集成电路芯片切割机有什么功能
集成电路芯片切割机的功能与应用
集成电路芯片切割机是现代半导体制造工艺中的关键设备,主要用于将晶圆分割成单个芯片(Die)。作为半导体封装前道工序的核心装备,其性能直接影响芯片的良率、生产效率和最终产品质量。以下将详细阐述集成电路芯片切割机的主要功能及其在半导体制造中的重要性。
一、核心切割功能
1. 高精度晶圆分割
芯片切割机通过金刚石刀片或激光技术,沿着晶圆上的切割道(Scribe Line)进行精确分割。机械切割精度通常可达±1.5μm以内,激光切割精度更高,确保不会损伤芯片内部电路。
2. 多种切割方式
– 刀片切割:适用于大多数硅基材料,成本较低
– 激光切割:用于超薄晶圆或特殊材料(如GaAs、SiC)
– 隐形切割(Stealth Dicing):激光在晶圆内部形成改性层,然后通过扩展分离
3. 异形切割能力
先进的切割机可进行曲线切割和角度切割,满足特殊芯片设计需求,提高晶圆利用率。
二、辅助功能系统
1. 视觉定位系统
– 高分辨率CCD相机自动识别切割道和对准标记
– 图案识别技术补偿晶圆制备过程中的位置偏差
– 自动校准功能确保切割路径精确
2. 工艺控制功能
– 实时监控切割深度(通常控制在晶圆厚度的1/3-2/3)
– 自动调节切割速度(通常50-300mm/s可调)
– 刀片磨损检测与自动补偿
3. 清洁与冷却系统
– 去离子水喷射冷却切割区域
– 超声波清洗去除切割残留物
– 真空吸附保持晶圆稳定
三、先进技术功能
1. 超薄晶圆处理
可处理厚度25μm以下的超薄晶圆,配备特殊承载系统防止破裂。
2. 多层堆叠切割
支持3D IC等堆叠结构的精确切割,层间对准精度达±0.5μm。
3. 智能检测功能
– 切割前缺陷检测
– 切割后芯片质量自动分选
– 数据追溯与工艺分析
四、自动化与集成功能
1. 自动化物料处理
– 自动上下料系统
– 晶圆盒到盒传输
– 与前后道工序设备无缝对接
2. 智能制造接口
– SECS/GEM通信协议支持
– 物联网远程监控
– 大数据分析优化切割参数
3. 多工艺整合
部分高端机型集成切割、清洗、检测于一体,形成完整加工单元。
五、特殊应用功能
1. MEMS器件切割
针对微机电系统的特殊要求,提供低应力切割方案。
2. 功率器件加工
优化切割工艺减少碳化硅等宽禁带半导体材料的边缘缺陷。
3. 柔性电子切割
支持柔性基板的低温、低应力分割工艺。
六、总结
现代集成电路芯片切割机已从单一分割设备发展为集精密机械、光学检测、自动控制和智能算法于一体的高端制造系统。随着芯片尺寸不断缩小、3D封装技术普及和新型半导体材料应用,切割机正朝着更高精度、更低损伤、更强智能的方向发展,成为提升半导体产业竞争力的关键装备之一。未来,随着人工智能和物联网技术的深入应用,芯片切割机将进一步实现自主决策和预测性维护,为半导体制造提供更高效的解决方案。
点击右侧按钮,了解更多激光打标机报价方案。
相关推荐
晶圆切割方式有哪几种
晶圆切割方式有哪几种
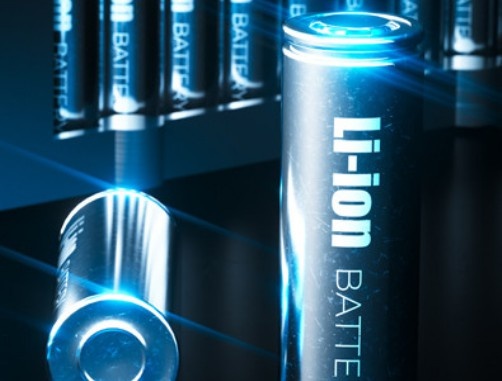
晶圆切割方式综述
晶圆切割(Wafer Dicing)是半导体制造中的关键工艺,用于将完成电路制作的整片晶圆分割成单个芯片(Die)。随着芯片尺寸缩小和材料多样化,切割技术不断演进,目前主要包括以下几种方式:
一、机械切割(Blade Dicing)
原理:使用高速旋转的金刚石刀片(转速30,000-60,000 RPM)对晶圆进行物理切割。
特点:
1. 适用材料:硅(Si)、砷化镓(GaAs)等传统半导体材料。
2. 优势:成本低、效率高(切割速度可达100-300 mm/s),适合大批量生产。
3. 局限性:
– 切割宽度(Kerf Width)较大(约20-50 μm),导致材料浪费;
– 机械应力易造成边缘崩裂(Chipping),影响良率;
– 不适用于超薄晶圆(<100 μm)或脆性材料(如玻璃、碳化硅)。 改进技术: - 阶梯切割(Step Cutting):分两步切割,先浅切后深切,减少应力。 - 激光辅助切割(Laser-Assisted Blade Dicing):用激光软化材料后再切割,降低崩边风险。 二、激光切割(Laser Dicing) 原理:通过高能激光(如紫外激光、皮秒激光)烧蚀或改性材料实现切割。 分类: 1. 烧蚀切割(Ablation Dicing):激光直接气化材料形成切割道,适用于有机材料或薄硅晶圆。 2. 隐形切割(Stealth Dicing): - 激光聚焦于晶圆内部,形成改性层(改质区),再通过机械扩展分离芯片; - 无粉尘、无热影响区(HAZ),适合超薄晶圆(如50 μm以下)。 特点: - 精度高:切割道宽度可控制在5-10 μm,节省材料。 - 无接触:避免机械应力,适合脆性材料(如SiC、GaN)。 - 挑战:设备成本高,切割速度较慢(约10-100 mm/s),需优化参数避免热损伤。 三、等离子切割(Plasma Dicing) 原理:利用反应离子刻蚀(RIE)或深反应离子刻蚀(DRIE)技术,通过化学腐蚀和物理轰击去除切割道材料。 特点: 1. 超窄切割道:宽度可小于5 μm,适合高密度集成芯片。 2. 无应力:避免机械损伤,良率高,尤其适用于MEMS器件。 3. 局限性: - 工艺复杂,需掩膜(光刻胶或硬掩膜)定义切割区域; - 设备昂贵,耗时较长(刻蚀速率约1-10 μm/min)。 应用场景:高端封装(如Fan-Out WLP)、射频器件(RF ICs)等。 四、水导激光切割(Water Jet Guided Laser Dicing) 原理:激光束通过高压水柱(直径约50 μm)引导至切割位置,结合了激光与水刀的优势。 特点: 1. 冷却效应:水柱带走热量,减少热影响区,适合热敏感材料。 2. 高精度:切割道窄(约20 μm),边缘质量优于纯激光切割。 3. 挑战:设备维护复杂,需处理水污染问题。 五、先进复合切割技术 为满足异质集成和3D封装需求,复合技术成为趋势: 1. 激光+机械切割:先用激光预处理切割道,再用刀片完成切割,平衡效率与质量。 2. DBG/SDBG技术: - 先划片后减薄(DBG, Dicing Before Grinding):切割部分深度后减薄晶圆,再裂片。 - 隐形划片后减薄(SDBG):结合隐形切割与DBG,用于超薄芯片(如CIS传感器)。 六、技术对比与选型要点 | 切割方式| 精度 | 速度 | 成本 | 适用材料 | 典型应用 | |-|-|-|-|--|--| | 机械切割 | 中 | 高 | 低 | Si, GaAs | 传统逻辑/存储芯片 | | 激光切割 | 高 | 中 | 高 | Si, SiC, 玻璃 | 薄晶圆、功率器件| | 等离子切割 | 极高 | 低 | 极高 | Si, 化合物半导体 | MEMS、射频芯片 | | 水导激光 | 高 | 中 | 高 | 热敏感材料 | 生物传感器| 选型考虑因素: - 材料特性:脆性材料优先选择激光或等离子切割。 - 厚度要求:超薄晶圆需无应力工艺(如隐形切割)。 - 成本与产量:机械切割仍是大规模生产的主流选择。 七、未来发展趋势 1. 异质集成驱动:针对SiC、GaN等宽禁带半导体,开发低损伤切割工艺。 2. 智能化升级:结合AI实时监控切割质量(如边缘缺陷检测)。 3. 绿色制造:减少切割粉尘(如干式激光切割)和化学废弃物。 总结 晶圆切割技术需根据材料、厚度、成本等需求综合选择。随着半导体器件多元化发展,复合切割和新型无应力技术将成为主流,推动芯片制造向更高集成度与可靠性迈进。
点击右侧按钮,了解更多激光打标机报价方案。
半导体切片机
半导体切片机
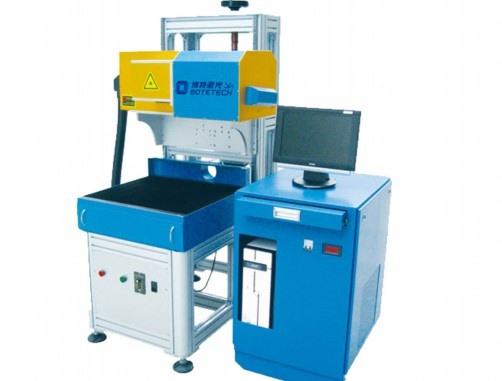
切割文明:半导体切片机与人类技术的精致化进程
在深圳一家晶圆厂的洁净车间里,一台价值数千万的半导体切片机正在安静地运作。金刚石刀片以每分钟数万转的速度旋转,将硅锭切割成厚度仅75微米的晶圆,相当于一根头发丝的直径。这种精度达到微米级别的切割工艺,是现代电子工业的基础。半导体切片机看似只是制造业中的一个专业设备,实则代表着人类文明从粗放走向精致的技术演进历程。从石器时代的简单敲打到今天原子级别的材料加工,切割技术的每一次突破都标志着人类控制物质世界能力的跃升。
人类切割技术的历史可以追溯到数百万年前。旧石器时代的原始人用燧石相互敲击,制造出粗糙的切割工具,这些简陋的石器帮助他们猎取食物、加工兽皮。考古学家在非洲发现的奥尔德沃石器,其边缘的微小磨损痕迹显示早期人类已经开始有意识地”设计”工具的切割功能。新石器时代,人类掌握了磨制技术,能够制作更精细的石刀和箭头。古埃及人用铜制工具切割石灰岩建造金字塔,中国商周时期的玉匠已经能够用解玉砂切割硬度极高的玉石。这些技术进步不仅满足了实用需求,更催生了早期艺术和宗教仪式中的精美器物。文艺复兴时期,达·芬奇设计的各种切割机械图纸,展现了人类对精密加工的早期构想。每一次切割技术的革新,都推动着文明向更精致的方向发展。
现代半导体切片机的技术突破集中体现了人类切割工艺的巅峰成就。1950年代,贝尔实验室的工程师首次用金刚石刀片切割硅晶体时,成品率极低,厚度控制困难。今天的半导体切片机采用纳米级金刚石颗粒镀层的超薄刀片,配合空气轴承主轴和精密伺服控制系统,能够实现亚微米级的切割精度。日本东京大学的研究团队开发的激光辅助切割技术,进一步将晶圆厚度减至20微米以下。这些技术进步的背后是材料科学、流体力学、振动控制和计算机模拟等多学科的协同创新。德国某精密机械公司研发的主动振动补偿系统,能够实时监测并抵消切割过程中的微小振动,其传感器灵敏度足以检测到单个细菌重量的变化。这种对”完美切割”的追求,正是人类技术精致化的生动体现。
半导体切片机的技术哲学意义远超其工业应用价值。法国技术哲学家贝尔纳·斯蒂格勒认为,技术是人类”外在化”的记忆和认知能力。从这个角度看,半导体切片机代表着人类将自身对物质世界的理解和控制能力推向了新高度。美国物理学家理查德·费曼在1959年提出的”底层充足空间”演讲中预见的纳米技术时代,正通过这类精密设备逐步成为现实。每一次切割精度的提升,都是人类突破物理限制、重新定义制造边界的尝试。日本工程师中村修二在开发蓝光LED时,正是因为改进了晶圆切割工艺,才实现了氮化镓晶体的高质量加工。这种技术进步与科学发现的互动,构成了人类认识世界和改造世界的双重奏。
半导体切片机的进化轨迹预示着未来技术发展的精致化方向。随着量子计算、柔性电子等新兴领域的兴起,对异质材料集成和三维结构加工的需求将推动切割技术向更精密、更智能的方向发展。美国麻省理工学院实验室正在研发的原子层刻蚀技术,可能最终模糊”切割”与”组装”的界限,实现在原子尺度上的材料重构。这种技术精致化的终极目标,或许是以最小的能量和物质消耗,获得最大的功能和价值产出,这与生态文明时代的技术伦理高度契合。从石器到硅片,人类切割技术的演进不仅改变了生产方式,更重塑了我们的思维方式和文明形态。在这条从粗糙到精致的道路上,半导体切片机只是一个中间站,它的真正意义在于向我们展示:人类对完美的追求永无止境,而每一次技术的精致化,都是向更高文明形态的迈进。
点击右侧按钮,了解更多激光打标机报价方案。
多线切割机
多线切割机
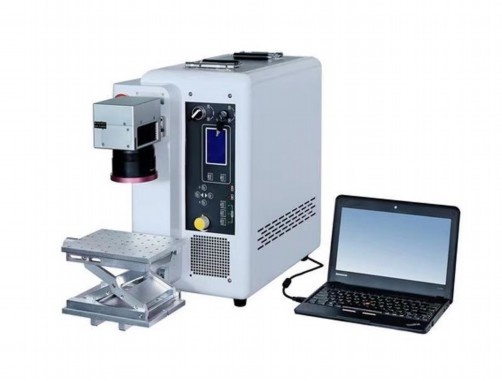
切割的暴力美学:多线切割机如何重塑工业生产的肌理
在当代工业生产的隐秘角落,一种看似简单却蕴含惊人力量的设备正悄然改变着制造业的基本面貌。多线切割机——这个由数百条细如发丝却锋利如刃的金属线编织而成的精密系统,正在以近乎暴力的优雅方式,重新定义着”切割”这一古老工业行为的极限。从单晶硅锭的完美剖开到超硬合金的精确成型,从太阳能电池板的基础材料到智能手机芯片的核心组件,多线切割机以其独特的工作原理和技术特性,在材料与精度之间架起了一座前所未有的桥梁,同时也重塑了工业生产的内在肌理。
多线切割机的核心魅力在于它将”暴力”与”精确”这对看似矛盾的特质完美融合。当数百条金刚石涂层的钢丝以每秒15米的速度同时运动,辅以研磨浆料的协同作用,这种切割过程本质上是一种受控的微观磨损——每平方毫米承受着数百牛顿的张力,每条钢丝每天可能经历数十万次的弯曲循环。这种高强度的工作状态,使得多线切割机能够轻松应对莫氏硬度高达9.5级的各类材料,包括令传统切割工具望而却步的单晶碳化硅和人造蓝宝石。在太阳能产业中,一台先进的多线切割机能在6小时内将直径8英寸、长2米的硅锭切割成2000片厚度仅160微米的硅片,每片的厚度偏差不超过±5微米。这种将宏观暴力转化为微观精度的能力,正是多线切割机最引人入胜的技术悖论。
多线切割技术的演进历程本身就是一部工业精密化的微缩史诗。20世纪50年代,美国晶体学家首次尝试用单根钢丝切割石英晶体时,切割精度尚以毫米计;而今天最先进的多线切割系统已能实现亚微米级的重复定位精度。这种跨越式发展源于多个关键技术节点的突破:1975年,往复式走线系统的发明使钢丝利用率提升300%;1992年,金刚石微粉镀层技术将钢丝寿命延长至500公里以上;2008年,伺服张力控制系统的应用将切割厚度偏差压缩到传统方法的1/20。特别值得一提的是,现代多线切割机采用的”主动式张力控制”技术——通过实时监测每段钢丝的张力变化并动态调整,确保切割过程中每根钢丝的张力波动不超过额定值的2%,这种对”力”的精妙掌控,正是实现超高精度切割的物理基础。
在光伏产业的爆发式增长中,多线切割机扮演了至关重要的”隐形推手”角色。2010年至2020年间,全球太阳能级硅片的平均厚度从180微米降至150微米,而破片率却从8%降至1.5%——这一看似矛盾的数据背后,是多线切割技术持续创新的直接结果。采用”自适应进给算法”的第五代多线切割机,能够根据硅锭的晶体取向自动优化进给速度和钢丝张力,使单位硅锭的出片量增加15%的同时,切割能耗降低22%。更令人惊叹的是,某些专用机型已实现”零损耗切割”——通过精确控制钢丝振动频率使其与材料固有频率错开,完全避免了边缘崩缺现象。这种将物理原理转化为生产效益的能力,使得多线切割机成为光伏产业降本增效的关键杠杆。
半导体领域对多线切割机的依赖则揭示了该技术的另一维度——洁净切割的极限挑战。当切割用于5纳米制程芯片的12英寸硅锭时,切割过程中产生的每个大于0.3微米的颗粒都可能造成价值数万美元的晶圆报废。为此,半导体级多线切割机发展出了”全封闭洁净切割系统”:采用离子化空气幕隔绝外部污染,切割区域保持ISO Class 3洁净度(每立方米空气中大于0.1微米的颗粒不超过1000个),甚至钢丝本身都需经过电解抛光达到表面粗糙度Ra<0.05微米。这种对"纯净"的极致追求,使得现代多线切割机已超越单纯的加工设备范畴,演变为集机械、材料、流体动力学和微污染控制于一体的复杂系统。 多线切割机的技术进化远未到达终点。在第三代半导体材料如氮化镓(GaN)、碳化硅(SiC)的加工领域,新型的"超声辅助多线切割"技术正崭露头角——通过给钢丝施加40kHz的高频振动,使研磨颗粒获得附加动能,切割效率提升70%的同时减少了亚表面损伤。另一方面,"智能钢丝"的研发可能引发下一轮革命:嵌入光纤传感器的钢丝能实时监测切割状态,结合AI算法实现真正的自适应切割。这些创新不仅延续着多线切割技术的生命力,更在不断重新定义"精密加工"的边界。 站在工业4.0的门槛回望,多线切割机的发展轨迹揭示了一个深刻洞见:当代工业进步的本质,往往不在于创造全新的加工原理,而在于将已知的物理过程推向极致的可控与精确。当数百条钢丝以人类头发1/10的精度同步运动,当每次切割同时产生数百万个微观相互作用却被完美掌控时,我们看到的不仅是一台高效的生产设备,更是人类将混沌的物理世界转化为可计算、可控制的工业秩序的非凡能力。这种能力,正是现代制造业最珍贵的核心资产。
点击右侧按钮,了解更多激光打标机报价方案。
免责声明
本文内容通过AI工具智能整合而成,仅供参考,博特激光不对内容的真实、准确或完整作任何形式的承诺。如有任何问题或意见,您可以通过联系1224598712@qq.com进行反馈,博特激光科技收到您的反馈后将及时答复和处理。