pcb电路板激光切割机速度慢如何调快
PCB电路板激光切割机速度慢的调优方法
一、速度慢的原因分析
PCB电路板激光切割机速度慢可能由多种因素造成,主要包括:
1. 激光功率设置不当:功率不足导致需要多次切割
2. 切割参数不合理:速度、频率等参数未优化
3. 光学系统问题:镜片污染或焦距不准
4. 运动系统限制:机械结构或驱动系统性能不足
5. 材料特性影响:不同PCB材料需要不同处理方式
6. 软件设置问题:路径规划或控制参数不当
7. 设备老化:长期使用导致性能下降
二、调优方法详解
1. 激光参数优化
功率调整:
– 逐步提高激光功率(建议每次增加5-10%)
– 确保不超过设备最大额定功率
– 注意功率与速度的平衡关系
频率调整:
– 对于PCB切割,通常使用较高频率(20-100kHz)
– 频率过高可能导致能量不足,需与功率配合调整
占空比优化:
– 适当增加脉冲占空比可提高切割效率
– 但需避免材料过热
2. 运动系统优化
加速度设置:
– 增加X/Y轴的加速度参数
– 确保机械结构能承受增加的动态负载
最大速度调整:
– 在控制软件中提高最大运动速度
– 需考虑拐角处的减速需求
运动轨迹优化:
– 使用软件中的”高速模式”或”优化路径”功能
– 减少不必要的空程移动
3. 光学系统维护与调整
镜片清洁:
– 定期清洁聚焦镜和保护镜
– 使用专用镜片清洁剂和无尘布
焦距校准:
– 确保焦点位置准确
– 不同厚度材料需调整焦距
光束质量检查:
– 使用光束分析仪检测光斑质量
– 必要时调整光路
4. 切割工艺优化
分层切割策略:
– 对于厚板可采用多次浅切割
– 设置合理的切割层数和每层深度
气体辅助优化:
– 调整辅助气体压力和类型
– 氮气切割通常效果优于空气
预热处理:
– 对某些材料可预先加热提高切割效率
– 控制预热温度避免损伤材料
5. 软件设置优化
路径规划:
– 选择最优切割顺序
– 减少激光开关次数
拐角处理:
– 适当降低拐角速度保持精度
– 使用圆角代替尖角减少减速
控制算法调整:
– 尝试不同的插补算法
– 优化前瞻控制参数
三、调优注意事项
1. 安全第一:任何调整都应在安全范围内进行
2. 逐步调整:每次只改变一个参数,观察效果
3. 记录参数:建立参数数据库供日后参考
4. 材料测试:对新材料应进行切割测试
5. 设备限制:不超出设备设计能力
6. 维护计划:建立定期维护保养制度
四、长期性能保持建议
1. 建立设备维护日志
2. 定期校准光学系统
3. 保持环境清洁稳定
4. 及时更换易损件
5. 操作人员定期培训
6. 软件及时升级
通过以上方法的系统应用,可显著提高PCB激光切割机的工作效率,同时保证切割质量。建议用户根据自身设备型号和加工需求,制定个性化的优化方案。
点击右侧按钮,了解更多激光打标机报价方案。
相关推荐
激光切割机的切割参数怎样调节
激光切割机的切割参数怎样调节
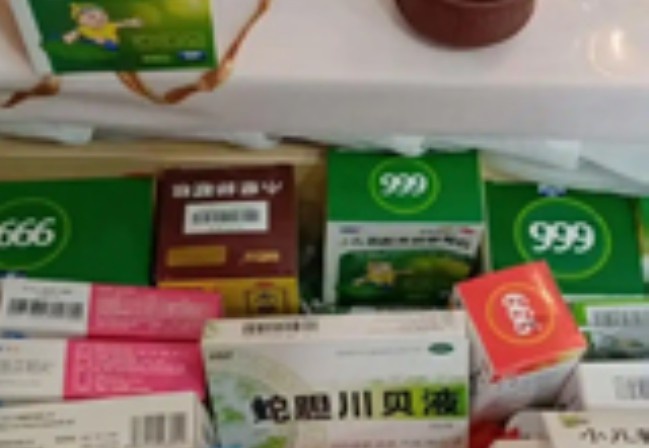
激光切割机切割参数调节指南
一、激光切割参数概述
激光切割机的切割参数调节是确保加工质量和效率的关键环节。合理的参数设置能够显著提高切割质量、延长设备寿命并降低生产成本。主要调节参数包括激光功率、切割速度、焦点位置、气体压力及喷嘴高度等。
二、核心参数调节方法
1. 激光功率调节
激光功率直接影响切割能力和切口质量。功率过高可能导致材料过度熔化甚至烧损,功率不足则无法完全穿透材料。调节原则:
– 薄板材料(1-3mm):使用较低功率(500-1500W)
– 中厚板(3-10mm):中等功率(1500-3000W)
– 厚板(10mm以上):高功率(3000W以上)
– 需根据材料反射率调整,高反射材料(如铜、铝)需要更高功率
2. 切割速度优化
切割速度与材料厚度、激光功率密切相关:
– 速度过快:切口不整齐,可能出现未切透现象
– 速度过慢:材料过热,切口过宽,热影响区增大
– 经验公式:速度(mm/min)=(功率(W)×效率系数)/(材料厚度(mm)×材料系数)
3. 焦点位置控制
焦点位置对切口质量和切割能力有决定性影响:
– 表面聚焦:适用于薄板精密切割
– 内部聚焦:适合中厚板切割
– 底部聚焦:用于厚板切割
– 一般规律:切割厚度增加,焦点位置应相应下移
三、辅助参数设置
1. 辅助气体选择与压力
– 氧气:用于碳钢切割,提供额外热能(压力0.5-5bar)
– 氮气:用于不锈钢、铝材等,防止氧化(压力5-20bar)
– 空气:经济选择,适用于非金属和薄金属(压力4-8bar)
– 气压过高可能导致切口上宽下窄,过低则排渣不畅
2. 喷嘴选择与高度
– 喷嘴直径:薄板用小口径(1.0-1.5mm),厚板用大口径(2.0-3.0mm)
– 喷嘴高度:通常0.5-2.0mm,需与焦点位置配合调节
– 喷嘴状态:定期检查,磨损或污染会严重影响切割质量
四、材料特性考量
不同材料需要不同的参数组合:
1. 碳钢:可使用氧气辅助,功率适中,速度较快
2. 不锈钢:需氮气保护,较高功率,中等速度
3. 铝及合金:高功率,低速度,氮气保护
4. 铜及合金:极高功率(因高反射率),特殊镀膜喷嘴
5. 非金属:低功率,高速度,空气辅助
五、参数优化流程
1. 初步设定:根据材料类型和厚度选择预设参数
2. 试切测试:进行小范围切割试验
3. 质量评估:检查切口垂直度、粗糙度、挂渣情况
4. 参数微调:根据评估结果逐步优化各参数
5. 稳定生产:确定最佳参数组合后固定设置
六、常见问题及调整
1. 底部挂渣:增加气压或功率,降低速度
2. 切口过宽:检查焦点位置,可能需重新对焦
3. 切割不透:提高功率或降低速度
4. 材料过热变形:提高速度或降低功率,增加辅助气体流量
5. 切割面倾斜:调整焦点位置,检查喷嘴同轴度
七、安全注意事项
1. 参数调整前确保设备处于待机状态
2. 功率调整需逐步进行,避免突变
3. 气体压力设置不得超过设备额定值
4. 新参数首次运行时需密切观察切割过程
5. 记录每次参数调整效果,建立参数数据库
通过系统化的参数调节和优化,可以充分发挥激光切割机的性能,实现高质量、高效率的切割加工。实际应用中需结合具体设备型号、材料特性和加工要求进行灵活调整。
点击右侧按钮,了解更多激光打标机报价方案。
电路板厂家线路板厂家
电路板厂家线路板厂家
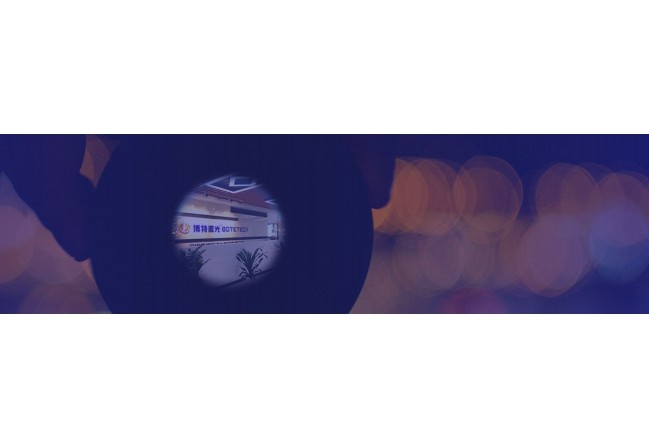
电路板厂家与线路板厂家:行业概述与关键选择因素
一、行业定义与产品范围
电路板(PCB)和线路板是电子设备的核心组件,用于连接和支持电子元器件。尽管术语常被混用,但严格来说:
– PCB(Printed Circuit Board):泛指所有印刷电路板,包括单层、多层和柔性板。
– 线路板:可能特指单层或简单电路载体,但实际使用中两者界限模糊。
厂家通常提供从设计到生产的全流程服务,产品涵盖:
– 消费电子(手机、电脑)
– 工业设备(控制板、电源模块)
– 汽车电子(传感器、导航系统)
– 医疗设备(监测仪、成像设备)
二、市场现状与竞争格局
1. 全球市场:2023年全球PCB产值超800亿美元,中国占比约50%,主导中低端市场,高端领域(如IC载板)仍由日韩企业主导。
2. 国内分布:
– 珠三角(深圳、东莞):消费电子集中区,中小型厂家密集。
– 长三角(苏州、上海):高端制造基地,外资企业聚集。
– 中西部(湖北、四川):成本优势区域,政府扶持转移产能。
3. 竞争趋势:
– 价格战激烈,利润率压缩至5%-10%。
– 环保要求(如无铅工艺)推高合规成本,淘汰小作坊。
三、核心生产技术对比
| 技术类型 | 适用场景 | 技术难点 |
|–||–|
| 刚性PCB | 手机主板、电脑显卡 | 高多层(12+层)对位精度 |
| 柔性FPC | 可穿戴设备、折叠屏 | 材料延展性与焊接可靠性 |
| HDI板 | 5G模块、微型传感器 | 激光钻孔与微细线路蚀刻 |
| 陶瓷基板 | 大功率LED、汽车电子 | 热膨胀系数匹配 |
创新方向:
– 材料:高频PTFE基材(用于毫米波雷达)、可降解基板。
– 工艺:加成法制造(减铜污染)、3D打印电路。
四、选择厂家的关键指标
1. 资质认证:
– 基础:ISO9001、UL认证。
– 特殊行业:汽车电子需IATF 16949,医疗需ISO 13485。
2. 产能与交期:
– 样板厂:3-5天快板服务,适合研发。
– 量产厂:月产能超10万平方米,承诺交期偏差<5%。 3. 成本控制: - 批量订单降价梯度(如1k片降价15%)。 - 材料替代方案(FR4与铝基板成本差可达40%)。 4. 技术支持: - DFM(可制造性设计)反馈速度。 - 高频信号完整性仿真能力。 五、行业挑战与未来展望 1. 痛点: - 原材料波动(铜价、环氧树脂)。 - 人才短缺(高端工艺工程师缺口达20%)。 2. 机遇: - 新能源车:PCB用量较传统车增加300%(雷达、电池管理)。 - AI服务器:高多层板(20层+)需求激增。 结论: 选择厂家需平衡技术能力与成本,建议: - 高端项目优先考察长三角企业(如沪电股份、深南电路)。 - 消费电子可考虑珠三角供应链集群,缩短交付周期。 - 长期合作需审核厂家研发投入(占比≥5%营收为佳)。 (注:本文数据基于2023年行业报告,实际选择需结合最新调研。)
点击右侧按钮,了解更多激光打标机报价方案。
激光切割机调试方法
激光切割机调试方法
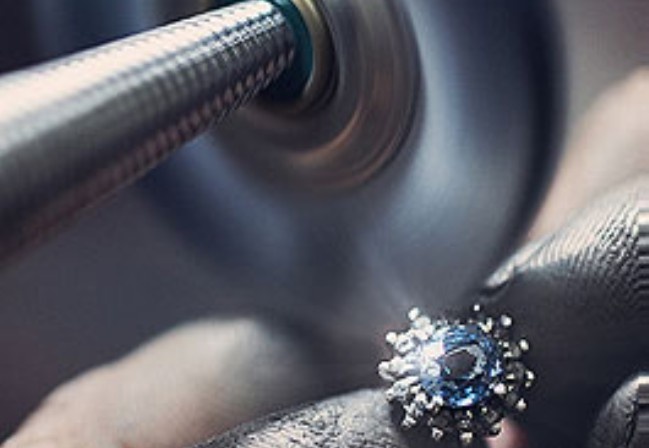
激光切割机调试方法
一、调试前的准备工作
1. 设备检查:
– 确认激光切割机各部件安装牢固,无松动现象
– 检查光路系统是否清洁,镜片无污染或损坏
– 确保冷却系统工作正常,水温在设定范围内
2. 安全确认:
– 检查急停按钮功能正常
– 确认防护装置完好有效
– 准备必要的防护装备(护目镜等)
3. 材料准备:
– 准备调试用材料(建议使用与生产相同材质的废料)
– 准备辅助工具:卡尺、水平仪、气压表等
二、机械系统调试
1. 机床水平调整:
– 使用精密水平仪检测机床水平度
– 调整机床地脚,确保X/Y轴方向水平误差≤0.02mm/m
2. 导轨与传动系统检查:
– 检查导轨润滑情况,补充适量润滑油
– 确认传动带/丝杠张力适当,无异常磨损
3. 运动精度测试:
– 执行机床回零操作,确认各轴回零准确
– 使用激光干涉仪或标准量块检测定位精度和重复定位精度
三、光学系统调试
1. 光路校准:
– 使用红光指示器初步调整光路同轴度
– 通过贴膜法检查聚焦镜位置,确保光斑居中
– 调整反射镜角度,使激光束与机床运动轴线平行
2. 聚焦镜检查:
– 清洁聚焦镜表面
– 确认焦距设置与加工材料匹配
– 检查聚焦镜冷却系统工作正常
3. 激光功率检测:
– 使用功率计检测实际输出功率
– 对比设定功率与实际功率的偏差,必要时进行校准
四、切割参数调试
1. 基础参数设置:
– 根据材料类型和厚度设置初始参数(功率、速度、频率等)
– 设置合理的穿孔参数(穿孔时间、穿孔高度等)
2. 辅助气体调试:
– 检查气体管路密封性
– 调整气体压力(氧气切割通常0.3-0.8MPa,氮气切割0.8-1.2MPa)
– 确认气体纯度符合要求(特别是氮气纯度应≥99.99%)
3. 焦点位置调试:
– 通过阶梯切割法确定最佳焦点位置
– 记录不同材料厚度对应的焦点偏移量
五、试切割与参数优化
1. 试切样品:
– 切割简单几何图形(方孔、圆孔等)
– 检查切缝质量、垂直度和毛刺情况
2. 参数优化:
– 调整功率、速度、气压等参数组合
– 通过正交试验法寻找最优参数组合
– 记录不同材料的最佳切割参数
3. 精度验证:
– 切割标准测试图形(如十字线、同心圆等)
– 使用测量仪器检测尺寸精度(误差应≤±0.1mm)
六、常见问题处理
1. 切割质量不佳:
– 毛刺过多:检查气体纯度、压力,调整焦点位置
– 切缝过宽:降低功率或提高切割速度
– 底部挂渣:调整气体类型或压力
2. 设备异常报警:
– 检查报警代码对应手册
– 常见问题:水温异常、气压不足、光学组件过热等
3. 运动系统异常:
– 检查驱动器参数
– 确认机械传动部件无卡阻
– 检测限位开关状态
七、调试记录与文件
1. 详细记录所有调试参数和结果
2. 建立设备调试档案
3. 编制标准化操作手册
调试完成后,应进行至少8小时的连续试运行,确认设备稳定性后方可投入正式生产。定期(建议每500工作小时)重复关键调试项目,确保设备保持最佳工作状态。
点击右侧按钮,了解更多激光打标机报价方案。
免责声明
本文内容通过AI工具智能整合而成,仅供参考,博特激光不对内容的真实、准确或完整作任何形式的承诺。如有任何问题或意见,您可以通过联系1224598712@qq.com进行反馈,博特激光科技收到您的反馈后将及时答复和处理。