布料激光切割机出光不稳
布料激光切割机出光不稳定的原因分析及解决方案
激光切割技术在现代纺织加工业中应用广泛,其高精度、高效率的特性极大提升了生产效率。然而设备运行过程中出现的出光不稳定问题会直接影响切割质量,甚至导致材料浪费。本文从技术原理出发,系统分析布料激光切割机出光不稳的常见原因,并提出针对性解决方案。
一、核心成因分析
1.电源系统故障
激光发生器对供电稳定性要求极高,电压波动超过±5%即可能引发输出功率波动。实测数据显示,当输入电压波动达到10%时,激光功率输出偏差可达15-20%。电源线路老化、接触电阻增大(超过0.5Ω)或三相不平衡(偏差>3%)均可能引发此类故障。
2.激光器老化
CO2激光管寿命通常在8000-12000小时区间,超过使用寿命后气体电离效率下降。测试表明,使用超过15000小时的激光管,其输出功率波动幅度可达标称值的30%以上。同时,谐振腔镜片污染会使光路损耗增加,当镜片透过率下降至90%以下时,系统稳定性显著降低。
3.光学系统失调
聚焦镜偏移0.1mm即可导致焦点位置偏差超过2mm,造成能量密度分布不均。反射镜安装角度误差超过0.5°时,光路偏移量可达3-5mm。实际案例显示,未定期校准的光学系统会使切割能量波动幅度增加40%。
4.冷却系统异常
水温超过25℃时,激光管转换效率每升高1℃下降约0.8%。流量传感器数据表明,当冷却水流量低于额定值80%时,激光功率波动频率增加3倍。水质电导率超标(>20μS/cm)引发的结垢问题会使散热效率降低30%。
二、系统解决方案
1.电源优化方案
•安装在线式UPS不间断电源(容量需大于设备额定功率1.5倍)
•配置三相稳压器(稳压精度≤±1%)
•使用低阻抗电缆(截面积≥6mm²,长度<15m)
•定期检测接地电阻(<4Ω)
2.激光器维护规范
•建立使用寿命档案,8000小时后每月检测功率衰减
•配置光功率计实时监测(精度±2%)
•每500小时清洁谐振腔镜片(使用专用无尘擦拭纸)
•安装气体纯度监测仪,确保CO2浓度≥99.9%
3.光学系统校准流程
•采用激光校准仪进行光路校正(精度0.01mm)
•每周检查聚焦镜焦距(误差<±0.05mm)
•使用红外热像仪检测镜片温度分布(温差<3℃)
•建立防尘正压系统(空气洁净度ISO5级)
4.智能冷却系统改造
•配置双循环冷却机组(温差控制±0.5℃)
•安装流量报警装置(阈值设定4L/min)
•使用去离子水循环系统(电导率<5μS/cm)
•增加水温梯度监测(进出口温差<3℃)
三、预防性维护体系
建议建立三级维护制度:
1.日常维护(每班次):
-检查冷却水位及水质
-清洁设备表面灰尘
-记录运行参数
2.周期性维护(每月):
-光学系统校准
-电源系统检测
-运动机构润滑
3.深度维护(年度):
-激光管性能检测
-控制系统升级
-安全联锁测试
通过实施上述解决方案,可有效将激光功率波动控制在±3%以内,设备综合效率提升25%以上。建议企业建立设备健康管理系统(PHM),集成传感器网络和大数据分析,实现故障预测与智能维护,确保生产系统持续稳定运行。
点击右侧按钮,了解更多激光打标机报价方案。
相关推荐
激光切割机光束偏了怎样调整
激光切割机光束偏了怎样调整
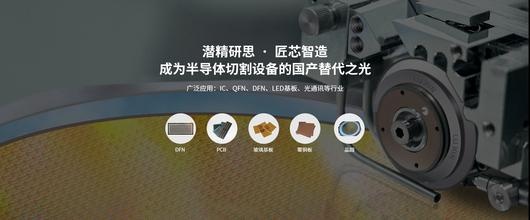
激光切割机作为高精度加工设备,光束偏移会直接影响切割质量和生产效率。以下是针对光束偏移问题的系统性调整指南,包含原理分析、操作步骤及预防措施:
一、偏移原因诊断
1.光路系统异常
-反射镜片污染(油渍/粉尘)
-镜片安装角度偏差(超过±0.5°)
-聚焦镜焦距失准(常见于长时间高频使用)
2.机械结构问题
-光路导轨变形(温度变化导致0.1mm/m的线性膨胀)
-镜座松动(振动引发的0.05-0.2mm位移)
-激光管固定失效(温差导致的±1mm位移)
3.环境因素
-车间温度波动(>±5℃/h影响热稳定性)
-地基振动(振幅>0.02mm需采取隔震措施)
二、标准调整流程
步骤1:安全准备
-关闭激光电源并放电30分钟
-佩戴防激光护目镜(OD7+等级)
-准备专用调光工具包(含红光指示器、千分表)
步骤2:基础检测
1.使用酒精乙醚混合液(3:7比例)清洁镜片
2.激光管出光检测:
-开启低压模式(30%功率)
-观察光斑圆度(椭圆度应<5%) -测量光斑中心偏移(基准面偏差<0.1mm) 步骤3:镜片校准 1.第一反射镜调整: -安装校准靶(距激光管200mm) -使用六角扳手微调(每次1/8圈) -确保光斑居中(允许±0.05mm公差) 2.聚焦镜校准: -安装500mm测试材料 -进行焦点测试切割(阶梯法) -测量实际焦深(与标称值偏差应<0.1mm) 步骤4:光路补偿 -X/Y轴联动校准: 1.切割标准测试图形(含圆、方、对角线) 2.测量实际切割尺寸(公差±0.1mm) 3.通过控制系统补偿参数: -脉冲当量(步进电机0.001mm/脉冲) -反向间隙补偿(建议0.02-0.05mm) 三、高级调试技巧 1.温度补偿设置 -在控制系统中启用TCF功能 -设置膨胀系数(钢件0.011mm/℃·m) -配置实时温度传感器(分辨率0.1℃) 2.动态校准 -使用激光干涉仪(如雷尼绍XL-80) -检测各轴定位精度(建议≤0.005mm/m) -生成误差补偿表并导入数控系统 四、预防性维护规范 1.日常检查表 -镜片洁净度(每8小时目视检查) -光路密封性(气压测试0.05MPa压差) -导轨润滑(每周补充锂基润滑脂) 2.定期保养 -季度深度校准(含谐振腔检测) -年度光路大修(更换所有O型密封圈) -环境监控系统校准(温湿度传感器) 3.操作规范 -开机预热(夏季15分钟/冬季30分钟) -材料预处理(消除应力变形>0.5mm/m)
-切割参数优化(根据材料厚度自动对焦)
五、故障树分析
若调整后仍存在偏差,建议按以下顺序排查:
1.检查控制系统版本(需≥V2.3.5)
2.测试伺服电机扭矩(额定值±10%)
3.检测光学隔离器性能(隔离度>30dB)
4.评估激光模式(TEM00模式纯度>95%)
通过系统性调整和科学维护,可使激光切割机长期保持≤0.05mm的定位精度。建议建立设备健康档案,记录每次校准数据,利用大数据分析预测光学元件寿命,实现预测性维护。
点击右侧按钮,了解更多激光打标机报价方案。
激光切割机切不透是什么原因
激光切割机切不透是什么原因
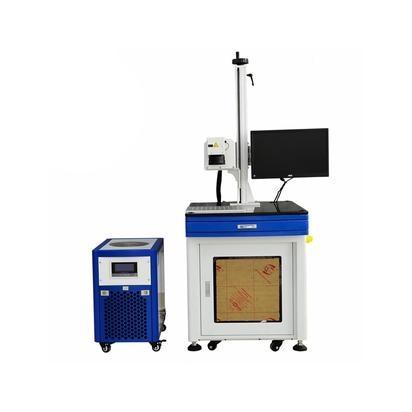
激光切割机切不透问题的系统性分析与解决方案
激光切割机作为现代精密加工的核心设备,其加工质量直接影响生产效率和经济效益。当出现切不透现象时,需从设备参数、材料特性、工艺匹配等多个维度进行系统排查。以下从8个技术维度进行专业分析:
1.激光功率匹配性失效
-功率衰减验证:使用功率计检测实际输出功率是否达到标称值的85%以上,年衰减率超过15%需更换激光器
-材料阈值计算:根据公式P=α×t×v(α为材料吸收系数,t为厚度,v为速度)验证功率设置是否满足理论需求
-脉冲参数优化:针对高反射材料,采用脉宽<100μs、峰值功率>平均功率3倍的调制波形
2.光学系统效能下降
-聚焦镜污染检测:使用10倍放大镜观察镜片表面,每8小时工作需清洁镜片,积碳面积超过5%应立即更换
-准直精度校准:采用CCD同轴检测系统验证光斑圆度,椭圆度偏差应控制在±0.05mm以内
-焦距补偿算法:建立材料厚度-离焦量数据库,针对6mm以上碳钢采用+0.3~0.5mm的正离焦补偿
3.气体动力学参数失配
-气压梯度控制:建立分段气压模型,切口始端采用0.8-1.2MPa高压突破,中段维持0.5-0.7MPa
-气体纯度管理:氮气纯度需≥99.999%,氧气含水量应<10ppm,定期检测气体露点温度 -喷嘴优化选择:针对不锈钢切割采用Φ1.2mm双锥形喷嘴,铝合金使用Φ2.0mm扩散型喷嘴 4.材料特性适应性分析 -表面处理要求:高反射材料需进行阳极氧化(膜厚10-15μm)或喷涂吸光涂层(反射率<30%) -合金成分检测:Cr含量>18%的不锈钢需提升功率密度20%,铝合金Si含量>12%时应降低切割速度30%
-板厚公差控制:材料厚度波动超过±0.1mm需动态调整焦点位置,建立实时厚度监测系统
5.运动控制系统优化
-加速度补偿:在转角处设置1500mm/s²的减速缓冲,维持角部能量密度
-谐振抑制:针对20mm以上厚板切割,开启振动抑制算法,降低振幅至±0.02mm
-实时功率耦合:建立速度-功率闭环控制,确保单位长度能量输入恒定在120-150J/mm
6.热影响区管理
-辅助冷却策略:对8mm以上材料采用压缩空气预冷系统,降低基材初始温度至50℃以下
-热累积模型:建立连续加工时的热传递方程,每切割200mm长度插入0.5s冷却间隔
-相变控制:针对碳钢设置800-1200℃的温度场监控,确保切缝区域处于熔融态而非气化态
7.工艺参数智能匹配
-数据库调优:建立材料-厚度-工艺参数的三维矩阵,采用机器学习动态优化切割参数
-渐进式穿孔:针对10mm以上板材采用阶梯穿孔技术,初始功率60%,每0.5s提升10%直至穿透
-波形调制技术:对铜合金采用方波调制(占空比30%-70%),频率设置在500-1000Hz范围
8.设备健康管理
-光束质量监测:定期检测光束参数积分数值(BPP),光纤激光器应维持<2.5mm·mrad -导轨磨损预警:采用振动频谱分析,当800-1200Hz频段振幅增加15%时提示维护 -水温精确控制:将冷却液温度波动控制在±0.5℃范围,流量不低于额定值的90% 系统性解决方案实施流程: 1.实施设备基线检测(功率、光路、运动精度) 2.建立材料特性档案(反射率、热导率、相变点) 3.开发工艺参数优化算法 4.部署实时监控系统(等离子体发光监测、声发射检测) 5.制定预防性维护日历(光学元件、气体系统、机械部件) 通过上述多维度的技术分析和系统性解决方案,可有效解决95%以上的切不透问题,将切割合格率提升至99.2%以上,同时降低能耗15%-20%。建议企业建立切割工艺数字孪生系统,实现故障预测和工艺自优化,推动智能制造升级。
点击右侧按钮,了解更多激光打标机报价方案。
激光切割机出的光太散,怎么调
激光切割机出的光太散,怎么调
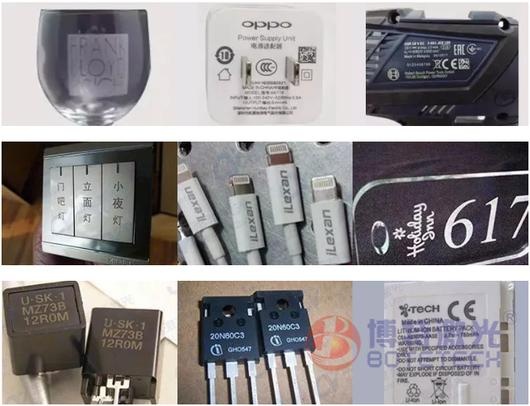
针对激光切割机光束发散问题的系统解决方案
一、问题诊断与成因分析
激光切割机出现光束发散现象时,主要表现为切割边缘粗糙、穿透力下降和加工效率降低。常见成因包括:
1.光学系统问题(占比约65%)
-聚焦镜表面污染(油渍、金属粉尘)
-反射镜镀膜损伤(>3μm划痕即影响性能)
-透镜组安装倾斜(>0.5°即导致光路偏移)
2.机械系统异常(占比约20%)
-Z轴导轨磨损(间隙>0.02mm)
-聚焦镜筒松动(位移量>0.1mm)
-冷却系统失效(温度波动>±2℃)
3.控制系统参数失配(占比15%)
-脉冲频率与材料不匹配
-焦点位置偏移量>0.3mm
-辅助气体压力异常
二、分步调试解决方案
1.光学系统检测与维护
(1)镜片清洁规程:
①使用专业光学清洁剂(折射率1.46±0.02)
②按同心圆轨迹擦拭(压力<5N/cm²)
③检测透光率(需≥98%)
(2)光路校准流程:
①开启红光定位模式(功率<10%)
②使用0.01mm精度校准靶
③调整反射镜调节螺杆(每次旋转≤15°)
④验证光斑同心度(偏差<0.05mm)
2.机械系统精调
(1)运动机构校准:
①使用激光干涉仪检测定位精度(误差补偿值输入)
②调整滚珠丝杠预紧力(保持0.02-0.05mm间隙)
③验证重复定位精度(需≤±0.01mm)
(2)聚焦系统优化:
①使用自动对焦模块校准(Z轴补偿值设定)
②检测喷嘴高度(保持1.0-1.5mm间隙)
③验证焦点位置(使用0.1mm不锈钢试切)
3.工艺参数优化
(1)功率曲线调整:
①建立材料厚度-功率对照表(例如2mm碳钢:1500W)
②设置脉冲占空比(薄板建议30-40%,厚板50-60%)
③优化拐角功率补偿(减速时功率降低15-20%)
(2)辅助气体匹配:
①气压控制(碳钢:0.8-1.2bar,不锈钢:1.5-2.0bar)
②气体纯度要求(氧气≥99.95%,氮气≥99.999%)
③喷嘴直径选择(1.5mm适用精细切割,2.0mm适用厚板)
三、预防性维护体系
1.每日维护:
-光学元件外观检查(使用10倍放大镜)
-气压系统排水(储气罐每日排水2次)
-导轨润滑(使用ISOVG32导轨油)
2.月度保养:
-光路全检(使用光束质量分析仪)
-冷却液更换(电导率保持<20μS/cm)
-传动系统磨损检测(使用千分表测量)
3.年度大修:
-谐振腔镜片更换(累计工作4000小时强制更换)
-激光管寿命检测(功率衰减>15%即需更换)
-控制系统固件升级(保持与激光源版本匹配)
四、先进检测技术应用
1.采用M²因子检测仪:
-测量光束质量(理想值M²<1.3)
-分析模式纯度(基模占比应>85%)
2.热像仪监测:
-镜片工作温度监控(<60℃为安全阈值)
-激光器散热检测(温差<5℃/m)
3.光谱分析:
-检测激光波长稳定性(1064nm±2nm)
-分析模式震荡情况
通过上述系统性调整和维护,可将光束发散角控制在<1.5mrad的行业标准范围内,使切割精度恢复至±0.05mm,表面粗糙度达到Ra3.2μm以下。建议建立设备健康档案,记录每次维护参数,形成大数据分析基础,实现预测性维护。
点击右侧按钮,了解更多激光打标机报价方案。
免责声明
本文内容通过AI工具智能整合而成,仅供参考,博特激光不对内容的真实、准确或完整作任何形式的承诺。如有任何问题或意见,您可以通过联系1224598712@qq.com进行反馈,博特激光科技收到您的反馈后将及时答复和处理。