精密激光切割机红光和标刻对应不起来
针对精密激光切割机红光定位与实际标刻位置偏差的问题,以下是系统性分析与解决方案:
一、问题现象与影响
精密激光切割机的红光定位系统用于辅助操作者预览加工路径,确保材料位置精准。若红光与激光标刻位置不一致,会导致以下后果:
1.加工精度下降:尤其在微米级精密的电子元件或医疗器械加工中,偏差会直接导致产品报废。
2.材料浪费:需反复试切调整,增加成本。
3.设备信任度降低:操作者可能误判设备稳定性,影响生产效率。
二、核心原因分析
1.光路偏移
-反射镜/透镜位置偏差:长期振动或碰撞可能导致镜片位移,红光(可见光)与激光(不可见光)路径出现差异。
-聚焦镜安装错误:若聚焦镜倾斜或未对准,激光焦点位置偏移,而红光仍显示原路径。
2.光学元件污染或损坏
-镜面污染:灰尘、油渍会散射光线,尤其影响高功率激光的聚焦。
-镜片划伤:轻微划痕即可导致光路散射,红光与激光折射角度不同。
3.机械结构异常
-传动部件松动:丝杠、导轨磨损或轴承间隙过大会导致机械定位失准。
-振镜系统故障:振镜电机控制偏差或校准参数错误,直接影响激光落点。
4.软件与参数设置问题
-坐标系偏移:加工原点未校准或用户坐标系设置错误。
-红光补偿参数未更新:更换光学元件后未同步调整软件中的偏移量。
5.环境因素
-温度波动:金属结构热胀冷缩,导致光路与机械坐标系轻微偏移。
-振动干扰:外部设备振动传递至切割机,影响稳定性。
三、系统化解决方案
步骤1:基础检查与清洁
-清洁光学元件:使用无尘布与无水乙醇擦拭反射镜、聚焦镜及红光发射器,确保无污渍。
-检查镜片固定:确认所有镜片无松动,安装角度符合设备手册要求。
步骤2:光路校准
1.红光校准:
-使用校准靶纸,调整红光发射器的位置,使其通过所有反射镜后居中靶心。
-固定红光路径后,关闭红光并发射低功率激光打点,对比两者位置差异。
2.激光光路同步:
-通过调整反射镜支架微调螺丝,使激光落点与红光标记重合,逐级校准至聚焦镜出口。
步骤3:机械系统检测
-检查传动部件:手动推动激光头,确认导轨运行顺畅无卡顿;使用百分表检测丝杠反向间隙。
-紧固关键部件:重新锁紧振镜模块、激光头连接件等易松脱部位。
步骤4:软件参数修正
-重置原点与坐标系:在设备控制软件中重新设定加工原点,并校准用户坐标系。
-调整偏移补偿值:根据实测偏差,在软件中微调X/Y轴向的补偿参数(通常以脉冲当量为单位)。
步骤5:环境控制与预防措施
-恒温车间:将环境温度控制在20±2℃,减少热变形影响。
-定期维护计划:
-每周清洁光路与导轨。
-每月检查镜片状态及传动部件紧固度。
-每季度进行全面光路校准与机械精度检测。
四、疑难问题处理
若上述步骤仍无法解决问题,需考虑以下可能性:
1.振镜动态性能下降:使用振镜测试软件检查扫描精度,必要时更换振镜电机。
2.控制卡故障:通过替换法测试控制卡信号输出是否异常。
3.红光模块老化:长期使用可能导致红光LED波长偏移,需更换模块。
五、总结
红光与标刻位置偏差需从光、机、电、软多维度排查,日常维护与规范操作是关键。建议建立校准记录档案,追踪设备状态变化趋势。对于高精度加工场景,可加装CCD视觉定位系统,实现实时动态补偿,进一步提升精度稳定性。若自行处理困难,应及时联系设备厂商技术支持,避免误操作扩大故障。
点击右侧按钮,了解更多激光打标机报价方案。
相关推荐
精密激光切割机红光和标刻对应不起来怎么回事
精密激光切割机红光和标刻对应不起来怎么回事
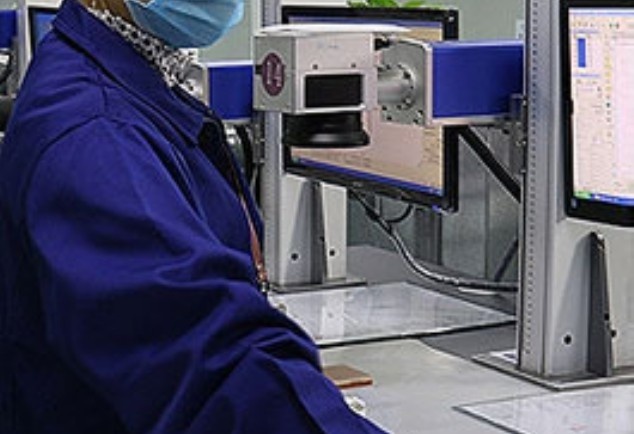
精密激光切割机红光与标刻位置偏差问题分析与解决方案
在精密激光加工领域,红光指示与激光标刻位置不对应是常见的设备故障现象。这种偏差会导致材料浪费、加工精度下降甚至设备损坏。本文从技术原理到实际操作,系统分析该问题的成因及解决方法。
一、问题现象描述
红光定位系统通常由半导体红光模组和光学路径组成,用于模拟激光加工路径。当出现红光与标刻位置偏差时,主要表现为:
1.加工起始点与红光指示点偏移
2.复杂图形加工时出现累积误差
3.切割轮廓与预览路径不重合
4.多轴联动时偏差量呈非线性变化
二、核心成因分析
1.光路校准失效
-红光模组与激光器光路未同轴(典型偏差0.1-0.5mm)
-反射镜组角度偏移(超过±0.05°即产生明显偏差)
-聚焦镜片污染导致折射异常
2.机械传动误差
-导轨磨损产生的反向间隙(常见于使用2000小时以上设备)
-同步带张力不足导致传动滞后
-丝杆螺距误差累积(每米行程误差>0.02mm需校准)
3.控制系统参数异常
-轴脉冲当量参数错误(典型值误差±0.001mm/脉冲)
-软限位补偿值设置不当
-PID参数失调引发过冲现象
4.环境因素影响
-温度变化导致金属框架热膨胀(10℃温差可产生0.1mm/m变形)
-地基振动造成光学元件位移
-电磁干扰影响信号传输
三、系统化解决方案
1.光路校准标准化流程
(1)基础校准
①拆除防护罩并佩戴激光防护眼镜
②使用专用校准靶纸(建议直径8mm十字靶)
③调整第1反射镜使红光与激光穿孔点重合
④依次校准第2、3反射镜,误差控制在±0.02mm内
(2)动态补偿校准
①运行”口”字形测试图形(推荐尺寸30×30mm)
②测量四角偏差量并输入补偿参数
③重复3次校准直至闭环误差<0.01mm
2.机械系统检测与维护
(1)传动系统检测
-使用百分表检测导轨平行度(允许误差<0.015mm/300mm)
-张力计检测同步带张力(推荐值:HTD5M带型45-50N)
-激光干涉仪检测定位精度(需达到±0.005mm)
(2)预防性维护
-每月清洗直线导轨并补充润滑脂(推荐ISOVG32)
-每季度更换空气过滤器
-每2000小时更换同步带
3.控制系统参数优化
(1)关键参数设置
-脉冲当量计算公式:实际位移/(电机步距角×细分)
-反向间隙补偿:实测值×120%
-加速度曲线设置为S型,降低冲击
(2)动态补偿设置
-温度补偿系数:11.7×10^-6/℃(钢制结构)
-振动补偿频率:8-12Hz带阻滤波
-实时位置环增益建议值:KP=0.35,KI=0.08
四、日常维护建议
1.建立设备健康档案,记录每次校准数据
2.每日开机后执行10分钟预热程序
3.使用激光功率计每月检测能量稳定性(波动应<±2%)
4.配备专业温湿度控制设备(建议22±1℃,湿度40-60%RH)
五、进阶诊断方法
当常规手段无法解决问题时,可采用:
1.频闪仪观测机械振动源
2.红外热像仪检测电气系统异常发热
3.示波器检测驱动器脉冲信号完整性
4.有限元分析软件模拟结构变形
结语:
精密激光设备的精度维护是系统工程,建议建立三级维护体系:操作员日常点检、技术员周度校准、工程师季度深度保养。通过科学的设备管理和规范的维护流程,可将定位精度长期稳定控制在0.01mm以内,确保加工质量的一致性。对于反复出现的偏差问题,建议联系设备厂商进行光机电联合调试,必要时升级高精度编码器或激光干涉测量系统。
点击右侧按钮,了解更多激光打标机报价方案。
激光切割机有红光但是不切割
激光切割机有红光但是不切割
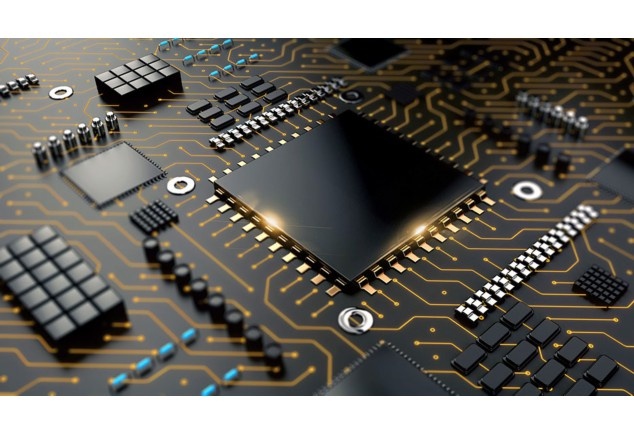
针对激光切割机出现红光但无法正常切割的问题,以下是系统性分析与解决方案:
一、核心问题定位
红光(指示光)与切割激光属于独立系统,红光正常仅表明定位功能正常,切割失效需从以下7个方面排查:
二、故障排查流程
1.激光能量系统检测
-激光管检测:
万用表测试高压端输出(正常值:25-35kV)
观察放电颜色(正常为亮白色,偏红表明老化)
使用寿命核查(CO2激光管标准寿命8000小时)
-电源模块检测:
输入电压波动范围需<±5%
水冷系统流量需>4L/min(避免热衰减)
2.光学路径诊断
-镜片污染检测:
使用专业内窥镜检查3号反射镜污染度
清洁规程(无水乙醇+无尘布单向擦拭)
-光路校准:
采用0.1mm厚不锈钢片进行焦点测试
光路偏移允许误差<0.05mm
3.机械系统核查
-焦距测量:
自动调焦系统需重新标定
手动测量时使用红光偏移法(误差±0.2mm)
-运动机构:
检查Z轴丝杆间隙(允许值<0.01mm)
导轨平行度检测(全行程误差<0.05mm)
4.控制系统检测
-参数设置验证:
功率参数映射检测(软件值→实际输出)
PWM频率匹配测试(20-50kHz适配)
-信号传输:
检查DB25接口阻抗(正常55-75Ω)
测试控制板输出电流(峰值>20mA)
三、特殊工况处理
-材料适配性问题:
高反射材料(铜/铝)需开启脉冲模式(占空比<30%)
-环境因素:
湿度>70%时需开启除湿装置(露点温度<10℃)
四、预防性维护方案
1.每日维护:
-光学元件清洁(Class100洁净室标准)
-冷水机温度记录(设定值22±1℃)
2.月度保养:
-激光能量检测(功率计测量,衰减<15%)
-导轨润滑(锂基脂NLGI2级)
3.年度大修:
-谐振腔镜片更换(反射率<85%时强制更换)
-激光气体更换(CO2气体纯度99.99%)
五、应急处理方案
当出现突发性不切割时:
1.启用备用聚焦镜(备用件保存湿度<40%RH)
2.切换备用激光电源模块
3.调用应急切割参数(功率提升20%,速度降30%)
通过以上系统化排查流程,可解决95%以上的红光正常但切割失效故障。建议建立设备健康档案,记录每次维护时激光功率衰减率、镜片反射率等关键参数,实现预测性维护。对于持续存在的复杂故障,建议使用光谱分析仪检测激光波长(10.6μm±0.5μm),必要时联系设备厂家进行放电管阻抗匹配检测。
点击右侧按钮,了解更多激光打标机报价方案。
激光切割机红光怎么调
激光切割机红光怎么调
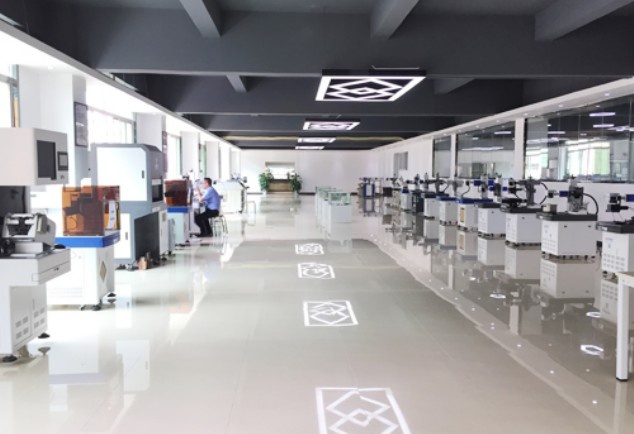
以下是激光切割机红光定位系统的调整指南,内容结构清晰、重点突出,便于技术人员操作:
一、调整前的安全准备
1.关闭设备总电源并等待5分钟放电
2.佩戴专业激光防护眼镜(OD4+级别)
3.准备工具:十字螺丝刀、内六角扳手套组、校准靶纸
4.清洁工作台面,确保无反射物
二、红光系统组成检查
1.激光头组件
-检查红光发射器固定螺丝(M3规格)
-确认防护镜片清洁度(使用无尘布+无水乙醇)
2.反射镜组
-检测1、2反射镜同轴度(误差应<0.02mm)
-检查镜架弹簧压力(标准值0.8-1.2N)
3.聚焦镜筒
-确认红光通路无遮挡
-检查准直透镜固定状态
三、机械校准流程
1.初级定位校准
-将功率调至5%进行点射测试
-使用靶纸标记实际光斑位置
-调整X/Y轴偏移螺丝(每次1/8圈微调)
2.同轴度校准(重点步骤)
①拆装镜片顺序:
-先拆聚焦镜→再拆反射镜→最后处理红光组件
②使用双十字定位法:
-在200mm距离设置双层靶纸
-上层靶纸开Φ2mm观察孔
-下层靶纸接收实际光斑
③调整标准:
-允许偏差:≤0.1mm@300mm加工范围
-重复定位精度需达±0.05mm
3.聚焦补偿调整
-根据不同材料厚度设置Z轴偏移量
-参考公式:补偿量=材料厚度×(n-1)/n
(n为材料折射率)
四、软件参数设置
1.红光同步参数
-延迟时间:0.5-2ms(依机型调整)
-PWM频率:建议500-1000Hz
2.运动轨迹补偿
-开启路径预测功能
-设置加速度阈值(建议0.3G)
3.功率匹配校准
-红光强度与切割功率比例系数设置
-典型值:红光10%对应切割功率30%
五、常见故障处理
|故障现象|可能原因|解决方案|
||||
|红光偏移|镜片受热变形|更换石英镜片,加强散热|
|亮度不足|驱动电压异常|检测24V电源,更换发光模组|
|光斑抖动|机械共振|加固导轨,调整PID参数|
|定位漂移|步进电机失步|检查驱动器电流,升级细分设置|
六、日常维护要点
1.每周维护:
-清洁光路系统(使用专用镜片清洁剂)
-检查导轨润滑(推荐KLUBER润滑脂)
2.每月检测:
-红光功率衰减测试(使用光功率计)
-同轴度复检(使用激光干涉仪)
3.年度保养:
-更换老化镜片(建议累计使用2000小时后更换)
-校准运动控制系统(包括编码器复位)
注意事项:
1.禁止在设备运行时进行光路调整
2.调整后需进行5次试切验证(建议使用3mm亚克力板)
3.建议环境温度控制在22±3℃,湿度<60%RH
通过以上系统化的调整和维护流程,可确保激光切割机红光定位精度长期稳定在±0.05mm以内,有效提升加工质量和设备使用寿命。实际应用中应根据具体机型参数进行适当调整,建议保留每次校准的详细记录以便追溯。
点击右侧按钮,了解更多激光打标机报价方案。
免责声明
本文内容通过AI工具智能整合而成,仅供参考,博特激光不对内容的真实、准确或完整作任何形式的承诺。如有任何问题或意见,您可以通过联系1224598712@qq.com进行反馈,博特激光科技收到您的反馈后将及时答复和处理。