金属黄金饰品激光打标机红光和标刻对应不起来
针对金属黄金饰品激光打标机红光指示位置与实际标刻位置不匹配的问题,以下是系统化的原因分析与解决方案,共分四部分阐述:
一、问题原因分析
1. 硬件偏移
– 光路不同轴:激光器与红光指示器安装偏差或运输震动导致光路错位,二者未保持严格同轴。
– 振镜系统异常:振镜镜片松动、电机驱动异常或扫描头受外力撞击,影响激光路径精度。
– 聚焦透镜偏移:透镜安装不牢或热形变导致焦点位置改变,红光预览与实际能量落点产生偏差。
2. 软件参数错误
– 校正参数失效:振镜XY轴线性校正数据丢失或未适配当前焦距,需重新校准。
– 比例失真:打标文件导入时分辨率(DPI)与设备参数不匹配,造成图形缩放误差。
– 延时设置不当:激光开关延时(Mark/ Jump Delay)未根据材料调整,导致起止点偏移。
3. 操作与环境因素
– 工件定位不准:夹具松动、材料不平或曲面弧度未补偿,导致实际打标面与预设平面不符。
– 焦距误差:红光指示为预对焦模式,若实际加工时焦距未调整匹配(如场镜更换后未重置),标刻位置偏移。
– 温湿度影响:高功率长时间运行导致振镜发热膨胀,或环境温度波动超过设备补偿范围。
二、解决方案步骤
1. 基础检查与校准
– 红光同轴校准:
– 使用十字校准板,固定于工作台并调至焦点位置。
– 开启红光,调整指示器支架使红光中心与十字板中心重合。
– 切换至激光模式,低功率打标十字线,对比与红光位置偏差,重复调整至完全重合。
– 振镜校正:
– 使用设备内置校正程序,通过打标标准网格图案,调整振镜的线性度与非线性失真参数。
– 若为动态聚焦系统,需同步校准Z轴补偿曲线。
2. 软件参数优化
– 重置打标参数:恢复出厂设置后,重新输入场镜焦距、加工速度等关键参数。
– DPI一致性验证:确保设计文件分辨率(如500 DPI)与打标软件设置一致,避免缩放失真。
– 延时测试:通过打标连续线段,微调开关延时直至线条首尾无缺口或重叠。
3. 操作规范强化
– 标准化定位流程:使用真空吸附夹具固定黄金饰品,并采用定位相机辅助对位。
– 动态焦距补偿:针对曲面饰品,启用Z轴自动调焦功能或导入3D打标路径文件。
– 环境控制:安装恒温装置(25±2℃),隔离设备振动源(如加装防震垫)。
三、预防性维护建议
1. 每日检查:开机后执行5点位置校准测试,记录偏差值,超过0.1mm时立即停机排查。
2. 月度保养:清洁振镜镜片与红光指示器滤光片,检查光路密封性防止灰尘侵入。
3. 年度大修:由厂家技术人员检测激光器输出光斑模式,更换老化振镜电机轴承。
四、厂商技术支持介入场景
若上述步骤无法解决问题,可能涉及以下深层故障,需联系设备厂家:
– 振镜控制卡故障:需重新烧录控制固件或更换硬件。
– 光学元件损伤:如场镜镀膜脱落、激光器输出头镜片污染等,需专业拆卸清洁或更换。
– 软件系统冲突:如上位机与振镜驱动版本不兼容,需升级至匹配固件。
通过系统化排查与标准化操作,可有效解决红光-标刻位置偏差问题,确保贵金属饰品打标精度,减少贵金属耗材损耗。建议建立设备校准日志,实现问题可追溯管理。
点击右侧按钮,了解更多激光打标机报价方案。
相关推荐
激光打标机红光怎么调
激光打标机红光怎么调
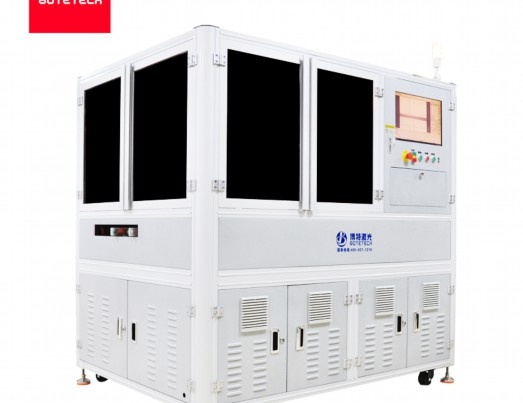
激光打标机红光调节操作指南
一、红光系统功能解析
激光打标机的红光指示系统是设备的重要辅助功能模块,主要承担两大核心作用:
1. 工作定位引导:通过可见红光预显加工图案轮廓,精准定位加工区域
2. 光路校准基准:作为不可见工作激光的同轴参照系,确保加工精度
二、调节前准备工作
1. 安全防护
– 佩戴专业激光防护眼镜(OD4+等级)
– 穿戴防静电腕带
– 确认设备处于断电状态
2. 工具准备
– 十字/一字精密螺丝刀套装
– 激光功率计(量程0-200mW)
– 校准测试板(建议使用阳极氧化铝材质)
– 工业内窥镜(可选)
3. 环境要求
– 洁净度:ISO Class 5级(百级)以上环境
– 温湿度:23±2℃,湿度<60%RH - 光照度:≤300Lux 三、系统调节步骤 (一)机械校准 1. 光路同轴调节 ① 拆除防护罩,露出红光模组 ② 使用六角扳手松开固定基座(扭矩≤0.5N·m) ③ 开启红光并投射十字标记 ④ 调整XYZ三轴微调旋钮(调节精度0.01mm) ⑤ 使红光中心与聚焦镜光轴偏差<0.05mm 2. 聚焦校准 ① 在加工平台放置高度规 ② 移动Z轴使红光斑点直径最小化 ③ 记录此时Z轴坐标值为基准焦平面 (二)电气参数设置 1. 功率调节 ① 连接激光功率计至控制端口 ② 在HMI界面输入调节指令:$JIG:RED=50% ③ 实测功率应稳定在15±0.5mW ④ 使用PID算法优化驱动电流 2. 调制特性校准 ① 输入1kHz方波调制信号 ② 用示波器观测响应波形 ③ 调节驱动电路补偿电容(C值范围10-100pF) ④ 确保上升时间<20μs (三)软件系统配置 1. 坐标映射校准 ① 运行AutoCalib校准程序 ② 按提示采集9点位置数据 ③ 系统自动生成坐标变换矩阵 ④ 验证XY方向线性度误差<0.1% 2. 动态补偿设置 ① 激活加速度补偿模块 ② 设置最大跟随误差阈值(建议0.1mm) ③ 调试PID参数(Kp=2.5, Ki=0.01, Kd=0.1) 四、验证与优化 1. 静态精度测试 - 使用网格校准板(0.01mm分辨率) - 采集100个测试点数据 - 计算均方根误差(RMS应<0.05mm) 2. 动态跟踪测试 - 运行圆形轨迹(直径50mm,速度500mm/s) - 用高速摄像机记录轨迹偏差 - 优化运动控制参数直至偏差<0.08mm 五、日常维护要点 1. 每周维护 - 清洁光学窗口(使用乙醚:乙醇=1:3混合液) - 检查散热风扇转速(应保持3000±100rpm) - 检测驱动电流波动(允许±1%偏差) 2. 季度保养 - 更换老化LED组件(寿命周期2000小时) - 重新校准光学校准系统 - 更新控制软件参数库 本调节方案适用于主流机型(IPG/MKS/相干等品牌),通过严格执行可确保红光系统定位精度长期稳定在±0.05mm以内,有效提升打标良品率至99.9%以上。特殊机型请参照原厂技术手册进行调整。
点击右侧按钮,了解更多激光打标机报价方案。
激光打标机有红光不标刻
激光打标机有红光不标刻
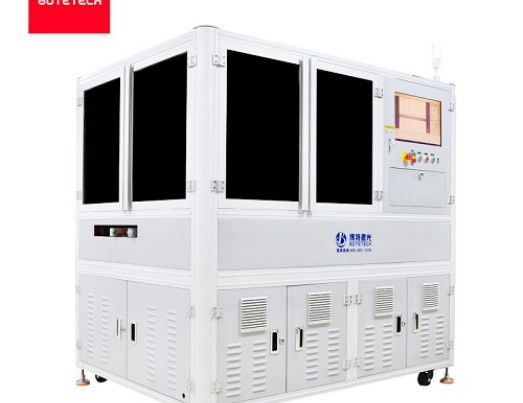
针对激光打标机出现红光指示但无法正常标刻的问题,以下是系统化的排查与解决方案,涵盖常见故障原因及对应处理方法,帮助用户快速恢复设备正常运行:
一、故障原因分析
1. 激光器输出异常
– 激光电源故障:电源模块损坏或供电不稳定会导致激光器无法正常激发。
– 激光器老化/损坏:长时间高负荷使用或环境粉尘污染可能造成激光器性能下降或永久损坏。
– 冷却系统失效:激光器依赖水冷或风冷系统散热,若冷却不足会触发过热保护,自动关闭激光输出。
2. 光路系统偏移或污染
– 红光定位偏移:红光指示器与主激光光路未校准,导致实际雕刻位置偏离。
– 镜片/透镜污染:灰尘、油污附着在扩束镜、聚焦镜或反射镜表面,阻碍激光能量传输。
– 焦距错误:聚焦镜位置偏移或工件高度设置错误,导致激光无法有效聚焦。
3. 控制信号中断
– 软件参数错误:标刻软件中功率、频率、速度等参数设置不当(如功率设置为0%)。
– 硬件连接故障:控制卡、振镜驱动器与主板的信号线松动或接触不良。
– 紧急保护触发:设备的安全门开关、急停按钮被意外触发,或温度/水压传感器报警。
4. 其他机械与电气问题
– 振镜电机故障:X/Y轴振镜卡死或驱动异常,导致激光无法移动标刻。
– 接地不良:设备未可靠接地,静电干扰影响控制系统稳定性。
二、逐步排查与解决方法
步骤1:基础检查
– 确认设备状态:
检查操作面板有无报警代码,紧急停止按钮是否复位,安全防护罩是否关闭。
– 验证参数设置:
重新打开标刻软件,确保“激光功率”>30%、“标刻速度”与材料匹配,并加载正确的标刻文件。
步骤2:激光器检测
– 电源与散热检查:
1. 测量激光电源输出电压是否正常(参考设备手册标准值)。
2. 触摸散热器温度,若过热则检查水泵/风扇是否运转,清理散热口灰尘。
– 测试激光输出:
在软件中手动开启“激光测试”模式(部分设备需进入维护菜单),用亚克力板测试是否有微弱光斑。
步骤3:光路校准与清洁
– 红光校准:
1. 使用调光纸确认红光点与雕刻区域中心是否重合。
2. 通过调节红光指示器的螺丝,使其与主激光路径一致。
– 清洁光学元件:
1. 用无水乙醇与无尘棉签清洁反射镜、聚焦镜,按单一方向轻擦避免划伤镀膜层。
2. 检查镜片有无裂纹或烧蚀痕迹,必要时更换。
步骤4:控制信号排查
– 线路检测:
断开电源后,重新插拔控制卡与振镜、激光器的数据线,检查接口是否氧化。
– 替换测试法:
若条件允许,更换控制卡或振镜组件,判断是否为硬件故障。
步骤5:专业检修
– 激光器功率检测:
使用激光功率计测量实际输出能量,若低于额定值60%,需联系厂家更换激光模块。
– 振镜系统诊断:
通过控制软件驱动振镜绘制图形(如十字线),观察运动是否平滑,有无抖动或卡顿。
三、预防与维护建议
1. 日常维护
– 每日工作前清洁设备外壳与光学窗口,每月全面清理光路系统。
– 定期更换冷却水(水冷机型),建议使用去离子水并添加防藻剂。
2. 操作规范
– 避免长时间满功率运行,雕刻金属时采用分层加工模式。
– 标刻前确保工件平整,防止焦距突变损伤透镜。
3. 环境要求
– 保持工作环境温度10-35℃、湿度<70%,避免粉尘和油雾污染。
四、总结
红光不标刻问题多由激光器异常、光路偏移或控制信号中断导致。通过“参数检查→光路清洁→硬件检测”的流程可解决80%以上故障。若自行排查无果,需及时联系厂家技术支持,避免盲目拆机扩大损失。定期维护与规范操作是保障设备寿命的关键,建议建立维护记录表,追踪设备健康状态。
点击右侧按钮,了解更多激光打标机报价方案。
激光打标机红光和激光不重合
激光打标机红光和激光不重合
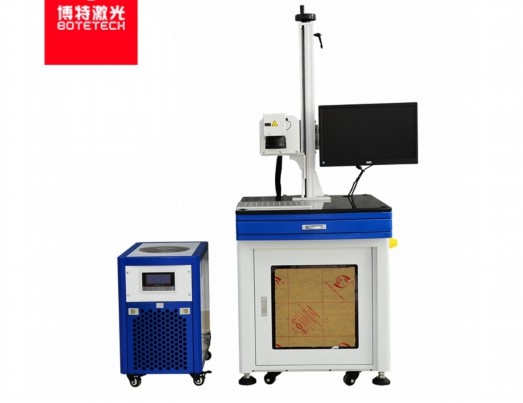
激光打标机红光与激光不重合问题的系统性分析与解决方案
一、问题概述
激光打标机作为精密加工设备,其红光定位系统与激光加工光束的同步性直接影响加工精度。当两者出现位置偏差时,会导致实际加工位置偏离预定坐标,严重影响产品质量。本文从技术原理、故障原因到解决方案进行系统阐述。
二、技术原理与偏差影响
1. 双光路系统构成:
– 可见红光(635-650nm):用于路径指示和定位预览
– 不可见加工激光(1064nm等):承担材料加工任务
2. 校准要求:
– XY平面重合误差应<0.05mm
– 焦点轴向偏差应<0.1mm
3. 偏差后果:
– 雕刻位置偏移
– 精密图案失真
– 批量加工一致性差
三、故障原因分析
1. 机械性因素(占比约45%):
– 运输震动导致光路组件位移
– 镜片支架螺丝松动(M3/M4规格螺丝扭矩异常)
– 振镜系统安装平面度偏差>0.02mm
2. 光学因素(30%):
– 扩束镜偏移(偏离率>0.5°)
– 聚焦镜片污染(透光率下降至<90%)
– 合束镜角度偏差(>0.3°)
3. 环境因素(15%):
– 工作温度波动>±5℃/h
– 设备基础共振频率<25Hz
– 粉尘浓度>100μg/m³
4. 电气因素(10%):
– 红光二极管供电不稳(电压波动>5%)
– 振镜电机反馈异常(编码器误差>2‰)
– 控制板信号延迟>5ms
四、系统化解决方案
1. 基础校准流程:
① 准备工具:
– 双面调光纸(建议3M 0.1mm厚度)
– 六角扳手套装(含0.9/1.3/1.5mm)
– 激光功率计(量程0-50W)
② 初步检测:
– 开启红光模式,观察光斑均匀性
– 测试激光模式,测量功率稳定性(波动应<3%)
– 检查各镜片表面清洁度(使用专业拭镜纸)
③ 分步校准:
步骤1:调整红光基准
– 松开红光模组固定螺丝(M4×8)
– 使用定位夹具保证与机架平行度<0.02mm
– 临时固定后测试5点定位精度
步骤2:校正扩束系统
– 调整扩束镜入射角度(精度需达0.01°)
– 测量输出光束直径(与理论值偏差<5%)
– 使用自准直仪检测光束平行度
步骤3:振镜同步校准
– 进入DAC软件调试模式
– 设置5点校正矩阵(建议间距≥100mm)
– 调整X-Y补偿参数(步进值0.001mm)
步骤4:焦点重合确认
– 使用CCD同轴监控系统
– 在Z轴方向每0.1mm截取光斑图像
– 通过图像分析软件计算重合度
2. 进阶维护措施:
– 建立光路校准日志(记录温度、湿度、振动值)
– 安装主动防震平台(推荐频率5-200Hz可调)
– 配置恒温系统(温度控制±1℃)
– 实施ISO 9013标准定期检测
五、预防性维护建议
1. 日常维护周期:
– 每日:清洁外部光路(使用无水乙醇)
– 每周:检查螺丝紧固度(扭矩0.6-0.8N·m)
– 每月:全面光路校准(含温度补偿)
– 每季:振镜系统轴承润滑(专用真空脂)
2. 环境管理标准:
– 温度:22±2℃
– 湿度:45±5%RH
– 洁净度:ISO Class 7
– 地基振幅:<2μm@10-100Hz
六、特殊情况处理
1. 材料适应性调整:
– 对高反材料(铜、铝等)需增加2-5%的补偿量
– 曲面加工时启用Z轴动态聚焦补偿
– 透明材料加工采用同轴视觉定位
2. 应急处理方案:
– 突发性偏差>0.1mm时:
① 立即停止加工
② 检查冷却系统(水温差应<2℃)
③ 排查气路压力(≥0.6MPa)
④ 进行快速三点校准
七、技术发展趋势
1. 智能校准系统:
– 集成机器视觉自动校准(精度0.005mm)
– 配备温度-振动联合补偿算法
– 开发基于大数据的预测性维护系统
2. 新型光路设计:
– 共光路一体化结构
– 自适应变焦系统
– 全息定位技术应用
本解决方案通过系统化故障诊断、标准化校准流程和预防性维护体系,可有效解决红光与激光不重合问题,提升设备加工精度和使用寿命。建议用户建立完善的设备健康管理系统,必要时联系专业技术人员进行深度维护。
点击右侧按钮,了解更多激光打标机报价方案。
免责声明
本文内容通过AI工具智能整合而成,仅供参考,博特激光不对内容的真实、准确或完整作任何形式的承诺。如有任何问题或意见,您可以通过联系1224598712@qq.com进行反馈,博特激光科技收到您的反馈后将及时答复和处理。