系统:通过光栅尺或激光干涉仪实时监测位置,动态补偿误差。 2.多轴联动校准:采用激光跟踪仪对XYZ轴进行空间精度补偿,降低阿贝误差。 3.人工智能优化:机器学习算法分析加工数据,预测热变形并自动调整参数。 五、未来发展趋势 -复合加工技术:结合视觉定位(精度±2μm)与激光加工,实现智能补偿; -飞秒激光应用:冷加工减少热影响区,加工精度突破至100nm级别; -模块化设计:用户可自定义精度模块,如更换高精度振镜或光学组件。 总结 激光加工平台的精度等级由设备硬件、控制系统及环境管理共同决定。当前主流工业设备精度在微米级,而尖端科技领域已向亚微米乃至纳米级迈进。用户需根据材料特性、加工复杂度及成本预算综合选择,同时注重定期维护(如光学镜片清洁、导轨润滑)以维持精度稳定性。未来,随着自适应光学和AI技术的融合,激光加工精度有望实现更智能化的突破。
点击右侧按钮,了解更多激光打标机报价方案。
激光加工平台精度等级要求
激光加工平台精度等级要求
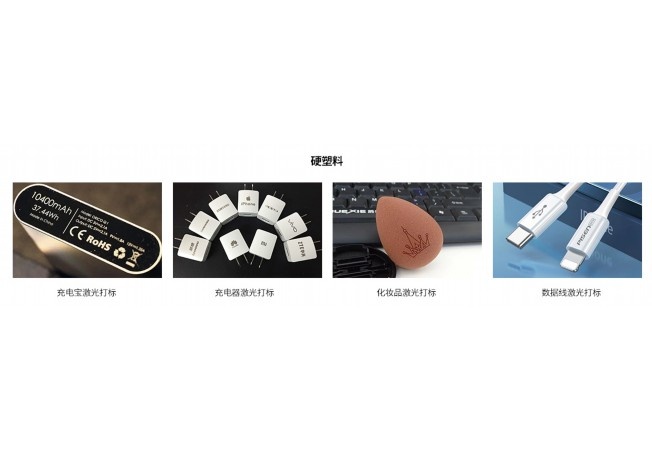
激光加工技术因其高效率、非接触式加工和高精度等优势,在精密制造、微电子、医疗器械等领域得到广泛应用。激光加工平台的精度等级直接决定了加工质量与工艺适用范围,其精度要求需从机械运动精度、光路系统精度、环境控制等多维度进行综合考量。以下是激光加工平台精度等级要求的系统分析:
一、精度等级的核心指标
激光加工平台的精度等级通常由以下核心参数定义:
1.定位精度(PositioningAccuracy)
指平台实际位置与目标位置的绝对偏差,通常要求达到±1-5μm(微米级)。高精度场景(如半导体光刻)需达到±0.1μm以下。
2.重复定位精度(Repeatability)
多次返回同一位置的偏差范围,是衡量稳定性的关键指标。工业级平台需优于±1μm,超精密平台则要求±0.05μm以内。
3.加工精度(ProcessingAccuracy)
综合激光光斑质量、运动控制、热变形等因素后的实际加工误差。例如,PCB钻孔需控制在±5μm,而OLED屏幕切割则需≤±3μm。
二、不同应用场景的精度需求分级
1.工业级加工(中等精度)
-典型应用:金属板材切割、汽车零部件焊接。
-要求:定位精度±10μm,重复精度±5μm。主要依赖高刚性机械结构与闭环伺服控制。
2.精密加工(高精度)
-典型应用:消费电子部件(如手机中框)、医疗器械微结构。
-要求:定位精度±2μm,光斑直径≤20μm。需采用直线电机、气浮导轨,并配备激光干涉仪反馈系统。
3.超精密加工(纳米级精度)
-典型应用:光通信器件、MEMS传感器、集成电路封装。
-要求:亚微米级定位(±0.1μm),激光波长稳定性≤0.01nm。需恒温实验室环境,并集成压电陶瓷微动台补偿误差。
三、影响精度的关键因素与解决方案
1.机械系统误差
-因素:导轨直线度、丝杠反向间隙、结构热变形。
-优化措施:采用大理石基座减少振动,使用预紧式滚珠丝杠或磁悬浮驱动,并引入温度传感器实时补偿。
2.光路系统误差
-因素:激光光束质量(M²值)、聚焦镜畸变、振镜扫描非线性。
-优化措施:选用单模光纤激光器(M²<1.1),配置动态聚焦模块,并通过软件校正振镜畸变。 3.控制算法与反馈系统 -因素:PID参数漂移、编码器分辨率不足。 -优化措施:采用自适应控制算法(如模糊PID),搭配高分辨率光栅尺(纳米级)或激光干涉仪。 四、未来精度提升的技术趋势 1.多轴协同控制技术 通过六轴联动平台补偿空间几何误差,实现复杂曲面的高精度加工。 2.在线检测与闭环修正 集成机器视觉或共聚焦传感器,实时监测加工结果并反馈调整参数。 3.智能补偿算法 基于大数据和AI预测热变形、机械磨损等误差源,实现主动补偿。 五、结论 激光加工平台的精度等级需根据具体工艺需求进行定制化设计。工业级应用侧重于成本与效率的平衡,而超精密加工则需在材料、控制算法和环境稳定性上投入更高成本。随着智能制造的发展,高精度、多轴化、智能化将成为激光加工平台的核心竞争力,推动微纳制造与高端装备的持续升级。
点击右侧按钮,了解更多激光打标机报价方案。
免责声明
本文内容通过AI工具智能整合而成,仅供参考,博特激光不对内容的真实、准确或完整作任何形式的承诺。如有任何问题或意见,您可以通过联系1224598712@qq.com进行反馈,博特激光科技收到您的反馈后将及时答复和处理。